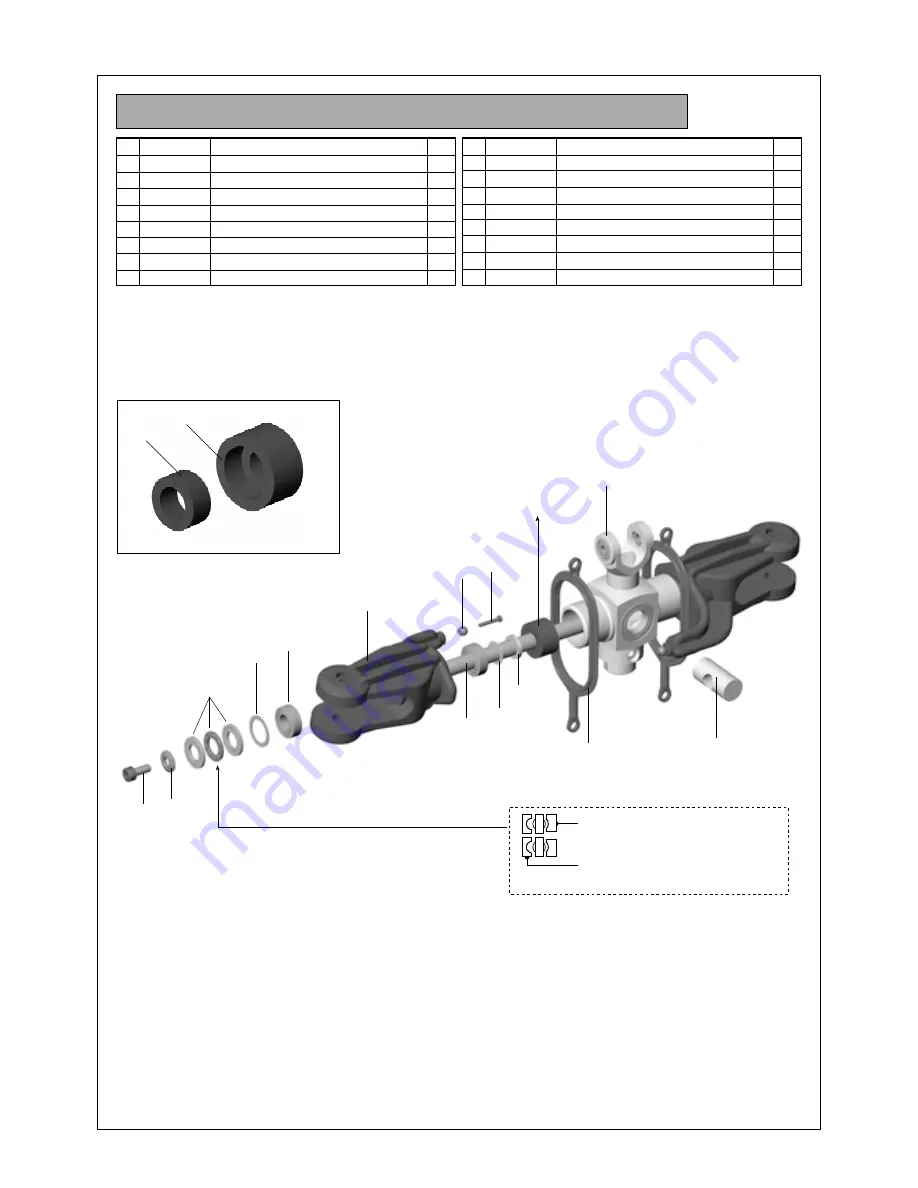
1
5
7
MAIN FRAME ASSEMBL
Y
8
9
1-1-1 Pinion Gear Subassembly
1
1
13
14
15
16
17
18
19
20
21
22
25
26
27
29
30
33
34
36
35
31
37
38
39
40
4
1-3-1 Rod Guide Collar Subassembly
1-5-1 Aileron Lever Subassembly
1-5-2 Metal Elevator Parallel Lever Subassembly
1-5-3 Elevator Control Lever Subassembly
1-5-4 Pitch Control Frame Subassembly
1-1-4 Elevator Control
Arm Subassembly
1-6-1 Wash Out Subassembly
ROTOR HEAD ASSEMBLY
T
AIL ASSEMBL
Y
3-1-1 T
ail T
ransmission Subassembly
FINAL ASSEMBL
Y
4-3-1 Skid Subassembly
4-4-1 Tail Support Subassembly
INSTALLATION OF PERIPHERAL EQUIPMENT
5-4-1 Body Subassembly
No.
Material No.
Description
Qty
.
1
HMC3-10B
Socket Screw M3x10
4
2
HMC3-12B
Socket Screw M3x12
21
3
BK0087
W
asher d3xD8x1.4
22
4
BK0274
T
ank Rubber Grommets
4
5
BK0380
Rear Frame L
1
6
BK0381
Rear Frame R
1
7
BK0629
W
asher
4
No.
Material No.
Description
Qty
.
1
HME3-18.5B
Set Screw M3x18.5
2
2
HMC3-25B
Socket Screw M3x25
10
3
BK0087
W
asher d3xD8x1.4
10
4
BK0103
Body Fitting Post
2
5
BK0658
Frame Spacer S
2
6
1-1
Upper Frame
Assembly
1
7
1-2
Lower Frame
Assembly
1
8
1-3-1
Rod Guide Collar Subassembly
2
No.
Material No.
Description
Qty
.
1
BK0389
Rod Guide Collar
1
2
BK0658
Frame Spacer S
2
No. Material No. Description
Qty.
1
BK0667
Servo Frame
1
2
HSE3-12B
M3x12 Self-Tapping Screw
6
3
1-3
Main Frame Assembly
1
No. Material No. Description
Qty.
1
HMC2-6B
Socket Screw M2x6
1
2
HMC3-10B Socket Screw M3x10
1
3
HMC3-25B Socket Screw M3x25
1
4
HME3-3B
Set Screw M3x3
1
5 HMJ3-20N Self-Tapping Screw M3x20 2
6
HMS4
E Ring
1
7
HMY2-10
Pin 2x10
1
8
BK0086
Ball link 4.8x20
2
9
BK0088
Washer d3xD5x0.5
3
No. Material No.
Description
Qty.
1
HMJ2-10N
Self-Tapping Screw M2x10
2
2
HMV840ZZY BRG d4xD8X3
2
3
BK0075
Link Ball 4.8
2
4
BK0340
Aileron Control Arm
1
No. Material No. Description
Qty.
1
HMJ2-10N
Self-Tapping Screw M2x10
2
2
HMV840ZZY BRG d4xD8X3
2
3
BK0075
Link Ball 4.8
2
4
BK0340
Aileron Control Arm
1
No. Material No.
Description
Qty.
1
BK0876
Elevator Control Arm
1
2
BK0075
Link Ball
φ
4.8
1
3
HMF2-8N
Philip Machine Screw M2x8
1
No. Material No.
Description
Qty.
1
BK0882
Elevator Push Pull Lever
1
2
HMV840ZZY BRG d4xD8x3
2
3
BK0075
Link Ball
φ
4.8
3
4
HMJ2-8N
Selfing-Tapping Screw M2x8
3
5 BK0410
Collar d3xD4x13
1
No.
Material No.
Description
Qty
.
1
HMS15
E Ring
4
2
BK0880
Elevator Link Shaft
2
3
BK0455
Metal Elevator Control
Arm
1
4
BK0663
Elevator
Arm Link
2
No. Material No. Description
Qty.
1
BK0093
Link Rod 2x46
2
2
BK0086
Ball Link 4.8x2.0
4
3
BK0547
Hardened Main Shaft
1
4
BK0234
Lock Ring
1
5
HSA3-6B
Button Head Socket Screw M3x6
2
No. Material No. Description
Qty.
1
HMJ2-10N
M2x10 Self-Tapping Screw
2
2
HMC3-12B Socket Screw M3x12
2
3
HMV840ZZY BRG d4xD8x3
4
4
BK0088
Washer d3x5x0.5
2
5
BK0472
Washout base
1
6
BK0342
Flybar Control Lever
2
7
BK0343
Washout Link
2
8
BK0075
Link Ball
φ
4.8
2
9
BK0409
Collar d3xD4x7
2
10
BK0487
Pin
2
11 HMS15 E Ring
2
No. Material No. Description
Qty.
1
BK0086
Ball Link
φ
4.8
4
2
BK0292
Link Rod 2.3x24
2
3
BK0408
Collar d3xD4x5.5
2
4
BV0549
Washout Base Guidance Ring
1
No. Material No. Description
Qty.
5
HMC3-10B
Socket Screw M3x10
2
6
HMC3-12B Socket Screw M3x12 1
7
2-1-1
Flybar Seesaw Subassembly
1
8
2-1-2
Metal Main Rotor Hub Subassembly
1
No.
Material No.
Description
Qty
.
1
HMV740ZZ
BRG d4xD7x2.5
2
2
HMV1350
BRG d5xD13x4
2
3
HMV6701ZZY
BRG d12xD18x4
2
4
HMJ2-8N
Self-T
apping Screw M2x8
1
5
HMC3-10B
Socket Screw M3x10
3
6
HMJ3-20N
Self-T
apping Screw M3x20
1
7
HME3-4B
Set Screw M3x4
1
8
HMM3Z
Locknut M3
3
9
BK0075
Link Ball 4.8
1
No.
Material No.
Description
Qty
.
1
HMC3-30B
Socket Screw M3x30
2
2
HMC3-14B
Socket Screw M3x14
2
3
HMM3Z
Locknut M3
4
4
BK0086
Ball Link 4.8x20
2
5
BK0278
Machined W
asher
2
6
BK0403
Rod Guide
4
7
BK0404
T
ail Rotor Blade
2
No.
Material No.
Description
Qty
.
8
BK0877
3D V
ertical Fin
1
9
BK0650
T
ail Boom
1
10
BK0707
Rear Servo Rod
1
1
1
BK0347
T
ail Push Rod
A
1
12
BK0653
T
ail Push Rod B
1
13
3-1-1
T
ail
T
ransmission Subassembly
1
14
3-1-3
T
ail Drive Shaft Subassembly
1
No.
Material No.
Description
Qty
.
1
BK0617
Bolt M4x25
1
2
BK0086
Ball Link 4.8x20
4
3
BK0318
Link Rod 2.3x95
2
4
HMM4Z
Locknut M4
1
5
2-1
Rotor Head
Assembly
1
No. Material No.
Description
Qty.
1
HME4-5B
Set Screw M4x5
4
2
BK0397
Skid Brace
2
3
BK0398
Skid Pipe End Cap
4
4 BK0668 Skid Pipe 2
No. Material No. Description
Qty.
1
5-4-1
Body Subassembly
1
No. Material No. Description
Qty.
1
HMJ2-6B
M2x6 Self-Tapping Screw
6
2
HSE3-12B
M3x12 Self-Tapping Screw
2
3
BK0102
d3xD6x11Grommet
2
4
BK0098
Body Clip A
1
5
BK0099
Body Clip B
1
6
BK0429
Body
1
7
BK0428
Canopy
1
8
JV0186
Decal
1
9
BK0473
Body Support
1
10
BK0474
Rubber CAP
2
11
HNLR6
R Pin
2
No. Material No.
Description
Qty.
1
*****
Main Rotor Blade
2
2
BK0446
Rotor Bolt M5x35
2
3
HMM5Z
Locknut M5
2
T
ABLE OF CONTENTS
REP
AIR AND REPLA
CEMENT P
AR
TS
Purchase replacement parts from the hobby shop where you have purchased the Raptor 90
3D
. Please contact
the
Thunder
T
iger distributor in your country
, and the distributor can tell you where to obtain the parts. For example,
in the U.S, all
Thunder
T
iger products are distributed by
Ace Hobby Distributors. On the web site www
.acehobby
.com,
there is a list of all the hobby shops in the USA
that can order any
Thunder
T
iger parts from
Ace for you.
T
echnical
questions regarding the Raptor will be answered quickly by sending an email to service@acehobby
.com or call
T
echnical Support at 949-833-7498. In Europe,
Asia and
Australia, please contact the distributor in your country
.
W
ARNING
T
o ensure safety
, please read the instruction manual thoroughly before assembly
. Radio control helicopters are
sophisticated equipment, and not toys. Radio control model helicopters are capable of causing serious bodily injury
if not properly assembled or operated.
The manufacturer and distributors assume no liability for damages that could
occur from the assembly or use of this product.
This product is designed for hobby use only
. Operating model
helicopters requires diligence and skill.
The best way to ensure quick and successful learning is to seek help and
guidance from accomplished pilots. It is strongly recommended to join the appropriate radio control modeling governing
society in your country
. For example, in the United States, it is strongly encouraged to join the
Academy of Model
Aeronautics.
AMA
is a nonprofit organization that provides members in the United States with liability insurance
and monthly modeling magazines. For further information or to find a model helicopter club, please contact
AMA
at:
Academy of Model aeronautics
515 East Memorial Drive
Muncie, IN 47302
USA
(317) 287-1256
W
e also encourage you to subscribe to dif
ferent radio control helicopter magazines and learn about RC flying events,
new flying techniques, safety procedures, and hints. Rotory Modeler is a bi-monthly and Model Helicopter
T
echniques
is a quarterly newsletter published in the USA. Model Helicopter W
orld is a month magazine published by
T
raplet
Publication in England and sold worldwide. Rotor is a monthly German magazine. Helico is a Swiss quarterly
magazine.
A
TTENTION
W
e are unable to accept replacement or return of this model after it has been used or assembly has begun.
It is legally prohibited to duplicate or reprint this manual in any format without a written permission from the
manufacturer
.
The manufacturer has the right to make changes to this model or instruction without notice.
W
e have done our best to the accuracy of information in this manual. If you are aware of any mistake, we welcome
you to notify us.
W
e will not accept any responsibility for any accident, breakdown, fault or trouble caused by improper usage of
this model. Please thoroughly inspect your model and range check the radio before flight. Please keep the model
in its best condition in order to enjoy it.
This model does not include all the items necessary for flying, such as engine, serevos, gyro...etc.
It is dif
ficult for beginners to fly RC helicopters by themselves. It is highly recommended that beginners seek the
help of experienced RC helicopter pilots. W
e recommend beginners start with an inexpensive model such as the
Thunder
T
iger Raptor 30 that is also designed by Mr
.
T
aya.
RC helicopters are not toys.
The manufacturer does not assume the liability for any property or bodily damage
caused by the model or the operator
.
OTHER ITEMS REQUIRED
6
BODY SUPPORT INSTALLATION
Insert the aluminum support
tube through the servo frame.
Insert the "R" pins through the
two holes in the support tube
to prevent the tube from
moving in the servo frame.
Install two rubber ends onto
the support tube. The rubber
ends will dampen shake or
vib rati on gener ated by the
engine.
Glow Plug W
rench
12V Battery
1.5V Glow Starter
(1.2V~1.5V)
Rubber Band
(Included)
Foam
Remote Glow Plug
Extension
1-2-2 Cooling Fan Casing Subassembly
1-2-3 Fuel T
ank Subassembly
No.
Material No.
Description
Qty
.
1
BK0062
Fuel
T
ank Stopper
1
2
BB0374
Silcon
T
ube (L=105mm)
1
3
BK0445
Fuel Plug
1
4
BK0463
Fuel
T
ank Nipple
1
5
BK0503-1
Fuel
T
ank
1
6
BE1867
Clunk W
eight
1
1-5-5 Header Tank Subassembly
No. Material No. Description
Qty.
1
HMC3-25B
Socket Screw M3x25
1
2
BK0087
Washer d3xD8x1.4
1
3
BV0502
Header Tank
1
4
BK0506
Tank Mount
1
5
BK0698
Header Tank Supporter
1
The Raptor 90 3D kit includes a header fuel tank that can be
attached to the right of the side frame.
23
2-1-1 Flybar Seesaw Subassembly
24
2-1-2 Metal Main Rotor Hub Subassembly
2
4.Final Assembly
----------------------------------------------------------------------------------------------
29
4-1 Installation of Rotor Head (Bag H)----------------------------------------------------------------------
30
4-2 Installation of Engine --------------------------------------------------------------------------------------
31
4-2-1 Engine Subassembly -------------------------------------------------------------------------------
32
4-3 Installation of Landing Skid-------------------------------------------------------------------------------
33
4-3-1 Skid Subassembly -----------------------------------------------------------------------------------
33
4-4 Installation of Tail Assembly -----------------------------------------------------------------------------
34
4-4-1 Tail Support Subassembly------------------------------------------------------------------------
34
5.Installation of Peripheral Equipment
-----------------------------------------------------------
35
5-1 Installation of Servo - Part 1 (Bag I) ------------------------------------------------------------------
36
5-2 Installation of Servo - Part 2 (Bag I) ------------------------------------------------------------------
37
5-3 Installation of Receiver and Gyro ----------------------------------------------------------------------
38
5-4 Installation of Body (Bag J) ------------------------------------------------------------------------------
39
5-4-1 Body Subassembly ----------------------------------------------------------------------------------
39
5-5 Installation of Rotor Blades (Bag K) -------------------------------------------------------------------
40
6.Settings
---------------------------------------------------------------------------------------------------------
41
6-1 Setting up Gear Backlash -------------------------------------------------------------------------------
42
6-2 Setting up of Stabilizer Paddles ------------------------------------------------------------------------
43
6-3 Setting up of Blade Pitch Angle -----------------------------------------------------------------------
43
6-3-1 Collective Travel for Hovering ------------------------------------------------------------------
44
6-3-2 Collective Travel for 3D ---------------------------------------------------------------------------
44
6-3-3 Configuring the Raptor 90 for 3D ---------------------------------------------------------------
45
Attention
--------------------------------------------------------------------------------------------------------------
46
7.Parts List Section
-------------------------------------------------------------------------------------------49
Raptor 90 3D Exclusive Parts --------------------------------------------------------------------------------
50
Raptor 90 3D Spare Parts List -------------------------------------------------------------------------------
55
Raptor 90 3D Optional Parts List ----------------------------------------------------------------------------
61
3
Thank you very much for purchasing the
Thunder
T
iger Raptor 90 3D R/C helicopter
.
The design of Raptor
90 3D is based on the original Raptor 90 series helicopter and modified for extreme aerobatics. It has all
needed must-have optional parts for 3D flying, such as metal main rotor hub, non-linear flapping damper
,
metal BRG, 3D light paddles and so on. It also adopts the push-pull control system on collective pitch
and elevator to achieve the most precise control.
The flybar ratio is changeable to fit all kinds of flying
style. Use of high quality material make the helicopter one tough machine that can handle everyday 3D
beating. Raptor 90 3D is born for 3D flying, and you don
’
t have to do any further modification for aggressive
3D maneuver
.
This is by far the best machine you have never seen. Just enjoy the model and have fun.
UNIQUE SIDEFRAME SYSTEM
Aluminum side plates are used in conjunction with molded material to construct the main structure.
This
design produces minimum weight with maximum strength. If the sideframes were completely made of
molded material, then to achieve equal strength the plastic would have to be very thick and heavy
. Using
molded material at the right place avoids using metal angle brackets or putting compound bends in metal
frames. Slots have been added in the frame design to permit the use of optional gear ratios to optimize
engine performance to suit any pilot's demand.
BELL-HIILLER MIXING CONTROL UNIT
Main rotor control geometry has been carefully engineered to minimize cross-coupling in collective and
cyclic commands. Blade pitch arms and the Bell-Hiller mixing arms are designed at an angle such that
the pushrod interlinking them are at 90 degrees when the blades are at 0 degree.
The pilots will get the
symmetrical cyclic control feel and flybar authority either at +10 or -10 degrees of collective. W
e design
this system with the 3-D pilot in mind. W
e guarantee you this whole design philosophy provides a strong
and accurate control mechanism.
SHAFT DRIVE T
AIL RO
T
OR
The Raptor 90 3D is designed with a constant drive tail rotor system to permit full tail rotor control during
autorotations. 180 autos, backward autos and pirouette autos are all within your reach now
. It has the
same aluminum torque tube system as the
Thunder
T
iger/T
aya Imperio helicopter
.
This allows obtaining
the maximum performance from any modern heading lock gyros.
3D CAD DESIGN
W
e use the latest 3D Computer
Aided Design to design and manufacture the Raptor 90 3D. Our high-
tech CAD program allows simulation of all moving parts to ensure no interference.
The analysis automatically
analyze the weight, the mass distribution, and inertia to help us pursue a design that will provide the high
level of maneuverability needed for all-out 3-D aerobatics.
INTRODUCTION
Socket Drivers
Hex W
rench
Grease
Blue Loctite
Instant Glue
Hobby Knife
Metric
4-way W
rench
Scissors
Diagonal Pliers
Open End
W
rench
5.5mm
Needle Nose Pliers
Screw Driver
7mm
5.5mm
7mm
8mm
5.5mm
7mm
8mm
10mm
Epoxy
Ball Link Pliers
No.
Material No.
Description
Qty
.
1
HMV6800ZZY
BRG d10xD19x5
1
2
HME4-5B
Set Screw M4x5
2
3
HMS5
E Ring M5x8
1
4
HMV696Z
BRG d6xD15x5
1
5
BK0388
Clutch BRG Case
2
6
BK0659
Frame Space M
4
7
BK0594
Starter Coupling
1
8
BK0592
Starter Shaft
1
9
BK0422
Drive Pinion 1
1T
1
10
BK0366
Pinion Gear Nut
1
1
1
BV0522-2
Clutch Bell Set
1
No.
Material No.
Description
Qty
.
1
HMC3-10B
Socket Screw M3x10
2
2
HMC3-12B
Socket Screw M3x12
4
3
BK0087
W
asher d3xD8x1.4
6
4
BK0393
Pitch Frame Cross Member
1
5
BK0394
Pitch Frame Cross Member Nut
2
6
BK0375T
Upper Frame
2
No. Material No.
Description
Qty.
1
HMM3Z
Locknut M3
4
2
HMC3-25B
Socket Screw M3x25
4
3
BK0820BL
Landing Skid Damper
4
4
4-3-1
Skid Subassembly
1
No. Material No.
Description
Qty.
1
HMC3-8B
Socket Screw M3x8
4
2
HMQ16
Retaining Ring
1
3
BK0357
Tail Drive Spur Gear 83T
1
4
BK0359
One Way Clutch Shaft
1
5
BV0368
Auto Rotation Hub
1
6
BK0356
Main Spur Gear 91T
1
1-6-2 Main Gear Subassembly
(3)
(2)
(4)
(6)
(5)
(1)
The carbon rear servo plate is secured
by two Lower 3mm bolts from the plastic
tail boom bracket.
10
1-1-2 Pitch Guide L
Subassembly
1-1-3 Pitch Guide R Subassembly
No.
Material No.
Description
Qty
.
1
BK0384
Pitch Guide Collar L
1
2
BK0658
Frame Spacer S
2
3
BK0693
Cross Member
1
The side with a number should face
in because the opening on both sides
are dif
fereent.
The hole on the plastic control arm has different
opening sizes on the two sides. Always snap the
bigger opening to the ball on swashplate gently and
afterward please check to make sure it is securely
attached and there is no damage or cracking.
INSTALLATION OF THE LINKS
Bigger Hole Face to Swashplate
Extended 6mm Hex
Starting
T
ool
Fuel Pump
Heli Engine (90size)
9609 PRO-90H(R)
Glow Fuel(15%-30%)
Glow Plug
Hi-torque 12V Electric starter
Receiver
T
ransmitter
(helicopter type, 6 or
more channels)
High Speed/T
orque Servo x 4
Rudder Servo x 1
Battery
Switch harness
Heading Lock
Gyro
In order to enjoy a safe and enjoyable experience, please read the manual carefully and completely understand
the helicopter structure and operation before the first flight.
Read the warnings to avoid injuries to you and others.
W
ARNING
–
The following could cause heavy injury or death if used incorrectly
.
Keep the model away from other people or animal when starting the engine.
Do not fly any model helicopter near or above people or cars. Models can sometimes lose
control due to pilot or mechanical failure.
W
ARNING
–
The following could also cause serious injury or death if not careful.
T
ake precaution with model fuel. Model engine glow fuel is highly flammable.
Please check the model carefully before each flight. Make sure that nothing has loosened up
or come apart.
Make sure everything moves freely without binding or excessive friction.
Do not operate the model in rain, snow
, thunderstorm, or adverse weather
.
W
ARNING
–
The following could also cause serious injury or death if not careful.
Please make sure that your radio frequency is not used before flight. If someone else is flying
with the same frequency as your radio, do not turn on your transmitter
. Otherwise, it can cause
a crash and even bodily and property damages.
Please monitor the fuel level during flight and land before running out of fuel.
Before each flight, please check that all servos and controls move properly
.
Do not modify any parts or use other than genuine
Thunder
T
iger parts.
Do not fly in places that are forbidden by law
.
Use Loctite on screws that do not use a locknut.
When operating the model, please beware that no loose cloth or jewelry can get entangled in
the model helicopter
.
Make sure the transmitter and receiver switches are on before starting the engine.
Do not touch the engine or the muf
fler right after flying because they are very hot.
Do not use this model for anything other than hobby
.
W
ARNING
–
The following damages can happen to the model.
Do not leave the model in a car for a long time.
The heat in the summer or the cold in the
winter and the humidity can cause damage to the model.
Be careful and watch the sharp edges and corners on the model.
BUILDING HINT
–
The instruction is divided into six assembly chapters:
Main Frame, Rotor Head,
T
ail Rotor
, Final
Assembly
, Radio Installation, and Settings.
There
are many major assembly steps in each chapter
, please follow the instruction to do each "
Subassembly" first, then combine the subassemblies into a major assembly
.
Upper Frame Assembly
Lower Frame Assembly
12
1-2-1 T
ail Drive Unit Subassembly
No.
Material No.
Description
Qty
.
1
HME3-4B
Set Screw M3x4
2
2
HMV1350
BRG d5xD13x4
2
3
HMV6701ZZY
BRG d12xD18x4
2
4
BK0362
T
ail Drive Bevel Gear
A
1
5
BK0363
T
ail Drive Bevel Gear B
1
6
BK0364
T
ail Drive Pinion
1
7
BK0365
T
ail Drive Gear Shaft
1
8
BK0382
T
ail Boom Bracket L
1
9
BK0383
T
ail Boom Bracket R
1
10
BK0414
Pin 2x12
2
1
1
BK0660
Frame Spacer L
5
Main Frame Assembly
Installation of Pitch Frame
No. Material No. Description
Qty.
1
HMJ2-10N
M2x10 Self-Tapping Screw
1
2
HMV840ZZY BRG d4xD8x3
2
3
HMV1280ZZY BRG d8xD12x3.5
2
4
BK0336
Pitch Frame
1
5
BK0075
Link Ball
φ
4.8
1
Optional: add a tiny drop of thick CA on the outside rim of the fovr ball
bearings before inserting them into the plastic Pitch Frame. Be careful
not to get any glue into the ball bearings. Add a tiny drop of thick CA
glue at the tip of the M2x10 self-tapping screw (No. 1) before
screwing it into the Pitch Frame.
32
Note:
The (3) spacer with threads is
supposed to be locate d at middle
position to fit the Body Fitting Post.
Note:
The (3) spacer with threads is
supposed to be locate d at middle
position to fit the Body Fitting Post.
No.
Material No.
Description
Qty
.
1
BK0385
Pitch Guide Collar R
1
2
BK0658
Frame Spacer S
2
3
BK0693
Cross Member
1
Tip:
When setting up the phase
adjustment ring, the flybar and
the tail boom can be the
reference. When the flybar and
the tail boom are centered, the
inner balls of swashplate should
be aligned with the outer balls.
Tighten the socket screw on the
phase ring at this moment.
NOTE: Improper alignment will
cause unwanted mixing.
No. Material No. Description
Qty.
1
********
90 Class Heli Engine
1
2
********
Nut (Comes With the Engine)
1
3
HMC4-8B
Socket Screw M4x8
2
4
HMC4-18B
Socket Screw M4x18
4
No. Material No. Description
Qty.
5
HMO10
Washer d9.5xD16x1
1
6
BK0349
Engine Mount
1
7
BV0380
Cooling Fan
1
8
BV0521
Heavy Duty Clutch
1
No. Material No. Description
Qty.
1
BK0075
Link Ball
φ
4.8
5
2
BK0086
Ball Link 4.8x20
8
3
BK0104
Servo Mounting Plate
6
4
BK0105
Rod Joint
1
5
BK0318
Link Rod 2.3x95
2
6
BK0436
Link Rod 2.3x55
2
7
BK0833
Servo Block
4
8
HMC2516B
Socket Screw M2.5x16
4
No. Material No. Description
Qty.
9
HMM25
Lock Nut M2.5
4
10 HML2
Nut
5
11
HME4-5B
Set Screw
2
12 HMF2-8N
Phillips Machine Screw M2x8
5
13 HSE2614N
Selt-Tapping Screw
4
14 HSE2630N
Selt-Tapping Screw
4
No. Material No. Description
Qty.
1
BK0075
Link Ball
φ
4.8
7
2
BK0086
Ball Link 4.8x20
4
3
BK0095
Link Rod 2.3x76
1
4
BK0104
Servo Mounting Plate
4
5
BK0833
Servo Block
2
6
BK0834
Pitch Lever Fixed Plate
1
7
BK0839
Link Rod 2.3x30
1
8
BK0881
Washer
1
9
BK0883
Pitch Push Pull Lever
1
No. Material No.
Description
Qty.
10 BK0884
Collar, d3xD4xW12
1
11
BV0085
Pitch Link Rod
2
12 HMC3-20B
Socket Screw M3x20
1
13 HMV840ZZY Bearing d4xD8xW3
2
14 HMF2-8N
Philip Maching Screw M2x8
4
15 HMJ2-8N
Selt-Tapping Screw M2x8
3
16 HML2
Nut
4
17 HSE2614N
Selt-Tapping Screw M2.6x14
8
18 HSE2620N
Selt-Tapping Screw M2.6x20
4
No. Material No.
Description
Qty.
1
****
Switch
1
2
****
Receiver Battery
1
3
****
Receiver
1
No. Material No. Description
Qty.
4
****
Gyro
5
BK0106
Foam
2
6 BE1052
Antenna Pipe
1
PV0517
ONEWAY BEARING GREASE
The hole on the Flybar Control Rod has different
opening on two sides. Always snap the bigger opening
to the link ball.
Bigger Hole
Face to Control Arm
10.5mm
10.5mm
When installing pinion gear
, add a small drop of Loctite to the
threads. Make sure not to get Loctite on lower clutch bell bearing.
Important:
For 90 class engine, we recommend the 1
1 teeth pinion for 3D
flying.
The servo tray and cooling fan shrouds on the Raptor 90 are dif
ferent from the
Raptor 60 in order to accommodate the full head sink on the O.S 91. engine.
If using
T
.T
90,
Y
.S 91 or W
ebra 91 engine, make sure to install the fan shroud
baf
fle with two self-tapping screws.
This will ensure optimal cooling of your engine
head.
Add CA glue
Add CA glue
It is necessary to add grease inside the one way clutch before your
first flight. The clutch might lock up once grease is gone. The one
way clutch grease( PV0517) is recommended for this lubrication.
Make sure the inside of Auto Rotation Hub is clean without any dirt
before you insert the one way clutch shaft.
Add Loctite
Add Loctite on
the threads
For 3D flying, it is recommended to use
lower flybar ratio setting.
Self-T
apping Screw
, No. 10 Collar
, and No. 1
1 W
asher
, with two
No. 1 Bearings.
Attach a No. 9 Link Ball with a No. 4 Screw
.
Upon finishing Step 3-1-1, make sure there are no extra parts
left on your workbench.
Elevator Control
Pushrod
Glue the two plastic halves of
the paddle with CA glue before
installation on flybar.
Add Loctite
the tail boom by tightening the four screws on the helicopter.
Visually check from the rear of the helicopter to make sure the
tail rotor output shaft is perpendicular to the main rotor shaft.
Add the tail boom supports.
Add Loctite
The thrust bearing washer with the
SMALLER inner hole should be closer to
the rotor blade.
The thrust bearing washer with the BIGGER
inner hole should be closer to the main rotor
shaft.
4-2-1 Engine Subassembly
Add Loctite
Add Loctite
Add Loctite
Add Loctite
Add Loctite
Add Loctite
Add Loctite
Add Loctite
Add Loctite
Add Loctite
Add Loctite
Add Loctite
Add CA Glue
Introduction
--------------------------------------------------------------------------------------------------------
3
Other Items Required
--------------------------------------------------------------------------------------
4
Warning
---------------------------------------------------------------------------------------------------------------
5
Assembly
1. Main Frame Assembly
---------------------------------------------------------------------------------
7
1-1 Upper Frame Assembly (Bag A) ----------------------------------------------------------------------
8
1-1-1 Pinion Gear Subassembly ------------------------------------------------------------------------
9
1-1-2 Pitch Guide Left Subassembly ------------------------------------------------------------------
10
1-1-3 Pitch Guide Right Subassembly -----------------------------------------------------------------
10
1-1-4 Elevator Control Arm Subassembly------------------------------------------------------------
10
1-2 Lower Frame Assembly (Bag B) ----------------------------------------------------------------------
11
1-2-1 Tail Drive Unit Subassembly ---------------------------------------------------------------------
12
1-2-2 Cooling Fan Casing Subassembly -------------------------------------------------------------
13
1-2-3 Fuel Tank Subassembly
-------------------------------------------------------------
-----------
13
1-3 Main Frame Assembly (Bag C) -------------------------------------------------------------------------
14
1-3-1 Rod Guide Collar Subassembly-----------------------------------------------------------------
14
1-4 Installation of Servo Frame (Bag C) -------------------------------------------------------------------
15
1-5 Installation of Pitch Frame (Bag D) --------------------------------------------------------------------
16
1-5-1 Aileron Lever Subassembly ---------------------------------------------------------------------
17
1-5-2 Metal Elevator Parallel Lever Subassembly -------------------------------------------------
17
1-5-3 Elevator Control Lever Subassembly ---------------------------------------------------------
17
1-5-4 Pitch Control Frame Subassembly -------------------------------------------------------------18
1-5-5 Header Tank Subassembly ----------------------------------------------------------------------
18
1-6 Installation of Main Shaft (Bag E) ----------------------------------------------------------------------
19
1-6-1 Wash Out Subassembly -------------------------------------------------------------------------20
1-6-2 Main Gear Subassembly -------------------------------------------------------------------------
20
2. Rotor Head Assembly
-----------------------------------------------------------------------------------
21
2-1 Metal Rotor Head Assembly (Bag F) -----------------------------------------------------------------
22
2-1-1 Flybar Seesaw Subassembly --------------------------------------------------------------------
23
2-1-2
Metal
Main Rotor Hub Subassembly ----------------------------------------------------------
24
3.Tail Assembly
-------------------------------------------------------------------------------------------------
25
3-1 Tail Assembly (Bag G) -----------------------------------------------------------------------------------
26
3-1-1 Tail Transmission Subassembly ---------------------------------------------------------------
27
3-1-2 Tail Rotor Subassembly ---------------------------------------------------------------------------
28
3-1-3 Tail Drive Shaft Subassembly -------------------------------------------------------------------
28
(9)
(5)
(18)
(1
1)
(10)
(12)
(6)
(4)
(16)
(17)
(7)
(8)
(3)
(15)
(14)
The Liner is pre-glued on the
inside of clutch bell with 30 min
epoxy
.
1-1
1-2
1-3
( 2 )
(1)
1-4
(1)
(2)
1-5
1-6
(7)
(1)
(5)
(4)
(9)
(3)
2-1
3-1
4-1
(5)
(3)
(2)
(1)
4-3
(4)
(2)
4-4
(2)
(7)
(1)
(3)
(5)
(8)
4-2
(3)
(1)
(2)
5-1
5-2
5-3
(4)
(6)
(1)
(3)
(2)
(5)
5-4
5-5
(2)
(3)
No.
Material No.
Description
Qty
.
8
BK0660
Frame Spacer L
3
9
BK0376T
Lower Metal Frame 2
10
BV0870
Metal Lower BRG Block
1
1
1
1-2-1
T
ail Drive Unit Subassembly
1
12
1-2-2
Cooling Fan Casing Subassembly
1
13
1-2-3
Fuel
T
ank Subassembly
1
No.
Material No.
Description
Qty
.
7
BK0659
Frame Spacer M
2
8
BV0869
Metal Upper BRG Block
1
9
1-1-1
Pinion Gear Subassembly
1
10
1-1-2
Pitch Guide L
Subassembly
1
1
1
1-1-3
Pitch Guide R Subassembly
1
12
1-1-4
Elevator Control
Arm Subassembly
1
(3)
No. Material No. Description
Qty.
10 BK0093
Link Rod 2x46
1
11 BK0407
Collar d3xD4x4.5
2
12 BK0410
Collar d3xD4x13
2
13 1-5-1
Aileron Lever Subassembly
1
14 1-5-2
Metal Elevator Parallel Lever Subassembly
1
15 1-5-3
Elevator Control Lever Subassembly
1
16 1-5-4
Pitch Control Frame Subassembly
1
17 1-5-5
Header Tank Subassembly
1
No. Material No. Description
Qty.
6
HMM4B
Lucknut M4
1
7
BK0617
Bolt M4x25
1
8
BV0504
Metal Swashplate
1
9
1-6-1
Washout Subassembly
1
10 1-6-2
Main Gear Subassembly
1
No.
Material No.
Description
Qty
.
10
BK0076
Collar d3xD4x10
1
1
1
BK0088
W
asher d3xD5x0.5
1
12
BK0346
T
ail Pitch Control Lever
1
13
BK0370
T
ail Case L
1
14
BK0371
T
ail Case R
1
15
BK0372
T
ail Input Bevel Gear
1
16
BK0373
T
ail Output Bevel Gear
1
17
HMY2-12
Pin 2x12
1
18
3-1-2
T
ail Rotor Subassembly
1
No. Material No.
Description
Qty.
1
HMM3Z
Locknut M3
6
2
HMC3-16B
Socket Screw M3x16
2
3
HMC3-20B
Socket Screw M3x20
2
4
HMC3-25B
Socket Screw M3x25
2
5
HMC3-30B
Socket Screw M3x30
2
6
BK0087
Washer d3xD8x1.4
4
No. Material No. Description
Qty.
1 HMJ2-8N Self-Tapping Screw M2x8 4
2
BK0447
Tail Support Rod End
4
3
BK0669
Tail Support Rod
2
No. Material No.
Description
Qty.
1
HMC4-42B
Muffler Bolt M4x42
2
2
HMT4B
Spring Washer
2
3
********
Muffler ( 90 )
1
4
4-2-1
Engine Subassembly
1
5
HMC4-12B
Socket Screw M4x12
4
6
BK0435
Washer d4xD11xW1.7
4
BAG
A
BAG B
BAG C
BAG C
BAG D
(L)
(R)
BAG E
BAG F
BAG G
BAG H
BAG I
97.5mm
48mm
(3)
Throttle
Collective Pitch
(2)
BAG I
BAG J
BAG K
(1
1)
(8)
(7)
(2)
(6)
(3)
(5)
(9)
(4)
Please complete subassembly steps 1-2-1 through 1-2-3 first.
Then attach the subassemblies to the two Lower Frames. Note
that the Metal Lower BRG is installed with the bearing open side facing up.
Please add a small drop of Loctite on every bolt
before screwing it into the aluminum hex spacer
. Do not apply Loctite to the bolts which are going to secure the Lower BRG
Block at this moment.
Assemble the upper main frames by starting with the two Metal Upper Frames.
The Pinion Gear Subassembly must be assembled
first according to Figure 1-1-1. Next insert three hex-shape frame spacers into the plastic Pitch Guide according to Figure 1-1
-2
and 1-1-3.
Assemble the Elevator Control
Arm subassembly according to 1-1-4. Insert it in between the two Upper Frames.
The
metal Elevator Control
Arm is not symmetrical.
The side with the longer profruding round knob should be on the right side of the
helicopter
.
Then attach the other subassemblies to the Upper Frames.
Locate Hex W
renches in BAG L
which you ne ed for
assembly
.
Please add a tiny drop of non-permanent type Loctite on the tip of all bolts before screwing them into the hex shaped aluminum
frame spacers. Never use too much Loctite, otherwise it will become nearly impossible to remove later on for servicing. Only use
the non-permanent type of Loctite. If encountering dif
ficulty in removing any bolt that was locked up by Loctite, heat up the head
of the screw or bolt with the tip of a hot soldering iron, it will help soften the cured Loctite.
For the kit, parts are bagged according to each major assembly and are labeled "Bag
A, Bag
B, etc."
The heading for each assembly indicates which bag to open.
As a go od practice,
only open up the bag that you need for the particular assembly
. Check the parts in that bag
against the parts list shown for each assembly as well as each sub-assembly to make sure
there are no missing parts.
T
o prevent losing small hardware, please empty the small nuts
and bolts and parts into small plastic trays on your work table.
At the end of each major
assembly
, there should be no left over parts.
The fuel tank comes assembled from the factory because every tank has been
checked for leak. If you were to take the tank apart here is how to put it back
together
. Install the silicone fuel line to the Fuel Nipple.
Then add the rubber
fuel tank stopper and the clunk weight.
The stock silicone fuel line is very soft
and thin which is designed to allow the clunk to pick up fuel easily during 3-D
aerobatics.
The pickup line should be inspected and replaced if necessary every
month, otherwise when it becomes soggy it can break of
f.
A
thicker silicone line
maybe substituted but make sure the clunk will reach the bottom when moving
the fuel tank to all dif
ferent orientations.
(4)
(5)
(2)
(2)
(4)
(1)
(6)
(5)
As show in Figure 1-3-1, insert two hex
Frame Spacers S into the plastic Rod
Guide Collars.
Then join the Upper
Frame
Assembly to the Lower Frame
Assembly according to drawing 1-3.
Secure the Set Screws (No.1) to the
frames, and fit the Body Posts (No.4)
to the Set Screews.
The two Body Posts
will be used to secure the canopy in the
future.
Add Loctite on all bolts and
inside BK0103 threaded hole.
Install the one-piece servo frame with six self-tapping screws.
Do not use Loctite when attaching self-tapping screws to plastic
parts. Loctite is only for threading metal into metal parts.
Assemble the constant drive Main Gear Subassembly according to Figure 1-6-2 first. Then build up the Wash Out Subassembly
according to 1-6-1. Insert the No.3 Main Shaft into the bearings and then add the No.4 Lock Ring and slide in the Main Gear
Subassembly. Add two M3x6 Button Head Screws to the Locking Ring, and the two screws are threaded into the holes on the
main rotor shaft.
The locking ring prevents the main shaft from sliding up. Line up the hole on the main gear and the main shaft, then insert M4x25
mm Bolt through them. Place a 4 mm M4 locknut on the other side of the autorotation hub, and then tighten the Bolt. Do not
over tighten the Bolt, otherwise the autorotation assembly will be distorted. Loosen the 3mm bolts holding the Upper and lower
bearing blocks for the 12mm main shaft. Wiggle the main shaft in the bearing blocks until the main shaft spins freely in the bearings.
This ensures the upper and lower bearing blocks are aligned. Push the lower bearing block up until the main shaft has no up
and down play. Then tighten the 3mm bolts for the upper and lower bearing blocks.
Insert the pin into the Washout Link. Add a tiny drop of Loctite on the inside
and outside of BK0409 Collar which will help give a completely slop free
control system. Do not let the Loctite seep into the bearing. Adjust the
tightness of the M3x12 bolts so the mixing arms can move freely but without
wobble or racheting the ball bearings. Add a ti ny drop of thick CA glue at
the tip of the M2x10 self-tapping screw (No. 1) before screwing it into the
Flybar Control Levers (No. 6).
Make the two pushrods for controlling the blade pitch. The distance 43 mm is measured between the center of two pushrod holes.
Attach the Seesaw Hub of the Control Paddle Assembly to the Main Rotor Head with Socket Screws (M3x10).
Please add a small drop of Loctite along the entire length of the M3x10 Socket Screw (No.5) and on the outside of the collar
d3xD4x5.5 (No.3). Temporarily install the Washout Base Guidence Ring, but do not tighten the No.6 M3 Socket Screw yet.
Assemble the tail transmission subassembly according to 3-
1-1 and 3-1-2 first.
And the tail drive shaft subassembly according
to 3-1-3.But do not close the two halves of the tail transmission
tightly
.
Y
ou will do this when you are ready to install the gearbox
onto the tail boom.
When installing the tail transmission, make sure the housings
match the hole on to the tail boom.
Add Carbon V
ertical Fin with
machined washer and Locknut, then tighten the five 3 mm bolts.
Add carbon V
ertical Fin with Pom washer and Locknut.
Before inserting the finished tail drive shaft assembly into the
tail boom, add some flexible silicone glue or ZAP
Goop glue
around the outside of the tail drive bearing housing.
This will
prevent the bearing housing from spinning inside the tail boom.
(7)
Install bearings No. 2 and No.3 into the
T
ail Cases. Install No.
16
T
ail Bevel Gear onto the
T
ail Shaft. Gently tap the No. 17
Pin into the Bevel Gear and
T
ail Shaft.
Then secure the pin
with a No. 7 Set Screw with Loctite.
After installing the M3x4 set screws, try pushing on the 2x12
pin with a small
Allen wrench to make sure the set screw has
locked the pin in place securely
. Before closing the two halves
of the
T
ail Cases, please check the gear mesh between gears
No. 15 and No. 16. If the gears mesh too tight, then a 5 mm
i.d. washer should be added to move the gear No. 16 further
out. If there exists too much freeplay
, then a 5 mm i.d. washer
to push gear No. 16 closer to gear No. 15.
Install the No. 12
T
ail Pitch Control Lever as shown with No. 6
Slide four No. 6 Rod Guides onto the tail boom. Do not glue
them onto the tail boom yet.
Add a tiny drop of CA
glue to the
pushrod guide after you finish building the entire helicopter
.
Before adding glue, make sure the tail pushrod is hooked up
to the servo and the rod travels in a straight line and moves
very smoothly
.
Congratulation, we are almost done. Install the finished main
rotor head onto the 12 mm rotor main shaft. Secure it with a
M4x20 Bolt and M4 Locknut. Make up two 1
13.5 mm long
pushrods and attach them to the Bell-Hiller mixing arm.
Before installing the plastic end caps, please
add a drop of slow, thick CA glue on the
rim of the end caps and on the inside edge
of the aluminum skid.
Slide the finished tail boom into the helicopter. The four bolts
on the helicopter must be loose in order to insert the tail boom.
Make sure the tail drive shaft is inserted into the front receptacle
properly. Check this by turning the main rotor head. Secure
Secure the two ends to the rod with Epoxy, making sure the
two metal ends are perpendicular to each other.
(4)
Attach the engine into the side frames, with four M4x12 bolts and
four washers, but do not tighten until Section 6-1.
Install the muffler after you have building the entire helicopter.
Always add Loctite on the muffler bolts.
Install the servos and make up the pushrods according to the drawings. The distance between the steel ball and the center of
servo arm are shown in the drawing. Use them as a guide. These distances are used in conjunction with the servo travels (ATV
or End point) set to 100% for all the channels in the transmitter. Tune them later on to suit your personal flying style.
Attach the rudder servo to the rear mounted carbon plate with four 2.6mm bolts and four M2.6 locknut.
Make up the throttle and collective control pushrods according
to the drawing. Use the outermost hole on the carburetor throttle
control arm. Attach the steel ball on the throttle servo arm at
approximately the same distance as the steel ball on the throttle
arm.
Make up the throttle at 97.5mm long first, and then adjust the
pushrod length and throttle servo ATV or Endpoint so full throttle
stick command will open the carburetor barrel fully. And full low
stick and low throttle trim will close the carburetor barrel completely.
Install the receiver and receiver battery. Even though the receiver and battery can be attached to the helicopter tray by using
double sided foam tape, but it is better to wrap the receiver and battery separately using half inch or 10 mm thick foam. Then
secure them to the tray using six to eight rubberbands, or Velcro bands.
Carefully cut out the canopy (windshield) using scissors. The
best scissors to use are (TTR 1304) designed to cut RC car
bodies and Canopy. Install the canopy to the body using six
small screws. Drill small holes in the canopy and body for the
holes. Drill two more holes for the rubber grommets.
Refer to color box and apply the decals (In BAG M).
T
ools for
Assembly
The Raptor 90 3D is designed for easy maintenance using standard hobby tools. Please only use genuine
Thunder
T
iger parts.
Please keep the model clean and well tuned. It will provide you with long lasting pleasure in return.
(6)
(13)
(2)
(9)
(7)
(4)
(18)
(3)
(16)
(8)
(17)
Add Loctite
(Included)
Add a tiny drop of thick CA glue at the tip of the M2x10
self-tapping screw (No. 1) before screwing it into the
Aileron Levers.
(9)
(10)
(11)
Make up the lan ding gear according to the
drawing.
(10)
(2)
(4)
(6)
(9)
(3)
(10)
(1)
(1
1)
(5)
(8)
(3)
(1)
No.
Material No.
Description
Qty
.
1
HSE3-6B
Self-T
apping Screw M3x6
2
2
BK0660
Frame Spacer L
4
3
BK0662
Cooling Fan Baf
fle
1
4
BK0665
Fan Casing L
1
5
BK0666
Fan Casing R
1
(2)
(1)
(4)
(3)
(1)
(3)
(2)
(4)
(4)
(3)
(2)
(5)
(1)
(12)
(5)
(10)
(14)
Assemble the metal flybar control arms according to the drawings. Slide Flybar Control Arm onto the No.18 Flybar Rod. Slide
the flybar into the No.17 Seesaw Hub. Make sure the Flybar has equal protrusion from each side of the Seesaw Hub measure
them with a ruler, then install and tighten the No.8 HME4-5B set screws. Add the paddles. Make sure the two paddles and the
two flybar control arms are all parallel. Lock the paddles with No.6 set screws.
Assemble and install the No.10 Mixing Levers and No.5 Bearings according to the drawing using No.12 Collar and No.9 d3xD5x0.5
washer.
Note:
Before installing the Mixing Lever (No.10), please add a small drop of Loctite along the entire length of the M3x18 button
head socket screw (No.4) and on the outside of the collar d3xD4x13 (No.12). Be careful do not let the Loctite seep into the bearings.
There are two choices of hole positions on the aluminum seesaw for attaching the mixing lever arm. The outside hole gives higher
Bell-Hiller mixing ratio. For aggressive 3D flying, you can attach the Bell-Hiller mixing arms to the inner hole which gives lower
flybar ratio.
(6)
No. Material No. Description
Qty.
10 BK0324
Mixing Lever
2
11
BK0406L
Paddle Root
2
12 BK0410
Collar d3xD4x13
2
13 BK0416
Paddle Stopper
2
14 BK0432L
Flybar Paddle
2
15 BK0633
Flybar Control Frame
2
16 BK0871 Longer Stabilizer Arm 2
17 BV0865 Longer Seesaw 1
18 BK0866 SUS Flybar 1
No. Material No. Description
Qty.
1
HMF2-8N
Phillips Machine Screw M2x8
2
2
HMJ2-10N
Selfing-Tapping Screw M2x10
4
3
HMC3-10B
Socket Screw M3x10
2
4 HMC3-18B Socket Screw 2
5
HMV840ZZY BRG d4xD8x3
4
6
HME4-3B
Set Screw M4x3
4
7
HME4-5B
Set Screw M4x5
2
8
BK0075
Link Ball
φ
4.8
6
9
BK0088
Washer d3xD5x0.5
2
Insert the aluminum Main Rotor Hub Pin and the Flap Dampers. (might need to apply silicone grease for easy installation). Push
the No.7 Feathering Spindle into the dampers and the rotor hub. Add No. 14 Flybar Control Rod. Slide both finished Main Rotor
Grip onto the feathering spindle and the secure with two M4x10 bolts and washers according to the drawing. Use two Allen
wrenches to tighten the two M4x10 bolts simultaneously.
Important Note:
The Raptor 90 3D kits come with non-linear flap damper for aggressive 3D flying. You may choose to experiment adding from
one up to three 0.4mm thick shim (No.10) washers between the washer (No.8) and bearing to further stiffen the main rotor flapping.
Stiffing the main rotor head will speed up the cyclic transient response, but may cause the helicopter fuselage to oscillate at around
1600 RPM. This oscillation characteristic exists for all helicopters with hard 3D flap dampers. The inner dampers should be
replaced periodically if a lot of 3D flying has been done. When the dampers are worn, the main rotor blades can flap excessively
during some 3D maneuvers and risk touching the tail boom.
Add flexible silcone glue or ZAP
Goop glue around the outside
before insert ing into the tail
boom from the front side.
(13)
(2)
(1)
(10)
(3)
(1)
(2)
(5)
(3)
(2)
(1)
(4)
180mm
25mm
(1)
(3)
(2)
(3)
The optional Thunder Tiger Remote Glow Plug Adaptor (#3803)
is recommended as shown, making starting easy without the
removal of your canopy.
(1)
(6)
(3)
(7)
(5)
(1)
(4)
(2)
Cut a hole at the
front air scoop for
backward flights.
(7)
No. Material No. Description
Qty.
9
BK0477
Washer
2
10 BK0703
Flap Damper Washer 0.4mm
6
11
BK0874
Inner Damper
2
12 BK0875
Outer Dampper
2
13 BK0075
Ling Ball
φ
4.8
2
14 BK0664
Flybar Control Rod
2
15 BK0319
Main Rotor Pitch Housing
2
16 BV0548-1
Metal Main Rutor Hub
1
No. Material No.
Description
Qty.
1
HMC4-10B
Socket Screw M4x10
2
2
HMJ2-12N
Self-Tapping Screw M2x12
2
3
HMV1680
BRG d8xD16x5
4
4
HMX0816
Thrust Bearing d8xD16x5
2
5
BK0330
Main Rotor Hub Pin
1
6 BK0325 Thrust
Washer
2
7
BK0326
Spindle
1
8
BK0435
Washer
2
Fiberglass or Carbon Rotor Blade
(8)
(11)
(15)
(1)
(6)
(1)
(5)
Add Loctite when setting up the
gearmesh in step 6-1.
(7)
No. Material No.
Description
Qty.
7
BK0539
Carbon Rear Servo Plate
1
8
BK0878
Bracket (Top)
1
9
BK0879
Bracket (Bottom)
1
10 3-1
Tail Assembly
1
11
4-4-1
Tail Support Subassembly
2
(6)
(9)
(1)
(2)
(1)
(2)
(12)
(4)
(4)
Engine System
Use a high quality 90 size 2-stroke
model helicopter engine, such as the
Thunder
T
iger
TT
PRO-90H, OS 91
SZ-H,
YS 91 ST
, W
ebra 91, or
equivalent. Please beware, some
engines may not fit because of their
shape and size.
The Raptor 90 3D
kit comes with a cooling fan hub to fit
the
TT
PRO-90H, OS 91 SZ-H, W
ebra
91.
W
e recommend a high quality muf
fler
or tuned exhaust system designed to
fit on the left side of the model.
Rotor Blades
It is important to use main rotor blades
that are of high quality and suitable
for your flying style. If fiberglass or
carbon graphite blades are used, the
length should be between 680 and
710 mm. Blade weigh t should be
between 170 and 200 grams.
Starter System
T
o start the engine, it is necessary to
use an electric starter with a 6mm
shaft extension.
The starter and the
6 mm extension are available from
Thunder
T
iger
, the part numbers are
No.2675 and No.3801.
Use a strong high torque 12 volt
electric starter which is designed for
models.
(9)
(2)
(1)
(3)
(5)
(8)
(10)
(6)
(7)
(1
1)
(4)
Add a small drop of Loctite.
Make sure it locks the pin.
Install BK0364 and BK0362 onto BK0365
T
ail Gear Drive Shaft.
Then insert the
two Pins and secure them with two M3x4 Set Screws.
Add a tiny drop of Loctite
on the set screw thread before inserting them.
Always use a very small amount
of Loctite liquid on the thread, otherwise it may be nearly impossible to remove
the set screws in the future for servicing.
After installing the two M3x4 set screws
(No. 1), try to push on the 2x12 pins with a small
Allen wrench to make sure the
set screws have locked the pins in place securely
.
Install the four ball bearings
and the hex shaped Frame Spacers according to the drawing.
Before closing
the two halves of the
T
ail Boom Brackets, please check the gear mesh between
gears No. 4 and No. 5. If there exists too much freeplay
, add some 5 mm i.d.
washers on top of gear No. 4. (The 5 mm i.d. washers are provided in BAG G).
Add a small drop of Loctite.
Make sure it locks the pin.
Shim W
asher
(3)
(5)
(4)
(2)
(3)
(1)
Add CA Glue
Standard flybar ratio
Lower flybar ratio
Mild 3D Flying
Extreme 3D Flying
(3)
(8)
(2)
(7)
(5)
(1)
Attach the engine mount to the engine using four 4mm bolts and Loctite.
The cooling fan hub is threaded to fit the OS, TT or Webra only. Place the washer that came with your engine onto the engine
crankshaft first. Then screw the fan hub onto the engine. Add a tiny drop of Loctite on the engine nut. Do not use too much
Loctite. Tighten the engine nut using a socket head wrench while grabbing the fan with a towel. The nut should be tighten securely.
For 50-size or bigger engines, we do not recommend using a piston locking tool on the glow plug hole because that may damage
the engine. Attach the No. 8 Heavy Duty Clutch to the fan hub. Add a drop of Loctite on the threads of the M4x8 bolts. The
threads on the aluminum cooling fan hub are for the TT 70H, OS 61 SX, OS 61LX, OS 70H, TT 90H, OS 91 or Webra 91 engines.
If YS 61, 80 or 91 engines are used, the fan hub must be re-tapped by the modeler to M8x1mm thread size or purchase a optional
plastic fan hub with threads for the YS engine(PV0198YS) or the metal fan for the YS (PV0293YS).
(4)
(3)
(1)
(2)
(4)
(1)
(3)
(3)
(2)
(3)
(6)
(10)
(8)
(1)
(9)
(5)
Please complete subassemblies 1-5-1 through 1-5-5 first, then add them to the Main Frame. Fit the Pitch Control Frame
Subassembly. Attach the E Ring on the left side of the Metal Elevator Control Arm. Then fit the Elevator Control Lever to the
right side, insert the pin and fix it with a set screw. Secure the Pitch Control Frame with a M3*10 Socket Screw and a collar on
the left side. And attach the Elevator Push Pull Lever to the right side of the Pitch Control Frame as shown. Adjust the two bolts
so that the Pitch Control Frame can move freely without excessive play. Finally, add the two plastic Aileron Levers and the 66.5mm
elevator pushrod. Add the Washers (BK0088) to make sure that the Aileron Lever and the Metal Elevator Parallel Lever will not
touch each other during operation.
(2)
(1)
(3)
(2)
(9)
(3)
(10)
(8)
(1)
(4)
(7)
(5)
(6)
(11)
(8)
(6)
(4)
Outer hole for standard.
Inner hole for extreme 3D.
(11)
(12)
(3)
(15)
(13)
(2)
(11) (12)
(16)
(9)
(10)
(7)
(14)
(8)
(1)
(4)
(5)
(13)
(8)
(3)
(6)
(9)
(10)
(14)
(4)
(1)
(5)
(5)
(6)
(6)
(1)
(10)
(7)
(4)
(1)
(2)
(4)
(3)
(5)
(4)
(1)
(7)
(6)
(9)
(12)
(5)
(2)
(11)
(3)
Add Loctite
Add Loctite
Add Loctite
(11)
Add Loctite
Add Loctite
Add Loctite
Add Loctite
Add Loctite
Add Loctite
30mm
(2)
Paddle
Flybar
A
Arm
Phase
Adjustment
Ring
Swash
plate
Boom
(3)
(8)
(14)
(13)
(9)
(1) (10) (12)
(7)
(11)
(12)
(2) (7)
(8)
(6)
(5)
(4)
(1) (14) (16)
(11)
(18)
Pitch push-pull subassembly
(13)
(1)
(15)
(10)
(9)
(17)
(2)
(3)
Add Loctite
Add Epoxy
Add Epoxy
(13)
(14)
(17)
(15)
(16)
Содержание Raptor 90 3D
Страница 1: ......
Страница 22: ...21 ROTOR HEAD ASSEMBLY 2...
Страница 26: ...25 TAIL ASSEMBLY 3...
Страница 30: ...29 FINAL ASSEMBLY 4...
Страница 36: ...35 INSTALLATION OF PERIPHERAL EQUIPMENT 5...
Страница 42: ...41 SETTINGS 6...
Страница 50: ...49 PARTS LIST SECTION 7...