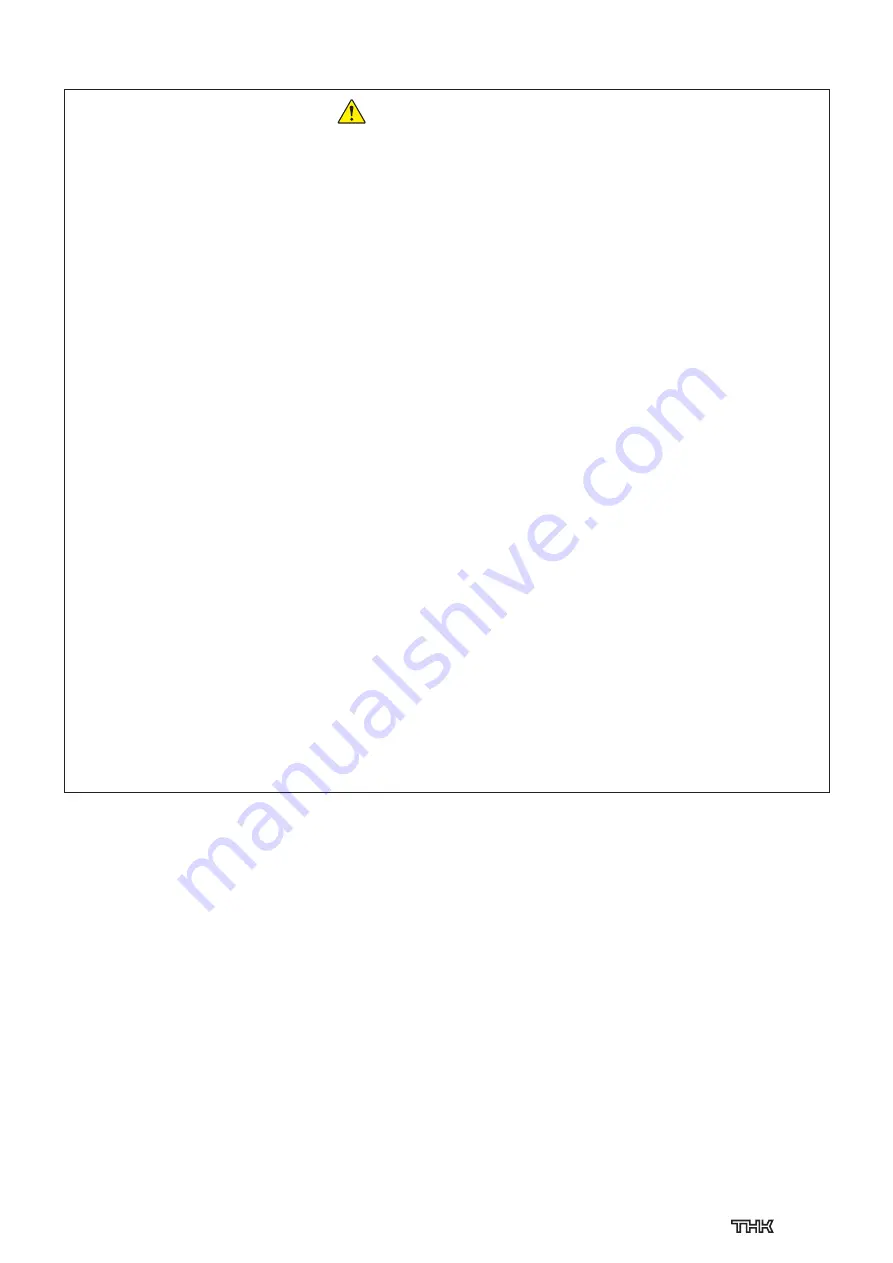
Precautions on Use
Handling
·
Do not disassemble the actuator or control devices unless necessary. This may result in debris entering the product and loss of functionality.
·
Take care not to drop or strike the actuator or control devices. Otherwise, it may cause injury or damage the unit. Even if there is no outward
indication of damage, a sudden impact could prevent the unit from functioning properly.
·
Please contact THK when using the product in special environments such as locations exposed to constant vibrations, clean rooms, vacuums,
and low/high temperatures.
·
When using the product in a wall-mounted orientation, install with the pulley side up.
·
The TSC controller for ET cannot be used to operate ES, EC, KRF, or other models.
Operating Environment
An improper usage environment may cause failure of the actuator and control devices. To avoid this, prepare an environment such as the
following.
·
Actuator: Ambient temperature between 0°C to 40°C, ambient humidity 80% RH or lower, no freezing, no condensation
·
Controller: Ambient temperature between 0°C to 40°C, ambient humidity 90% RH or lower, no freezing, no condensation
·
A location with no corrosive or flammable gas
·
A location where electrically conductive particles such as steel dust, dust, oil mist, cutting oil, water content, salt content, or organic solvents
will not be present in the air
·
A location not exposed to direct sunlight or radiant heat
·
A location where no strong electric fields or powerful magnetic fields are generated
·
A location where vibrations or impacts are not transmitted to the main unit
·
A location where inspections and cleanings can easily be performed
Safety precautions
·
Do not touch any moving parts while the product is in operation or in an operable state. In addition, do not enter the operating range of the
actuator.
·
When installing, adjusting, inspecting, or performing maintenance on the actuator and connected peripherals, be sure to disconnect all power.
Implement safety measures to ensure that no one else can turn the power on.
·
If performing a task involving multiple people, confirm how to perform the work, what signals will be used, and how to handle problems before
beginning, and assign another person to monitor the work.
·
Carefully read JIS B8433 “Manipulating Industrial Robots - Safety” and the Japanese Ministry of Health, Labour and Welfare’s “Ordinance on
Industrial Safety and Health” before working with the product, and follow the guidance within.
·
Using this product in excess of the torque limit may damage the components or cause an accident.
·
Do not set the torque control parameter higher than the torque limit.
·
A stopper is installed inside the product. It is intended to limit the stroke, and may become damaged in the event of a strong impact.
·
In applications where this product will be moved or transferred, the conditions of use may cause inertia from the motor’s mass to result in
damage to the motor attachment (Housing A) or other parts. Please contact THK before using in this manner.
Lubrication
·
Thoroughly wipe off anti-rust oil before using the product.
·
The ET must be lubricated in order for it to demonstrate its full performance. Insufficient lubrication may increase wear on the rolling elements
and lead to premature damage.
·
Do not mix lubricants with different properties.
·
Contact THK if a special lubricant will be used.
·
Contact THK if oil lubricant will be used.
·
The lubrication interval will vary depending on the usage conditions, so we recommend determining the lubrication interval based on the initial
inspection.
Storage
·
When storing the actuator, enclose it in a package designated by THK and store it in a horizontal orientation while avoiding high temperatures,
low temperatures, and high humidity.
·
Avoid storing control devices in an environment with high/low temperatures or high humidity.
26
Содержание ET20 Series
Страница 26: ...MEMO 25...