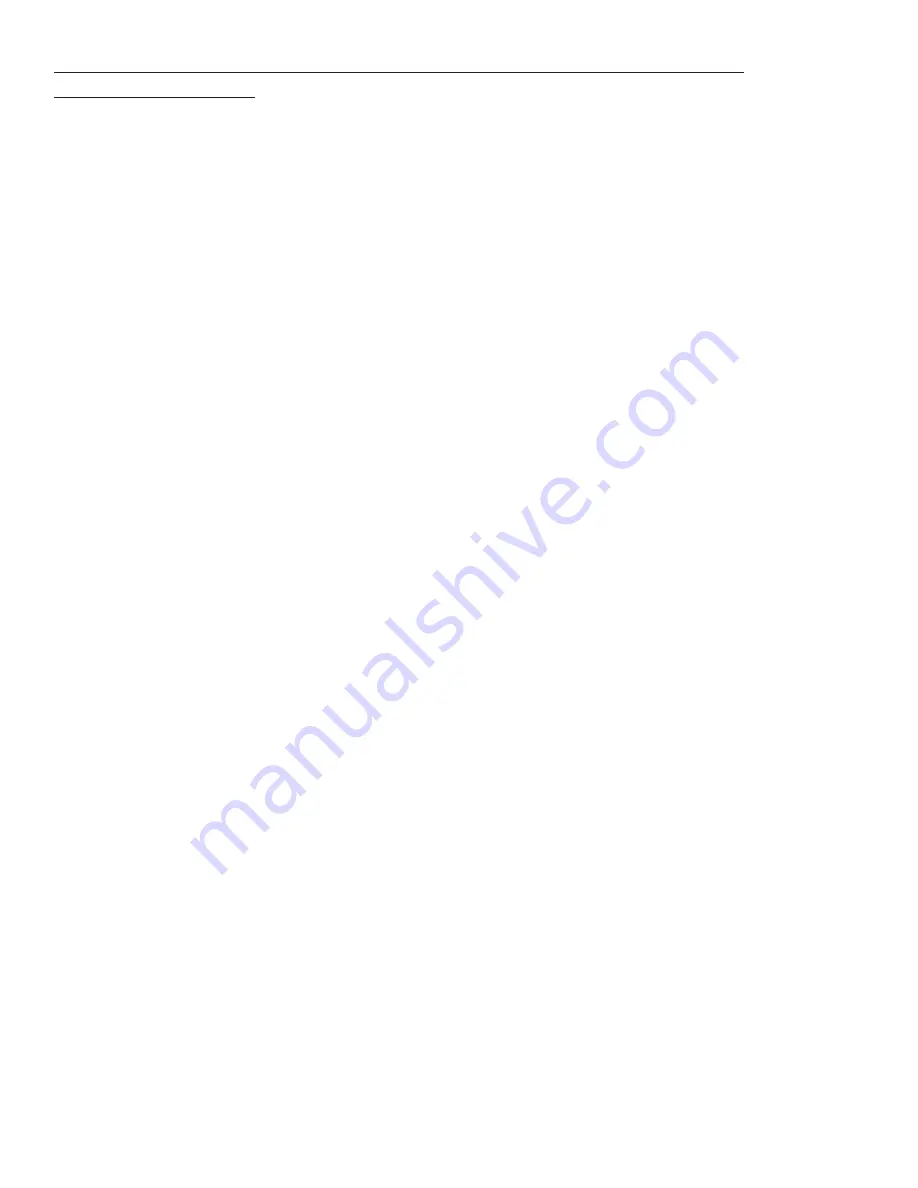
Section 4.2: V1 Mixing Valve Adjustment Instructions with the WWM
Diaphragm Removed
Before beginning repairs read and understand Section 3.1 and follow the steps in Section 3.2
to decommission the Therm-O-Mix Station. The Station should be tested after all repairs are
completed.
1.
Label each hose connection going to the diaphragm housing for easy re-installation. (See
Appendix #3)
2.
Disconnect hoses from the diaphragm housing only.
3.
Use a 1-1/2” wrench or spud wrench to loosen diaphragm valve assembly. Once unthreaded,
pull diaphragm valve out. Some resistance may be felt due to O-ring seal.
4.
Remove cap nut and loosen calibration lock nut with a 7/16” wrench.
5.
Place the stainless steel sensor into a water bath with a temperature 5F over the set point
for five minutes. *Note: The sensor should be at or below 75F prior to being placed into the
water bath for proper calibration. Use calibration screw to adjust the valve spool so that the
opening between the spool and the cap is .160-.175 in. (See Appendix #5 & #6).
6. Place stainless steel sensor into a water bath with a temperature 5°F below the set point for
five minutes. Verify that the top of the spool is sitting on the bottom of the cap.
7.
Once properly adjusted, tighten the calibration lock nut and replace cap nut.
8.
Thread WWM Diaphragm Actuator back into the V1 Mixing Valve Tee assembly and tighten
with 1-1/2” wrench.
9.
Position the diaphragm housing so that the adaptor fittings are pointing to the side of the
body with the braided hoses. *Note: To position the diaphragm housing, rotate clockwise
when looking down on the Therm-O-Mix® Station/WWM to prevent the valve internals from
loosening.
10. Reconnect the braided hose lines by hand tightening the hose swivel fittings onto the
adaptor fittings. Use a 9/16” open end wrench to tighten the swivel nut 1 to 1-1/2 hex
flats or 60 to 90 past hand tight. *Use second 1/2” wrench as a back-up wrench to
prevent hose from twisting.
*If braided hose connections containing orifice plates are opened, the orifice plate must be
replaced. Orifice plates have been included in the replacement kit in case they are needed.
(See Appendix #3)