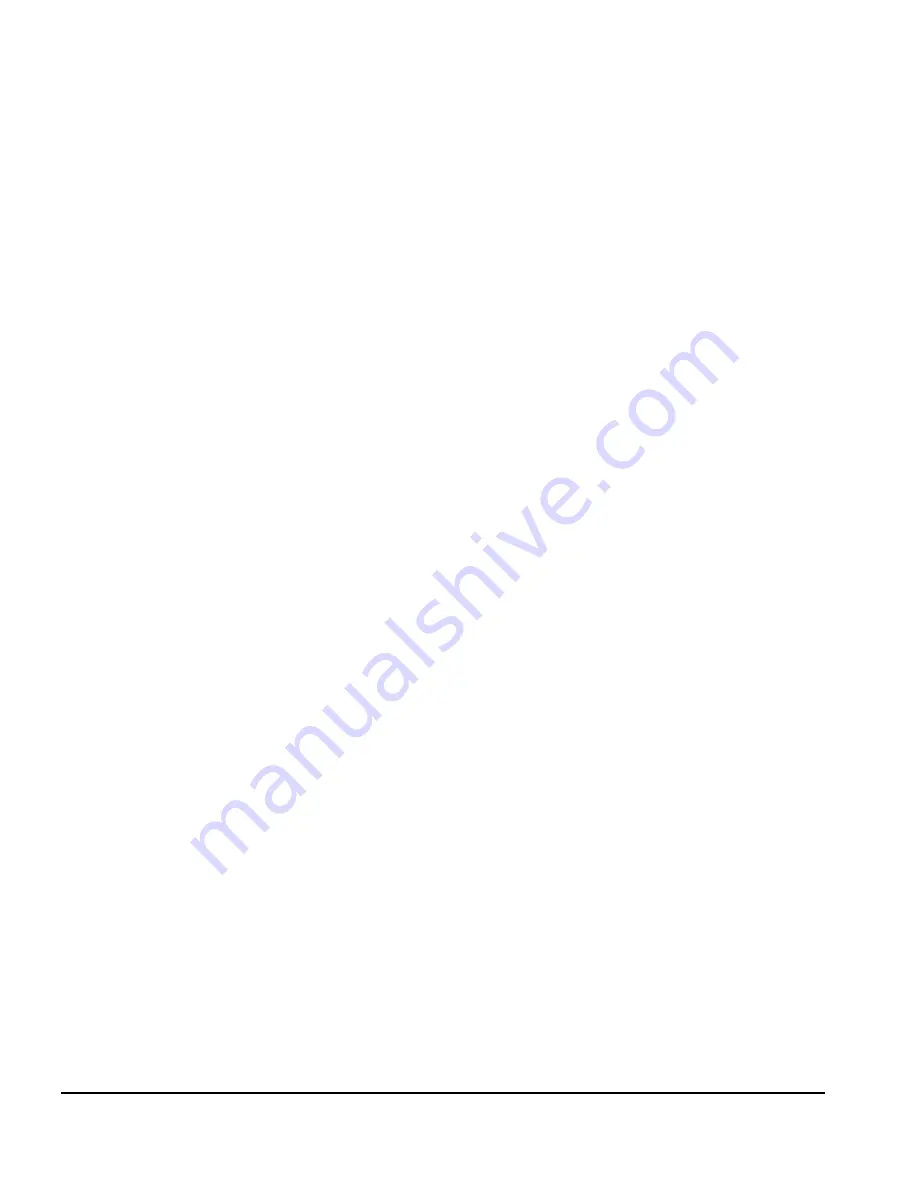
Valve Oven Operating Manual
May 2003 Edition
Part Number 317 093 63
© 2003 Thermo Finnigan Italia S.p.A. All rights reserved.
Printed in Italy
Published by ThermoFinnigan Italia S.p.A., Strada Rivoltana, 20090 Rodano - Milan - Italy
Tel: +39 02 95059355 Fax: +39 02 95059388
Printing History: First Edition, released May 1999.
Second Edition, released July 2002
Third Edition,
released May 2003
Disclaimer
Technical Information contained in this publication is for reference purposes only and is subject to change without notice. Every effort has
been made to supply complete and accurate information; however, Thermo Finnigan assumes no responsibility and will not be liable for any
errors, omissions, damage, or loss that might result from any use of this manual or the information contained therein (even if this information
is properly followed and problems still arise).
This publication is not part of the Agreement of Sale between Thermo Finnigan and the purchaser of a TRACE™ GC Ultra system. In the
event of any conflict between the provisions of this document and those contained in Thermo Finnigans’s
Terms and Conditions, the
provisions of the Terms and Conditions shall govern.
Reference to System Configurations and Specifications supercede all previous information and are subject to change without notice.
Trademarks
TRACE™ is a trademark of Thermo Finnigan Italia S.p.A.. Other brand and product names may be trademarks or registered trademarks of
their respective companies.
Содержание Valve Oven
Страница 1: ...Valve Oven Operating Manual ...
Страница 18: ...Chapter 1 Valve Oven Overview Valve Oven Components 18 Operating Manual ...
Страница 34: ...Chapter 2 Valve Installation Configuring Valves 34 Operating Manual ...
Страница 42: ...Chapter 3 Operation Operating Valves Automatically 42 Operating Manual ...
Страница 46: ...Chapter 4 Troubleshooting 46 Operating Manual ...
Страница 52: ......
Страница 60: ...Index 60 Operating Manual ...
Страница 62: ...Table 4 1 Leak Testing for Valves 44 Table 4 2 Causes and Remedies for Improper Valve Switching 44 ...