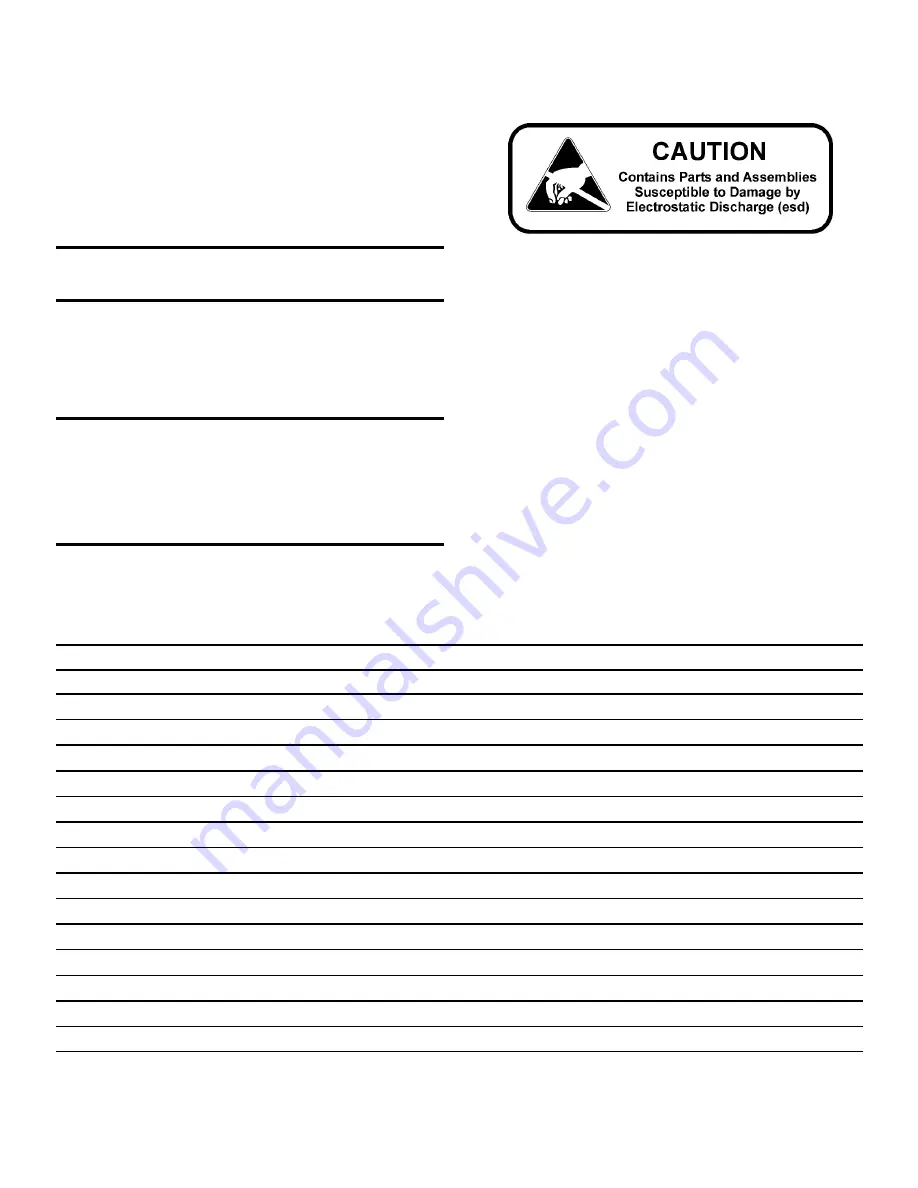
Model 3920 _________________________________________________________________________________
i
Read This Instruction Manual.
Failure to read, understand and follow the instructions in
this manual may result in damage to the unit, injury to operat-
ing personnel, and poor equipment performance.
CAUTION! All internal adjustments and maintenance must
be performed by qualified service personnel.
Refer to the serial tag on the back of this manual.
The material in this manual is for information purposes only. The
contents and the product it describes are subject to change with-
out notice. Thermo Electron Corporation makes no representa-
tions or warranties with respect to this manual. In no event shall
Thermo be held liable for any damages, direct or incidental, aris-
ing out of or related to the use of this manual.
MANUAL NUMBER 7033920
15
21505/SI-9018
9/18/03
New drier (P/N 209016), no flare connections
ccs
14
21173/IN-3057
11/15/02
Added ground shields on temperature and humidity probes
ccs
13
20479/IN-3013
6/27/02
Removed Auto IR CO
2
option as a standard accessory
aks
12
20479/IN-3013
5/29/02
Added Auto IR CO
2
option as a standard accessory
aks
--
20480/PIP-041
11/21/01
Removed reference to p-trap (190467), no longer on parts list
ccs
11
20342/PIP-012
10/3/01
Revised electrical schematics
aks
10
19935
5/8/01
Added 3920-71 drawing
aks
9
IN-2858
3/13/01
Revised control panel access and revised electrical schematic
aks
8
19617
12/13/00
New door - updated electrical schematics
ccs
7
19207/IN-2827
6/28/00
Revised electrical schematics and parts list (250200 to 300345 contactor) ccs
6
--
4/20/00
Quark format
ccs
5
18896/SI-7773
2/8/00
New 3920 schematic - wiring harness, 430305
ccs
4
--
11/22/99
Corrected Section 2.9 Offset Configuration
ccs
3
17861/IN-2439
8/10/99
Updated schematics for CSA
ccp
REV
ECR/ECN
DATE
DESCRIPTION
By
Содержание 3920
Страница 4: ...Model 3920 _________________________________________________________________________________ iii ...
Страница 20: ...Model 3920 _________________________________________________________________Refrigeration Schematics 8 1 ...
Страница 21: ...Model 3920 ____________________________________________________________________Electrical Schematics 8 2 ...
Страница 22: ...Model 3920 ____________________________________________________________________Electrical Schematics 8 3 ...
Страница 23: ...Model 3920 ____________________________________________________________________Electrical Schematics 8 4 ...
Страница 24: ...Model 3920 ____________________________________________________________________Electrical Schematics 8 5 ...