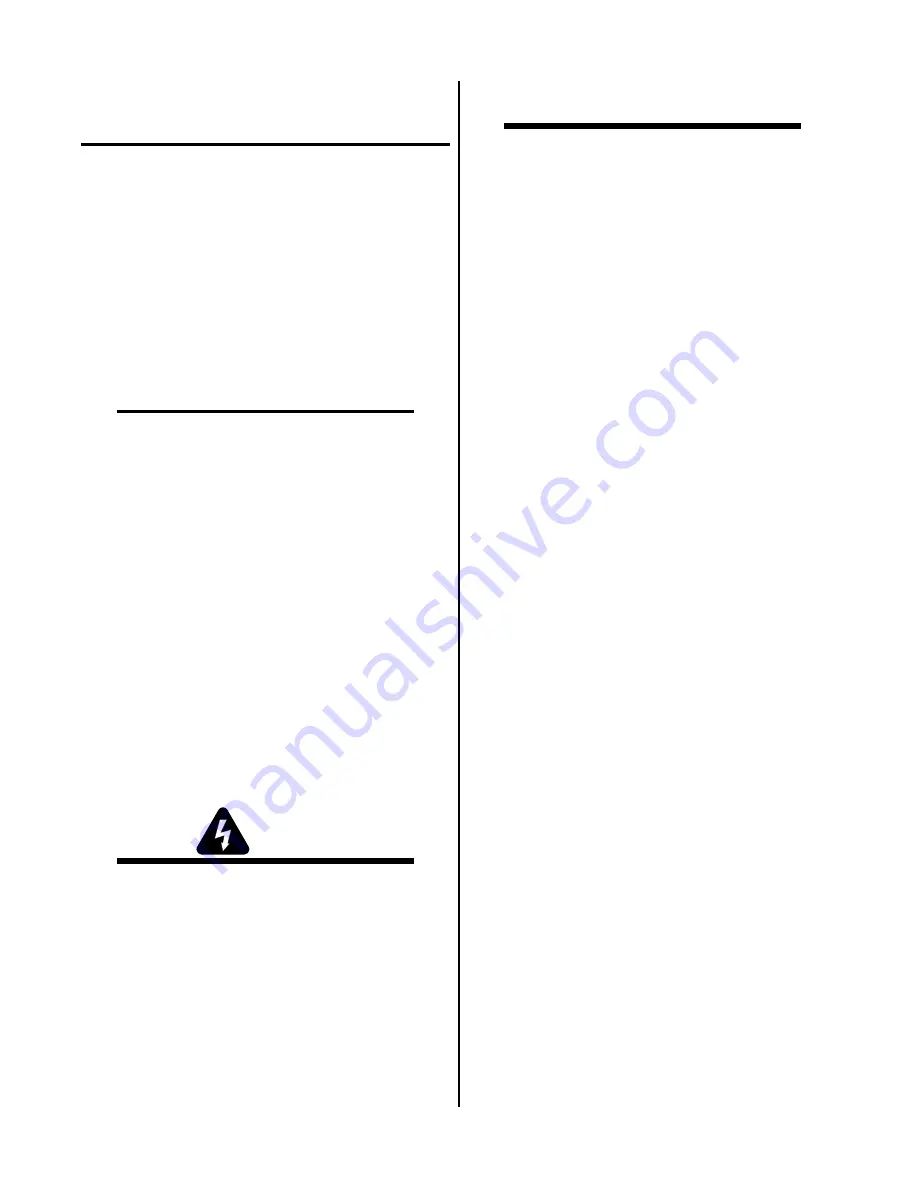
Manual 0-2747
4-1
TROUBLESHOOTING
Section 4:
TROUBLESHOOTING
4.01 Introduction
This section provides service diagnostics for the Pak
Master 75XL PLUS Power Supply, allowing the Techni-
cian to isolate any faulty Subassemblies. Refer to Section
5, Repairs & Replacement Procedures, for parts replace-
ment instructions.
Under no circumstances are field repairs to be attempted
on Printed Circuit Boards or other Subassemblies of this
unit. Evidence of unauthorized repairs will void the fac-
tory warranty.
NOTE
The troubleshooting contained in this manual is
for the Power Supply only. Troubleshooting other
parts of the system is covered in the separate manu-
als for those products.
4.02 Periodic Inspection &
Procedures
This subsection describes inspection procedures which
should be performed at periodic intervals as required.
A. Physical Inspection
Check that all cable connections are secure.
B. Cleaning
Unit should be cleaned per Appendix 11, Maintenance
Schedule.
4.03 Common Operating Problems
WARNINGS
Disconnect primary power at the source before dis-
assembling the power supply, torch, or torch leads.
Frequently review the Important Safety Precau-
tions (Section 1). Be sure the operator is equipped
with proper gloves, clothing, eye and ear protec-
tion. Make sure no part of the operator’s body comes
into contact with the workpiece while the torch is
activated.
Sparks from the cutting process can cause damage
to coated, painted, and other surfaces such as glass,
plastic and metal.
Handle torch leads with care and protect them from
damage.
A. Piloting
Piloting is harder on parts life than actual cutting be-
cause the pilot arc is directed from the electrode to
the tip rather than to a workpiece. Whenever possible,
avoid excessive pilot arc time to improve parts life.
B. Torch Standoff
Improper standoff (the distance between the torch tip
and workpiece) can adversely affect tip life as well as
shield cup life. Standoff may also significantly affect
the bevel angle. Reducing standoff generally results
in a more square cut.
C. Edge Starting
For edge starts, hold the torch perpendicular to the
workpiece with the front of the torch tip at the edge
of the workpiece, not touching, at the point where the
cut is to start. When starting at the edge of the plate,
do not pause at the edge and force the arc to “reach”
for the edge of the metal. Establish the cutting arc as
quickly as possible.
D. Direction of Cut
The plasma gas stream swirls as it leaves the torch.
The purpose of the swirl is to maintain a smooth col-
umn of gas. The swirl effect results in one side of a
cut being more square than the other. Viewed along
the direction of travel, the right side of the cut is more
square than the left.
E. Dross
When dross is present on carbon steel, it is commonly
referred to as either “high speed, slow speed, or top
dross”. Dross present on top of the plate is normally
caused by too great a torch to plate distance. "Top
dross" is normally very easy to remove and can often
be wiped off with a welding glove. "Slow speed dross"
is normally present on the bottom edge of the plate.
It can vary from a light to heavy bead, but does not
adhere tightly to the cut edge, and can be easily
scraped off. "High speed dross" usually forms a nar-
row bead along the bottom of the cut edge and is very
difficult to remove. When cutting a troublesome steel,
it is sometimes useful to reduce the cutting speed to
produce "slow speed dross". Any resultant cleanup
can be accomplished by scraping, not grinding.
Содержание Pak Master 75XL Plus
Страница 2: ......
Страница 6: ......
Страница 16: ...INTRODUCTION 2 2 Manual 0 2747...
Страница 49: ...Manual 0 2747 6 5 REPLACEMENT PARTS This page left blank...
Страница 71: ...Manual 0 2747 A 15 APPENDIX Notes...
Страница 72: ...APPENDIX A 16 Manual 0 2747 APPENDIX 12 SYSTEM SCHEMATIC A 02503...
Страница 73: ...Manual 0 2747 A 17 APPENDIX A 02503...
Страница 74: ......