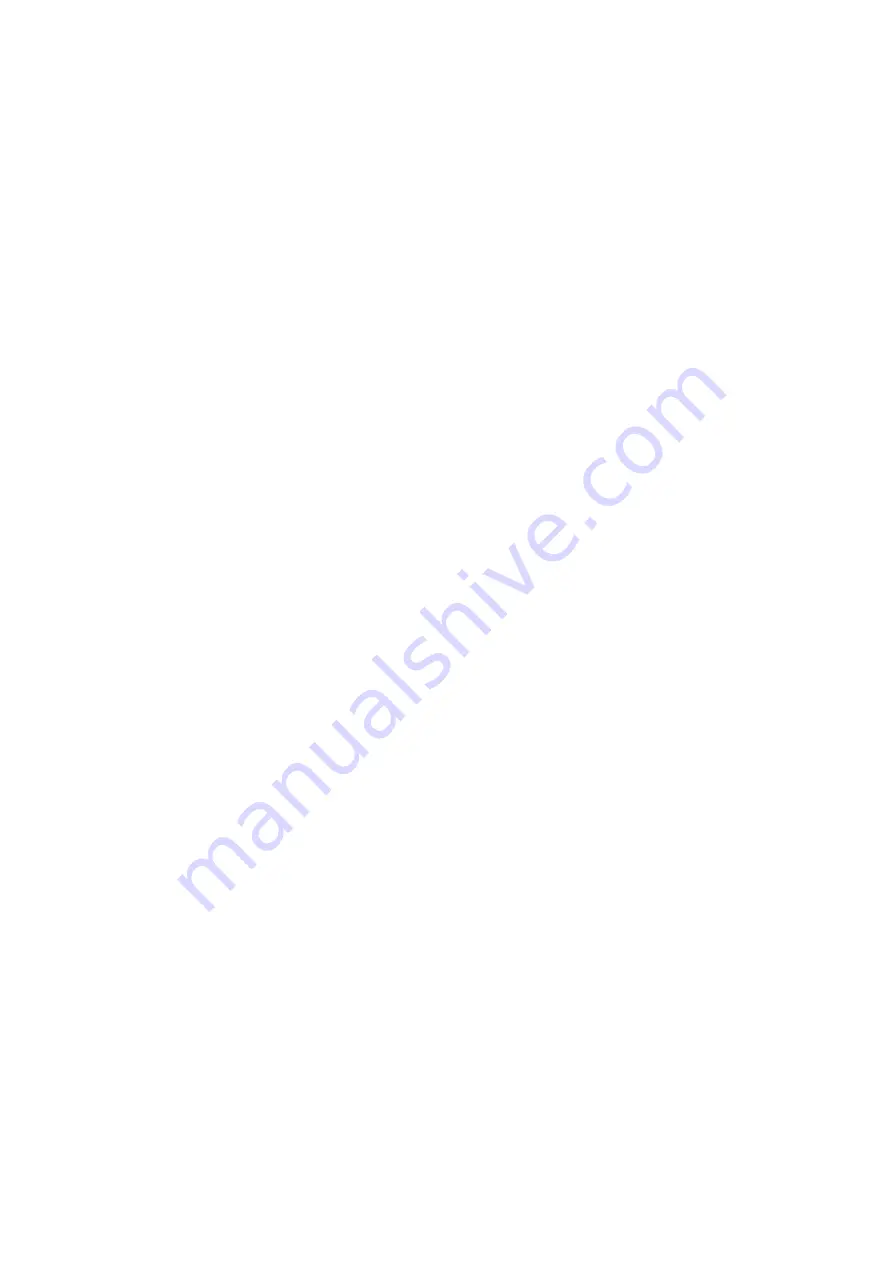
SECTION 5
LYCOMING OPERATOR’S MANUAL
MAINTENANCE PROCEDURES
O-360 AND ASSOCIATED MODELS
d. Generator or Alternator Output –
The generator or alternator (whichever is applicable) should be
checked to determine that the specified voltage and current are being obtained.
2. FUEL SYSTEM.
a. Repair of Fuel Leaks –
In the event a line or fitting in the fuel system is replaced, only a fuel soluble
lubricant such as clean engine oil or Loctite Hydraulic Sealant may be used on tapered threads. Do not
use Teflon tape or any other form of thread compound. Do not apply sealant to the first two threads.
b. Carburetor or Fuel Injector (Except Simmonds Injectors) Fuel Inlet Screen Assembly –
Remove the
assembly and checkthe screen for distortion or openings in the strainer. Replace for either of these
conditions. Clean screen assembly in solvent and dry with compressed air and reinstall. The fuel inlet
screen assembly is tightened to 35-40 in.-lbs. on carburetors and 65-70 in.-lbs. on fuel injectors. The
hexhead plug on pressure carburetor is tightened to 160-175 in.-lbs.
c. Fuel Grade and Limitations –
The recommended aviation grade fuel for the subject engines is listed in
Section 3, Item 8.
In the event that the specified fuel is not available at some locations, it is permissible to use higher
octane fuel. Fuel of a lower octane than specified is not to be used. Under no circumstances should
automotive fuel be used (regardless of octane rating).
NOTE
It is recommended that personnel be familiar with latest revision of Service Instruction No.
1070 regarding specified fuel for Lycoming engines.
d. Air Intake Ducts and Filter –
Checkall air intake ducts for dirt or restrictions. Inspect and service air
filters as instructed in th
e airframe manufacturers handbook.
e. Idle Speed and Mixture Adjustment.
(1) Start the engine and warm up in the usual manner until oil and cylinder head temperatures are
normal.
(2) Check magnetos. If the mag-drop is
normal, proceed with idle adjustment.
(3) Set throttle stop screw so that the engine
idles at the airframe manufacturers recommended
idling RPM. If the RPM changes appreciably after making idle mixture adjustment during the
succeeding steps, readjust the idle speed to the desired RPM.
(4) When the idling speed has been stabilized, move the cockpit mixture control lever with a smooth,
steady pull toward the Idle Cut-Off position and observe the t
achometer for any change during
the leaning process. Caution must be exercised to return the mixture cont
rol to the Full Rich
position before the RPM can drop to a point where the engine cuts out. An increase of more than
50 RPM while leaning out indicates an excessively
rich idle mixture. An immediate decrease in
RPM (if not preceded by a momentary increase) indicates the idle mixture is too lean.
5-4