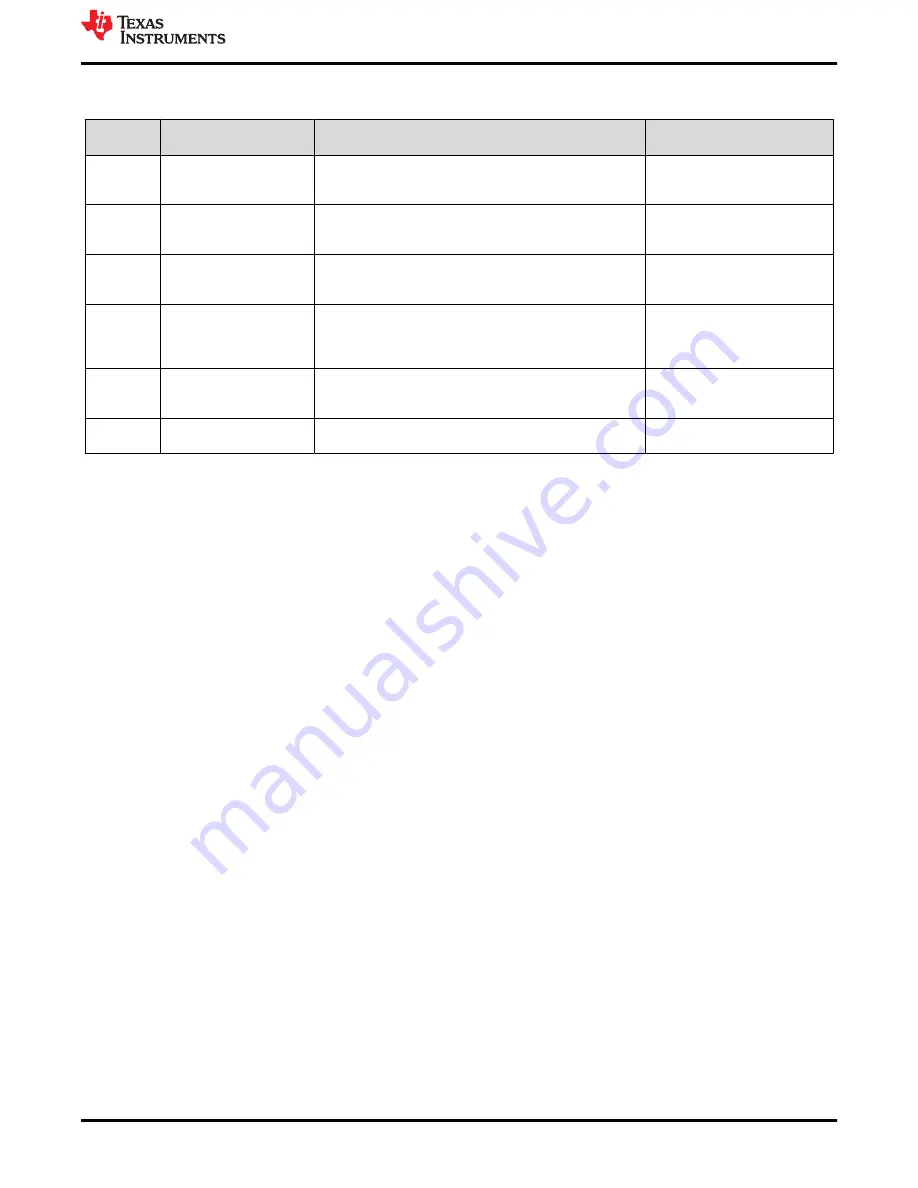
shows the jumpers and switches for the EVM.
Table 5-2. Jumpers and Switches
Jumper
Number
Function
Placement
Comment
JP1
Buck1 enable (EN1)
Connect EN1 to GND to disable Vout1, connect EN1 to Vin
through a 100-kΩ resistor to enable Vout1; Leave open to
enable Vout1
JP2
Buck2 enable (EN2)
Connect EN2 to GND to disable Vout2, connect EN2 to Vin
through a 100-kΩ resistor to enable Vout2; Leave open to
enable Vout2
JP7
I
2
C address
I
2
C address configuration pin. Connect this pin to GND to
set address 0x60H; connect it to Vcc to set address 0x61H;
leave it open to set address 0x62H
On board Vcc is 6.25 V
JP8
Mode
Operation mode control pin. Connect this pin to GND to
set forced PWM mode; leave the pin open to set auto PSM-
PWM; connect this pin to Vcc set the IC to run in current
share mode.
JP9
I
2
C Power
Power connected to the I
2
C IO pull-up resistor; Leave the
two pins un-connected set the power to be 3.3V from the I
2
C
interface adaptor; short the two pins set the power to be Vcc.
On board Vcc is 6.25 V
JP15
I
2
C interface connector
Pin 5 is 3.3 V from adaptor; pin 6 is Ground; pin 9 is SCL, pin
10 is SDA.
5.2 Hardware Requirement
This EVM requires an external power supply capable of providing 4.5 V to 18 V at 7 A.
A function generator capable of driving the SYNC pin with 0.4- to 3.3-V amplitude and a 200-kHz to 1.6-MHz
square wave signal is required for synchronization. The EVM kit includes a USB-TO-GPIO interface box which,
when installed on a PC and connected to the EVM, allows communication with the EVM via a GUI interface. The
minimum PC requirements are:
• Windows
®
2000 or Windows XP operating system
• USB port
• Minimum of 30 MB of free hard disk space (100 MB recommended)
• Minimum of 256 MB of RAM
5.3 Hardware Setup
After connecting the power supply to J1, turn on the power supply, and connect JP1 to Vin through a 100-kΩ
resistor, connect JP2 to Vin through a 100-kΩ resistor, connect JP7 to GND, connect JP8 to GND, the EVM will
regulate the output voltages to the values shown in
. Additional input capacitance may be required in
order to mitigate the inductive voltage droop that may occur during a load transient event.
The output voltage is changed by sending the digital control signal via a PC running the TPS65279V controller
software and USB-TO-GPIO interface box. Change the output voltage with the following steps:
• Connect one end of the USB-TO-GPIO box to the PC using the USB cable and the other end to JP15 of the
TPS65279V using the supplied 10-pin ribbon cable as shown in
. The connectors on the ribbon
cable are keyed to prevent incorrect installation.
• Connect the power supply on J1, and turn on the power supply.
• Run the software as explained in the next section.
Bench Test Setup Conditions
SLVU876A – FEBRUARY 2013 – REVISED MAY 2021
TPS65279V Buck Converter Evaluation Module User's Guide
9
Copyright © 2021 Texas Instruments Incorporated