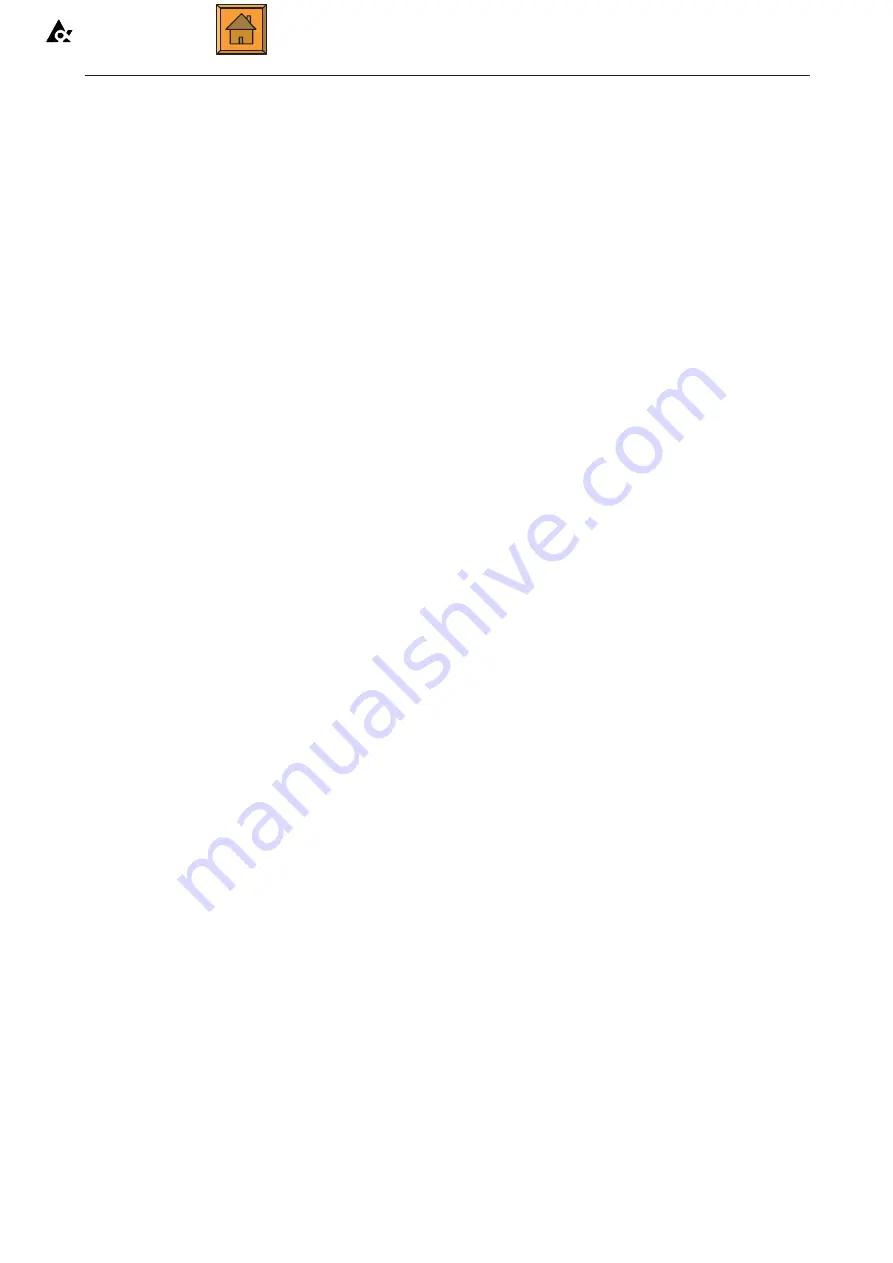
DIN806BC
3-3
Tetra Pak
Hoyer
synchronisation no matter what the production
speed in the SL C tunnel.
Products are supported and transported to the
coating station on stainless steel rollers (Pos. 2,
Fig. 3.1). Each roller carries nine sets of products
picked up together.
A sufficient number of rollers is provided to
permit a one-minute drying and hardening time
for chocolate at the maximum speed of the tunnel.
The rollers are hooked up to a chain positioned on
either side of the body of the machine.
The stainless steel chain has a 70 mm step, is
extensible and does not require lubrication.
The roller conveyor motor (Pos. 12, Fig. 3.1) is
positioned to one side of the machine and
connected to the serrated wheels through an
intermitter; it is driven in step with the line.
A proximity sensor makes the motor stop.
The optional coating station (Pos. 3, Fig. 3.1)
consists of a set of tanks assembled on wheels so that
they can easily be removed for washing and
maintenance.
Level control is not automatic and so the level in
the tanks must be topped up manually from time to
time during production.
The tank unit consists of a stationary body made of
stainless steel surrounded by a space which is
filled with water to keep the chocolate at the
correct temperature and a tank with raising/lowering
motion to contain the chocolate for coating the
products.
The water is kept at the correct temperature by an
immersed electrical resistor.
A pump designed on the principle of the
Archimedean screw carries chocolate and nut bits
(if any) from the stationary tank to the mobile tank.
The level of chocolate in the mobile tank is maintained
by allowing chocolate to overflow out of the mobile
tank into the stationary tank below it.
The shape of the tank permits collection of drops of
chocolate which fall of products during the first 20
seconds of drying.
The raising and lowering motion is created by a
pneumatic cylinder connected to the pick-up
machine programme, which raises the tank when the
roller is positioned above the mobile tank and lowers
it before the roller moves on for the next cycle.
The Hoyer Dino C multiple row pick-up machine
may also be equipped with a fruit juice coating
station, which consists of a product pre-cooling
area in which the first three rows of products are
immersed in liquid nitrogen while the two rows
behind them are immersed in fruit juice. After the
four stages involved in hardening the juice, the
last two rows are immersed in the liquid nitrogen.
The maximum thickness of the fruit juice layer is
1 to 1.5 mm.
The last station in the multiple row pick-up machine
is the product rejection station (Pos. 8, Fig. 3.1),
with automatic step conveyance on a belt with
lamellas which is synchronised with the line.
The operator interface panel on the door of the
electrical cabinet (Pos. 3, Fig. 3.1) may be used to
select a working programme and modify the factory
settings to optimise operation of the machine
under actual operating conditions, which may
vary in accordance with the type of product being
made.
The pick-up machine is run by a PLC with a
programme capable of synchronising the belts
that travel through the cooling tunnel of the line
for coating products without sticks. When
producing products without sticks, such as bars,
an optional smooth belt (Pos. 5, Fig. 3.1). must be
positioned on top of the roller for removal and
conveyance of products arriving from the pick-up
station to the Hoyer Hoyrobe 350 coating machine.
The speed of the evacuation belt is controlled by
an inverter which is set automatically by the
tunnel programme; when the operator adjusts the
speed of production in the tunnel, the belt speed
and following movement are automatically
adjusted.
RETURN TO PM
Содержание Hoyer Dino C
Страница 41: ...DIN806BI 9 11 Tetra Pak Hoyer Fig 9 6 Opening of load grippers 4 1 1 2 2 3 3 RETURN TO PM LAY OUT LIST...
Страница 47: ...DIN806BI 9 17 Tetra Pak Hoyer Fig 9 9 Translation 2 2 2 2 3 4 2 2 2 2 3 4 3 5 3 1 RETURN TO PM LAY OUT LIST...
Страница 49: ...DIN806BI 9 19 Tetra Pak Hoyer Fig 9 10 Translation 4 3 2 1 5 11 9 10 9 8 7 6 RETURN TO PM LAY OUT LIST...
Страница 51: ...DIN806BI 9 21 Tetra Pak Hoyer Fig 9 11 Stick roller 3 2 3 2 3 2 3 2 1 3 2 2 RETURN TO PM LAY OUT LIST...
Страница 55: ...DIN806BI 9 25 Tetra Pak Hoyer Fig 9 13 Stick pick up 4 3 2 7 6 7 6 5 5 1 RETURN TO PM LAY OUT LIST...
Страница 57: ...DIN806BI 9 27 Tetra Pak Hoyer Fig 9 14 Candy bar pick up 15 RETURN TO PM LAY OUT LIST...
Страница 61: ...DIN806BI 9 31 Tetra Pak Hoyer Fig 9 16 Cone pick up 2 3 4 4 5 6 7 8 8 9 9 1 RETURN TO PM LAY OUT LIST...
Страница 65: ...DIN806BI 9 35 Tetra Pak Hoyer Fig 9 18 Wafer cup pick up 2 3 4 4 5 6 7 7 8 8 1 RETURN TO PM LAY OUT LIST...
Страница 67: ...DIN806BI 9 37 Tetra Pak Hoyer Fig 9 19 Bricket pick up 6 8 6 7 6 8 3 2 5 4 9 1 RETURN TO PM LAY OUT LIST...
Страница 71: ...DIN806BI 9 41 Tetra Pak Hoyer Fig 9 21 Juice coating device 3 2 1 9 20 9 22 9 23 9 24 RETURN TO PM LAY OUT LIST...
Страница 79: ...DIN806BI 9 49 Tetra Pak Hoyer Fig 9 25 Chocolate tank 2 4 1 3 4 6 8 9 10 5 7 11 11 11 RETURN TO PM LAY OUT LIST...