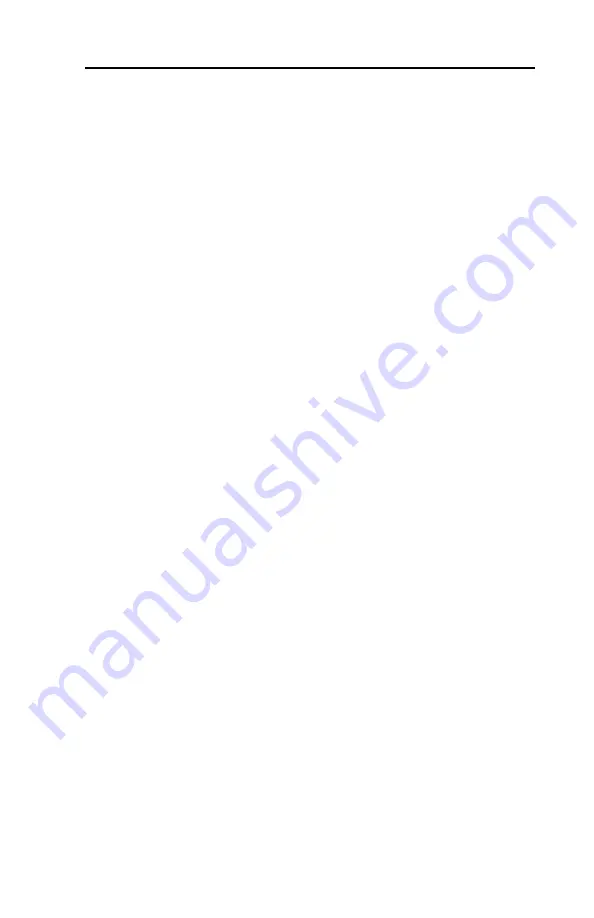
7.12 General Undercarriage Information
The undercarriage assemblies typically operate in harsh working conditions. They
work in mud, gravel, debris and various other abrasive materials during operation.
A daily inspection of the undercarriage assemblies and cleaning if necessary is
recommended.
Materials that are particularly sticky or abrasive like clay, mud, or gravel should
be cleaned from the undercarriages often to minimize component wear. A pres-
sure washer works well for cleaning materials from the undercarriages. At times
when a pressure washer is not available, use a bar, shovel or similar device to
carefully remove foreign materials.
When cleaning, pay particular attention to the drive motors/sprockets and the
front and rear wheels where debris is likely to accumulate. If working in scrap or
debris, inspect the undercarriages more often and remove foreign objects that
may wrap around or lodge themselves between components causing premature
wear and damage.
Operation on sand, turf, or other finished surfaces may require less frequent
cleaning, but daily inspection is still advised.
7.13 Track Tension Check
Proper track tension is important for optimum performance and maximum track
life. Operating with tracks that are too loose can cause them to misfeed, possibly
causing damage. During the first 50 hours of operation, the tracks will "break-in",
and may require adjustment.
To check for proper track adjustment:
1.
Drive the machine forward 5 ft (1.5 m) to remove slack from the lower and
rear portions of the track. Stop the engine and remove the key from the
ignition.
2.
Lay a straight edge along the top of the track, across the sprocket and the
front idler wheel (fig. 7.13-1).
3.
Using a rope or wire, put 90 lb (41 kg) of down force on the track at the mid
point between the sprocket and idler.
4.
Using a ruler or tape, measure the distance between the straight edge and
track (fig. 7.13-2). The track should not deflect more than 3/4 in. (1.9 cm)
between the top of the track and the straight edge.
5.
If the track does deflect more than 3/4 in. (1.9 cm), tighten the track until
within specification.
7 MAINTENANCE
71
RT-60/R160T/R190T ROW O&M
0404-659 2016-05
Содержание R190T-ROW
Страница 7: ...6 RT 60 R160T R190T ROW O M 0404 659 2016 05 This Page Intentionally Left Blank...
Страница 29: ...28 RT 60 R160T R190T ROW O M 0404 659 2016 05 This Page Intentionally Left Blank...
Страница 31: ...30 RT 60 R160T R190T ROW O M 0404 659 2016 05 This Page Intentionally Left Blank...
Страница 37: ...36 RT 60 R160T R190T ROW O M 0404 659 2016 05 This Page Intentionally Left Blank...
Страница 47: ...46 RT 60 R160T R190T ROW O M 0404 659 2016 05 This Page Intentionally Left Blank...
Страница 57: ...56 RT 60 R160T R190T ROW O M 0404 659 2016 05 This Page Intentionally Left Blank...
Страница 61: ...60 RT 60 R160T R190T ROW O M 0404 659 2016 05 This Page Intentionally Left Blank...
Страница 63: ...62 RT 60 R160T R190T ROW O M 0404 659 2016 05 This Page Intentionally Left Blank...
Страница 85: ......