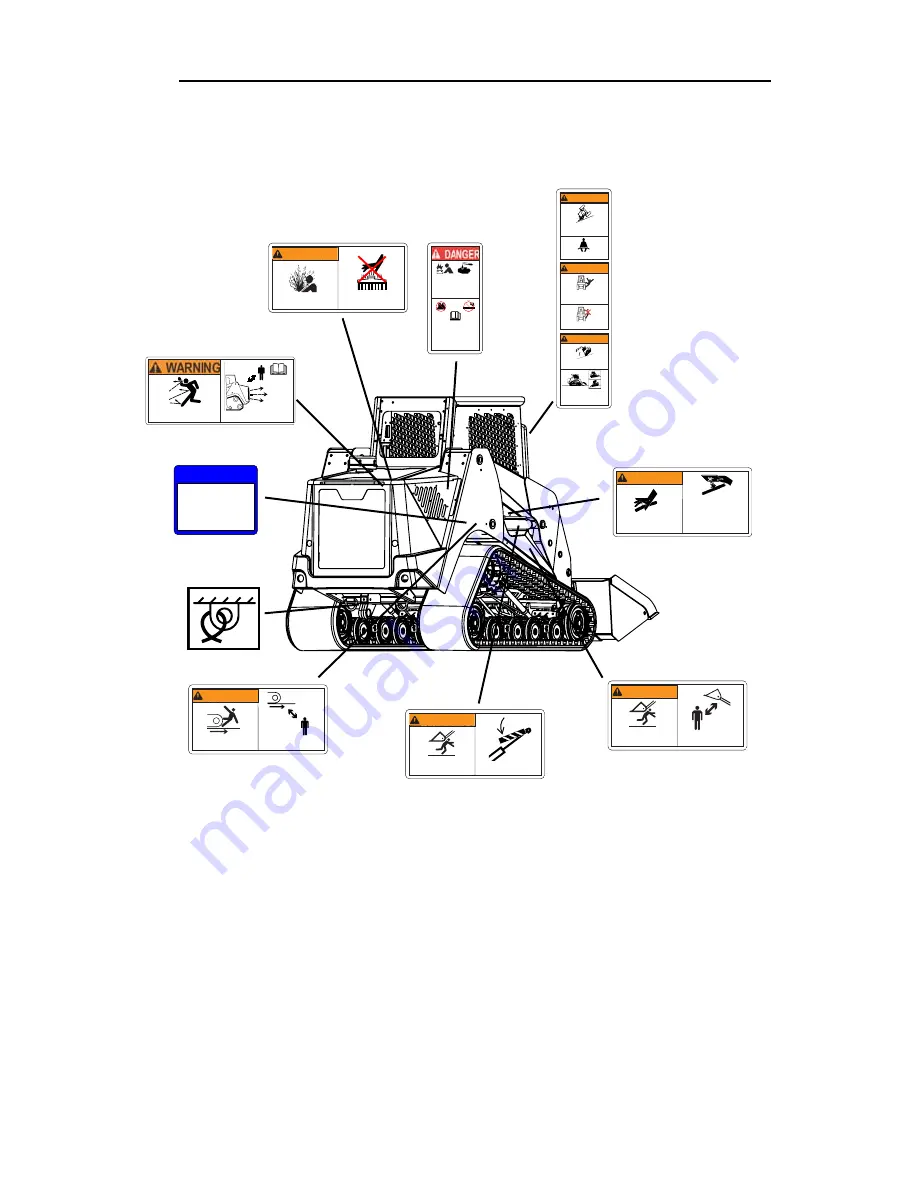
Note:
If any of the safety signs shown in this section are missing or damaged, contact
your dealer to obtain a replacement.
Key
(continued)
11.
Burn hazard (engine compartment)
12.
Explosion / burn hazard (read operator’s manual) (engine compartment)
13.
Crush hazard / fall hazard / rollover/ejection hazard (inside cab)
14.
Skin (oil) injection hazard
15.
Crush hazard (lift arms)
16.
Crush hazard (lift arm brace)
17.
Crush hazard (run over)
18.
Tie down location
19.
Clean undercarriages notice
20.
Flying Debris (100G Forestry only)
Burn Hazard
Hot fluid under pressure can scald.
Allow the machine to cool thoroughly
before opening.
2030-595
Explosion/Burn Hazard
Will cause death, burns or
blindness due to ignition of
explosive gasses or contact
with corrosive acid.
•
Keep all flames/sparks
away!
•
No Smoking!
•
Read and understand
all manuals prior to
operation.
2030-603
11
12
CRUSH HAZARD
Contact with moving machine can
result in death or serious injury.
Keep clear of moving machine.
2030-593
Crush Hazard
Rollover can crush and result in
serious injury or death.
Fasten Seat Belt
Fall Hazard
Falling from a machine can result
in serious injury or death
No Riders
Rollover/Ejection Hazard
Serious injury or death can result.
Carry loads low. Load unload and
turn on level ground. Travel on
inclines with heaviest end of
machine uphill.
2046-300
Crush Hazard
Death or serious injury can result
from contact with moving lift arm or
attachment.
Keep clear of lift arms and
attachments.
2030-592
Injection Hazard
Escaping fluid under pressure can
penetrate skin, causing serious injury.
•
Relieve internal pressure before
disconnecting any line or fitting.
•
Keep away from leaks or pinholes.
•
Use cardboard to check for leaks.
Fluid injected into skin must be surgi-
cally removed within a few hours by a
doctor familiar with this type of injury
or gangrene will result.
2030-602
14
15
13
17
18
Crush Hazard
Death or serious injury can result
from contact with moving lift arm or
attachment.
Install lift arm brace prior to servicing.
2030-594
16
15
2 SAFETY
Inspect undercarriages daily for
accumulation of debris. If debris
is present, clean thoroughly with
a pressure washer. If debris is
allowed to build up, it can cause
premature component wear and
decrease machine performance.
2085-253
NOTICE
19
WARNING
WARNING
WARNING
WARNING
WARNING
WARNING
WARNING
WARNING
2076-386
FLYING DEBRIS
Contact with flying debris can result in
death or serious injury.
Stay clear of rear of machine.
20
Содержание DTM 00101 (standard)
Страница 2: ......
Страница 6: ...4...
Страница 8: ...6...
Страница 34: ...32...
Страница 36: ...34...
Страница 42: ...40...
Страница 62: ...60...
Страница 72: ...70...
Страница 78: ...76...
Страница 99: ...SERVICE LOG 97 Hours Service Performed Notes...
Страница 100: ...SERVICE LOG 98 Hours Service Performed Notes...
Страница 101: ...SERVICE LOG 99 Hours Service Performed Notes...
Страница 102: ......