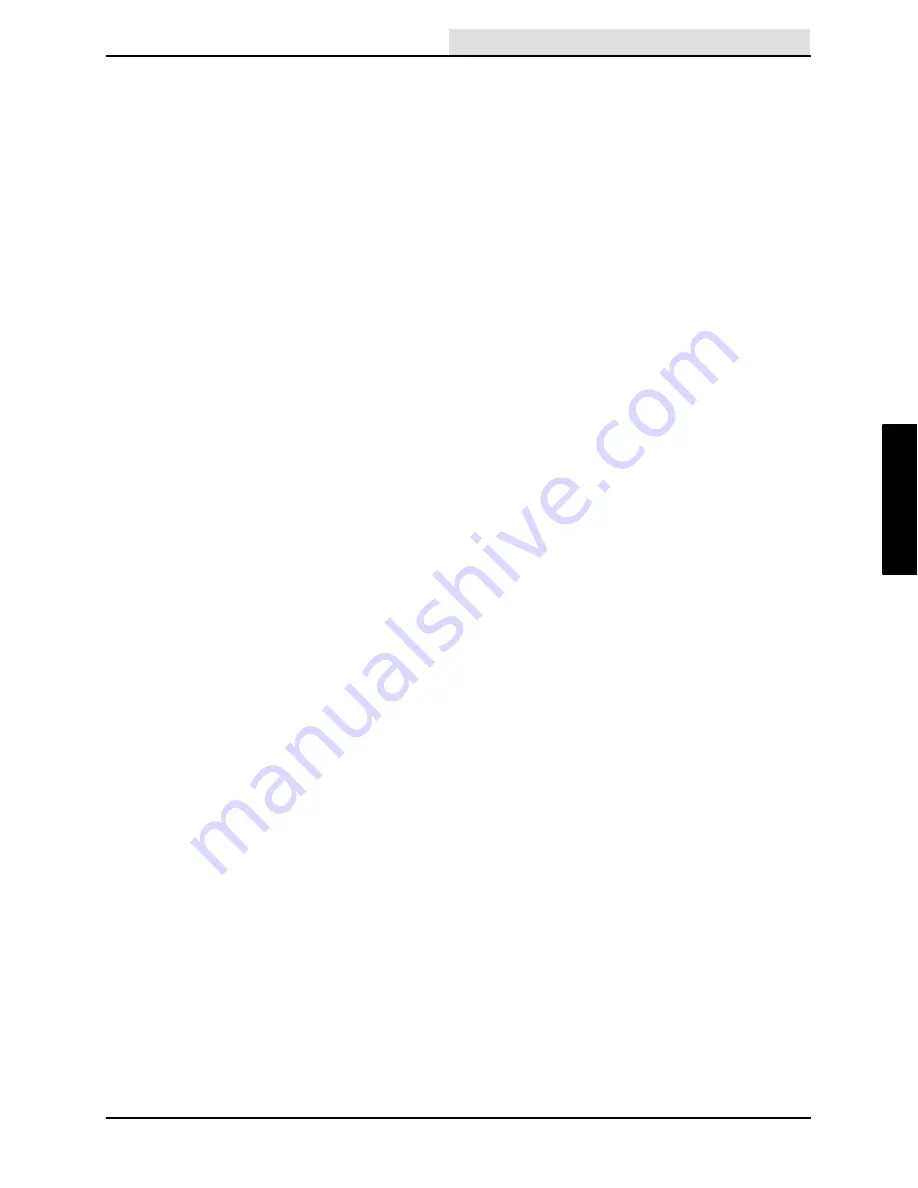
SWEEPING
3-1
6500/6550 330275 (5--02)
CONTENTS
Page
INTRODUCTION
3-3
. . . . . . . . . . . . . . . . . . . . . .
DEBRIS HOPPER
3-4
. . . . . . . . . . . . . . . . . .
TO REMOVE HOPPER FROM
MACHINE
3-4
. . . . . . . . . . . . . . . . . . .
TO INSTALL HOPPER
3-6
. . . . . . . . . . .
TO ADJUST AND LEVEL HOPPER
HEIGHT
3-8
. . . . . . . . . . . . . . . . . . . . .
THERMO SENTRY
t
3-9
. . . . . . . . . . . .
TO REPLACE
THERMO SENTRY
t
3-9
. . . . . . .
HOPPER DUST FILTER
3-10
. . . . . . . . .
TO REPLACE HOPPER DUST
FILTER
3-11
. . . . . . . . . . . . . . . . . . . . .
HOPPER DUMP DOOR
3-14
. . . . . . . . .
TO ADJUST HOPPER DUST
DUMP DOOR
3-14
. . . . . . . . . . . . . . .
TO REMOVE HOPPER DUMP
DOOR
3-14
. . . . . . . . . . . . . . . . . . . . .
TO INSTALL HOPPER DUMP
DOOR
3-16
. . . . . . . . . . . . . . . . . . . . .
BRUSHES
3-17
. . . . . . . . . . . . . . . . . . . . . . . .
MAIN BRUSH
3-17
. . . . . . . . . . . . . . . . . .
TO REPLACE MAIN BRUSH
(For all 6550 and 6500 model
machines below serial
number 20000)
3-18
. . . . . . . .
TO REPLACE MAIN BRUSH
(For 6500 model machines serial
number 20000 and above)3-19
TO CHECK AND ADJUST MAIN
BRUSH PATTERN (For all 6550
and 6500 model machines below
serial number 20000)
3-20
. .
TO CHECK AND ADJUST MAIN
BRUSH PATTERN (For 6500 model
machines serial number 20000
and above)
3-22
. . . . . . . . . . .
TO REPLACE MAIN BRUSH IDLER
PLUG BEARINGS
3-24
. . . . . . . . . . .
TO REPLACE BRUSH SHAFT BEARINGS
(For all 6550 and 6500 model machines
below serial number 20000) 3-25
TO REPLACE BRUSH SHAFT BEARINGS
(For 6500 model machines serial
number 20000 and above)
3-27
.
Page
SIDE BRUSH
3-29
. . . . . . . . . . . . . . . . . .
TO REPLACE SIDE BRUSH
3-30
. .
SIDE BRUSH GUARD
3-31
. . . . . . . . . .
TO ROTATE OR REPLACE
SIDE BRUSH GUARD
3-31
. . . . .
SKIRTS AND SEALS
3-32
. . . . . . . . . . . . . .
HOPPER LIP SKIRTS
3-32
. . . . . . . . . . .
TO REPLACE HOPPER LIP
SKIRTS
3-32
. . . . . . . . . . . . . . . . . . . .
BRUSH DOOR SKIRTS
3-33
. . . . . . . . .
TO REPLACE AND ADJUST BRUSH
DOOR SKIRTS
3-33
. . . . . . . . . . . . . .
REAR SKIRT AND DEFLECTOR
BLADE
3-35
. . . . . . . . . . . . . . . . . . . . .
TO REPLACE AND ADJUST THE
REAR SKIRT AND DEFLECTOR
BLADE
3-35
. . . . . . . . . . . . . . . . . .
BRUSH DOOR SEALS
3-36
. . . . . . . . . .
HOPPER SEALS
3-36
. . . . . . . . . . . . . . .
TO REPLACE HOPPER SEALS
3-37
. .
HOPPER INSPECTION DOOR
SEAL
3-38
. . . . . . . . . . . . . . . . . . . . . .
HOPPER DOOR SEALS
3-38
. . . . . . . .
TO REPLACE HOPPER DOOR
SEALS
3-38
. . . . . . . . . . . . . . . . . . . . .
HOPPER COVER SEAL
3-40
. . . . . . . . .
HOPPER DUST SEAL
3-40
. . . . . . . . . .
HOPPER VACUUM FAN SEAL
3-40
. . .
HOPPER FILTER SEALS
3-40
. . . . . . . .
HOPPER LIFT ARM
3-41
. . . . . . . . . . . .
TO REMOVE HOPPER LIFT ARM 3-41
TO INSTALL HOPPER LIFT ARM 3-42
VACUUM FAN
3-43
. . . . . . . . . . . . . . . . . . . .
TO REMOVE VACUUM FAN
ASSEMBLY
3-43
. . . . . . . . . . . . . . . . .
TO INSTALL VACUUM FAN
ASSEMBLY
3-44
. . . . . . . . . . . . . . . . .
TO REPLACE VACUUM FAN
IMPELLER
3-45
. . . . . . . . . . . . . . . . . .
MACHINE TROUBLESHOOTING
3-47
. . .
Содержание 6500
Страница 1: ...6500 6550 330275 Rev 02 5 02 Service Manual Gas LP Diesel 330275 ...
Страница 24: ...GENERAL INFORMATION 6500 6550 330275 5 02 1 22 ...
Страница 26: ...CHASSIS 6500 6550 330275 6 98 2 2 ...
Страница 36: ...CHASSIS 6500 6550 330275 6 98 2 12 ...
Страница 38: ...SWEEPING 6500 6550 330275 5 02 3 2 ...
Страница 84: ...SWEEPING 6500 6550 330275 6 98 3 48 ...
Страница 149: ...ELECTRICAL 4 65 6500 6550 330275 6 98 Volts D C C B 6 1E RED 22 YELLOW ...
Страница 182: ...ELECTRICAL 6500 6550 330275 5 02 4 98 ...
Страница 184: ...HYDRAULICS 6500 6550 330275 6 98 5 2 ...
Страница 209: ...HYDRAULICS 5 27 6500 6550 330275 5 02 ...
Страница 210: ...HYDRAULICS 6500 6550 330275 6 01 5 28 6500 HYDRAULIC SCHEMATIC METAL HOPPER 1 2 3 4 5 ...
Страница 211: ...HYDRAULICS 5 29 6500 6550 330275 6 01 6500 HYDRAULIC SCHEMATIC METAL HOPPER 1 2 3 4 5 351757 6500 NA ...
Страница 212: ...HYDRAULICS 6500 6550 330275 6 01 5 30 6500 HYDRAULIC SCHEMATIC PLASTIC HOPPER 1 2 3 4 5 ...
Страница 213: ...HYDRAULICS 5 31 6500 6550 330275 6 01 6500 HYDRAULIC SCHEMATIC PLASTIC HOPPER 1 2 3 4 5 351757 6500 NA ...
Страница 214: ...HYDRAULICS 6500 6550 330275 6 01 5 32 6550 HYDRAULIC SCHEMATIC 1 2 7 3 4 5 6 351758 6550 ...
Страница 215: ...HYDRAULICS 5 33 6500 6550 330275 6 01 6550 HYDRAULIC SCHEMATIC 1 2 7 3 4 5 6 351758 6550 ...
Страница 216: ...HYDRAULICS 6500 6550 330275 6 01 5 34 6500 HYDRULIC HOSE GROUP METAL HOPPER E C A B D F IN OUT BYD R P L T IN OUT ...
Страница 217: ...HYDRAULICS 5 35 6500 6550 330275 6 01 6500 HYDRULIC HOSE GROUP PLASTIC HOPPER E C A B D F IN OUT BYD R P L T IN OUT ...
Страница 218: ...HYDRAULICS 6500 6550 330275 6 01 5 36 6550 HYDRULIC HOSE GROUP IN A B D F C E BYD R P L T IN OUT 351758 ...
Страница 245: ......
Страница 246: ......
Страница 247: ......
Страница 248: ......
Страница 249: ......
Страница 250: ......
Страница 251: ......
Страница 252: ......
Страница 253: ......
Страница 254: ......
Страница 255: ......
Страница 256: ......
Страница 257: ......
Страница 258: ......
Страница 259: ......
Страница 260: ......
Страница 261: ......
Страница 262: ......
Страница 263: ......
Страница 264: ......
Страница 265: ......
Страница 266: ......
Страница 267: ......
Страница 268: ......
Страница 269: ......
Страница 270: ......
Страница 271: ......
Страница 272: ......
Страница 290: ...18 18 Model 70142 70144 and 70145 Notes ...
Страница 291: ...19 19 Model 70142 70144 and 70145 Notes ...
Страница 294: ...ENGINE G LPG 6500 6550 330275 6 98 6 2 ...
Страница 330: ...ENGINE G LPG 6500 6550 330275 5 02 6 38 ...
Страница 332: ...ENGINE D 6500 6550 330275 6 98 7 2 ...