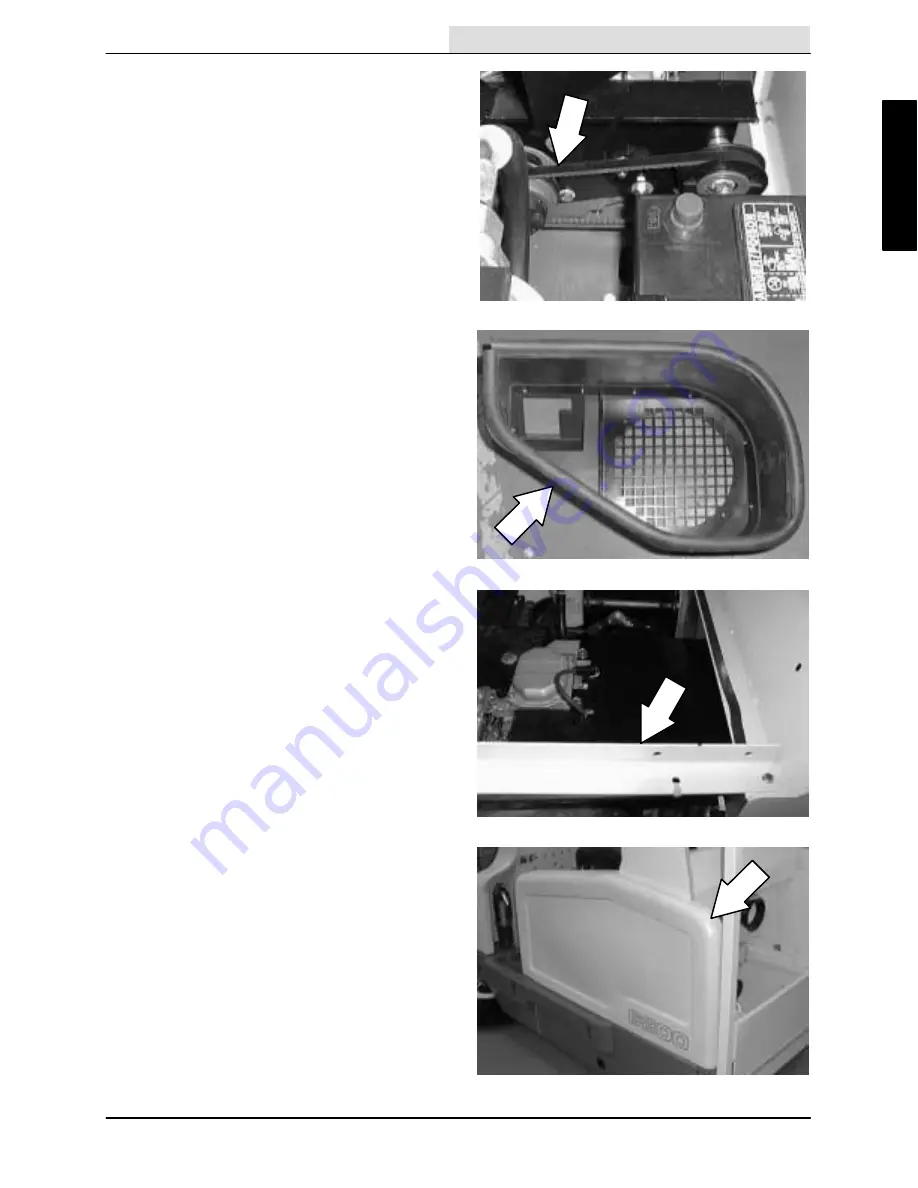
ENGINE–GAS/LP
6-19
6200G/LP 330375 (6–99)
10. Reinstall the jackshaft V–belt onto the
sheave on the engine and the two idler
sheaves. Pull the idler tight and tighten the
hardware.
11. Reinstall the air duct baffle assembly onto
the left side of the engine.
12. Reinstall the left hand side brace onto the
machine panels.
13. Reinstall the left hand side panel.
Содержание 6200G
Страница 1: ...330375 Rev 00 6 99 Service Manual 6200G LP ...
Страница 4: ...GENERAL INFORMATION 1 2 6200G LP 330375 6 99 ...
Страница 12: ...GENERAL INFORMATION 1 10 6200G LP 330375 6 99 ...
Страница 18: ...GENERAL INFORMATION 1 16 6200G LP 330375 6 99 ...
Страница 20: ...CHASSIS 2 2 6200G LP 330375 6 99 ...
Страница 74: ...CHASSIS 2 56 6200G LP 330375 6 99 ...
Страница 76: ...SWEEPING 3 2 6200G LP 330375 6 99 ...
Страница 138: ...ELECTRICAL 4 2 6200G LP 330375 6 99 ...
Страница 172: ...ELECTRICAL 4 36 6200G LP 330375 6 99 ...
Страница 173: ...ELECTRICAL 4 37 6200G LP 330375 6 99 Fig 1 Electrical Schematic Gas 352982 ...
Страница 174: ...ELECTRICAL 4 38 6200G LP 330375 6 99 Fig 2 Electrical Schematic LPG 352983 ...
Страница 175: ...ELECTRICAL 4 39 6200G LP 330375 6 99 Fig 3 Wire Harnesses Group ...
Страница 176: ...ELECTRICAL 4 40 6200G LP 330375 6 99 Fig 3 Wire Harnesses Group 3 3 ...
Страница 177: ...ELECTRICAL 4 41 6200G LP 330375 6 99 Fig 3 Wire Harnesses Group ...
Страница 178: ...ELECTRICAL 4 42 6200G LP 330375 6 99 ...
Страница 181: ...ELECTRICAL 4 45 6200G LP 330375 6 99 S Fig 1 ...
Страница 182: ...ELECTRICAL 4 46 6200G LP 330375 6 99 S Fig 2 ...
Страница 184: ...ELECTRICAL 4 48 6200G LP 330375 6 99 S Fig 3 ...
Страница 186: ...ELECTRICAL 4 50 6200G LP 330375 6 99 S Fig 4 ...
Страница 187: ...ELECTRICAL 4 51 6200G LP 330375 6 99 S Fig 5 ...
Страница 189: ...ELECTRICAL 4 53 6200G LP 330375 6 99 S Fig 6 ...
Страница 190: ...ELECTRICAL 4 54 6200G LP 330375 6 99 S Fig 7 ...
Страница 191: ...ELECTRICAL 4 55 6200G LP 330375 6 99 S Fig 8 ...
Страница 192: ...ELECTRICAL 4 56 6200G LP 330375 6 99 S Fig 9 ...
Страница 194: ...ELECTRICAL 4 58 6200G LP 330375 6 99 S Fig 1 ...
Страница 195: ...ELECTRICAL 4 59 6200G LP 330375 6 99 s Fig 2 ...
Страница 197: ...ELECTRICAL 4 61 6200G LP 330375 6 99 S Fig 3 ...
Страница 199: ...ELECTRICAL 4 63 6200G LP 330375 6 99 S Fig 4 ...
Страница 200: ...ELECTRICAL 4 64 6200G LP 330375 6 99 S Fig 5 ...
Страница 202: ...ELECTRICAL 4 66 6200G LP 330375 6 99 S Fig 6 ...
Страница 203: ...ELECTRICAL 4 67 6200G LP 330375 6 99 S Fig 7 ...
Страница 204: ...ELECTRICAL 4 68 6200G LP 330375 6 99 S Fig 8 ...
Страница 205: ...ELECTRICAL 4 69 6200G LP 330375 6 99 S Fig 9 ...
Страница 206: ...ELECTRICAL 4 70 6200G LP 330375 6 99 ...
Страница 208: ...HYDRAULICS 5 2 6200G LP 330375 6 99 ...
Страница 236: ...HYDRAULICS 5 30 6200G LP 330375 6 99 HYDRAULIC SCHEMATIC PROPEL ...
Страница 237: ...HYDRAULICS 5 31 6200G LP 330375 6 99 HYDRAULIC SCHEMATIC HOPPER LIFT ...
Страница 238: ...HYDRAULICS 5 32 6200G LP 330375 6 99 OUT IN B A B A HYDRAULIC HOSE DIAGRAM PROPEL ...
Страница 239: ...HYDRAULICS 5 33 6200G LP 330375 6 99 HYDRAULIC HOSE DIAGRAM HOPPER LIFT ...
Страница 243: ......
Страница 244: ......
Страница 245: ......
Страница 246: ......
Страница 247: ......
Страница 248: ......
Страница 249: ......
Страница 250: ......
Страница 251: ......
Страница 252: ......
Страница 253: ......
Страница 254: ......
Страница 255: ......
Страница 256: ......
Страница 257: ......
Страница 258: ......
Страница 259: ......
Страница 260: ......
Страница 261: ......
Страница 262: ......
Страница 263: ......
Страница 264: ......
Страница 265: ......
Страница 266: ......
Страница 267: ......
Страница 268: ......
Страница 269: ......
Страница 270: ......
Страница 271: ......
Страница 272: ......
Страница 274: ...ENGINE GAS LP 6 2 6200G LP 330375 6 99 ...
Страница 293: ......
Страница 294: ......
Страница 295: ......
Страница 296: ......
Страница 297: ......
Страница 298: ......
Страница 299: ......
Страница 300: ......
Страница 301: ......
Страница 302: ......
Страница 303: ......
Страница 304: ......
Страница 305: ......
Страница 306: ......
Страница 307: ......
Страница 308: ......
Страница 309: ......
Страница 310: ......
Страница 311: ......
Страница 312: ......
Страница 313: ......
Страница 314: ......
Страница 315: ......
Страница 316: ......
Страница 317: ......
Страница 318: ......
Страница 319: ......
Страница 320: ......
Страница 321: ......
Страница 322: ......
Страница 323: ......
Страница 324: ......
Страница 325: ......
Страница 326: ......
Страница 327: ......
Страница 328: ......
Страница 329: ......
Страница 330: ......
Страница 331: ......
Страница 332: ......
Страница 333: ......
Страница 334: ......
Страница 335: ......
Страница 336: ......
Страница 337: ......
Страница 338: ......
Страница 339: ......
Страница 340: ......
Страница 341: ......
Страница 342: ......
Страница 343: ......
Страница 344: ......
Страница 345: ......
Страница 346: ......
Страница 347: ......
Страница 348: ......
Страница 349: ......
Страница 350: ......
Страница 351: ......
Страница 352: ......
Страница 353: ......
Страница 354: ......
Страница 355: ......
Страница 356: ......
Страница 357: ......
Страница 358: ......
Страница 359: ......
Страница 360: ......
Страница 361: ......
Страница 362: ......
Страница 363: ......
Страница 364: ......
Страница 365: ......
Страница 366: ......