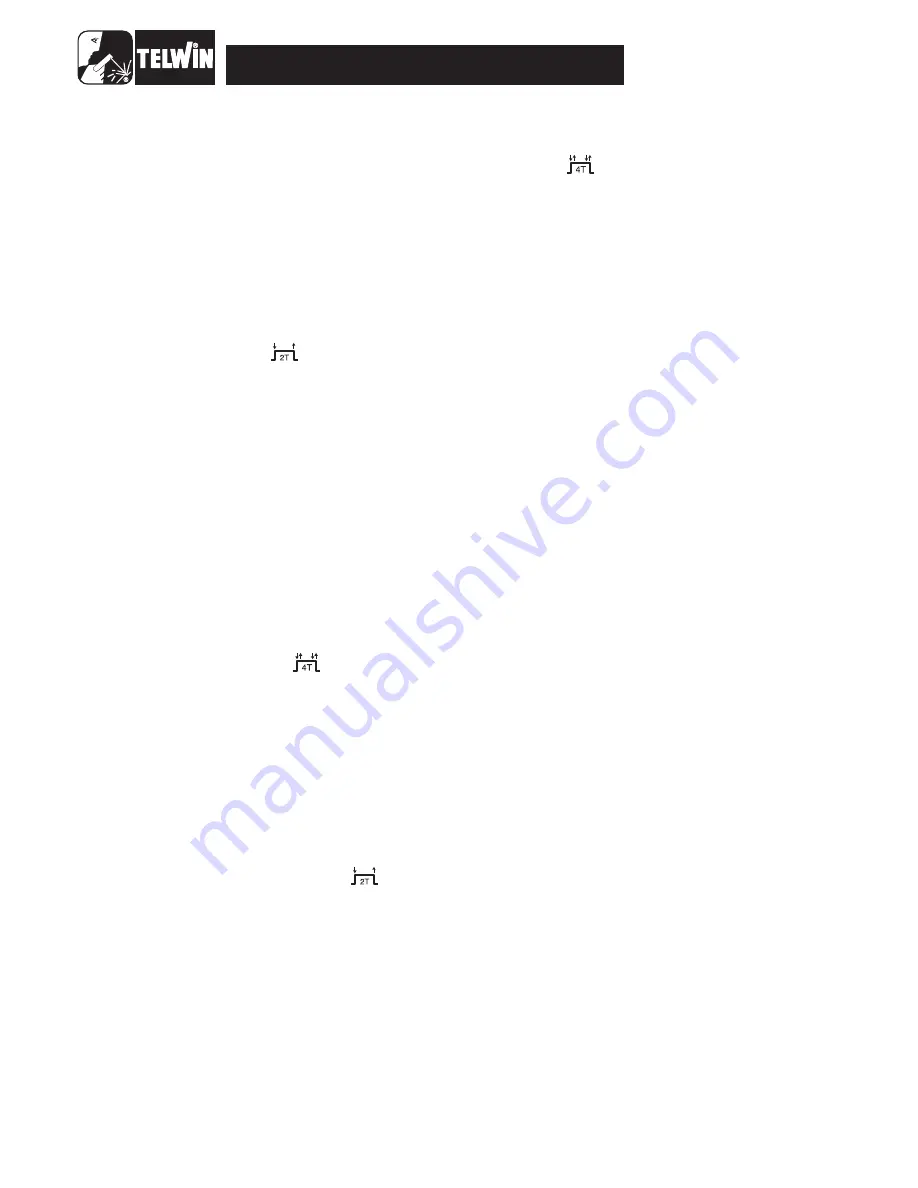
TECHNOLOGY TIG
4
R53) is properly set, the welding arc should strike.
b) Release the torch push-button, check the gradual
decreasing of current and the post-gas potentiometers.
a) Set the switch located on the front panel at 4-phase
position (
).
b) Bring the tugsteno electrode in contact with the element to
be welded, press and release the torch push-button then lift
the electrode for about 2 mm; the welding arc should strike.
In order to obtain a gradual decreasing of current, you must
press and release the torch push-button for the second
time. Finally, check whether there is a post-gas.
Switch the remote control on (code 802109) and ensure that it
works correctly.
Warning! The following remote control adjusts the current in
function of the current set on the front panel; thus, if we set a
value of 50 A on the inverter, we could adjust this value from 5
A to 50 A by acting on the remote control.
Switch the "tig pulse" box on (code 802320) and ensure that
it works correctly by checking the current parameters relative
to peak, pause and work phases.
If striking a welding arc by means of high frequency proves to be
difficult (weak high frequency), the failure could be due to the
following components:
- Torch
- High frequency box
- High frequency transformer
- High frequency filter
- Primary coil with inverted polarity
If after having replaced these components the failure persists, we
suggest to check carefully the high frequency silicone insulated
cable as well as the high frequency transformer connection on the
positive inverter, which must NOT touch the carpentry or the wire
of the torch push-button. Furthermore, we suggest you
disassemble the positive dinse plug and check for signs of
discharges due to high frequency.
There are two types of tig control board and high frequency
transformers:
Tig control board
High frequency transformer
- The two tig control boards are perfectly compatible insofar as the
tig 165 DC-HF is concerned (high frequency striking).The board
with code 112453 instead, cannot be mounted on tigs with lift
striking (tig 161 DC-LIFT).
- The high frequency transformer in Figure 8 is equipped with a
different mechanical fastening system thus, should you need to
make a replacement on a tig mounting a transformer like the one
in Figure 5, you must drill three new holes on the carpentry
3) Checking the 4-phase cycle.
Checking the remote control.
1)
2)
High frequency striking
(See Figure 4-5)
(See Figure 6-7)
(see
Figure 6).
5) Changes and Updates
Jumper set towards connectors J1, J2 (H),
high frequency striking (tig 165 DC-HF).
Jumper set towards pre-gas and lift trimmers (L),
"lift" striking (tig 161 DC-LIFT).
Ensure that the aforementioned jumper is in H position.
Set the machine in electrode through the commutator.
Through static load or directly in welding, ensure the correct
operation of the inverter. (See "Final Testing" in Paragraph 5 of
the Technologic Repairs Manual.)
Set the inverter up for tig welding. (Connect torch and
argon gas bottle.)
Set the switch at two phases (
) down slope and post-
gas potentiometers at the middle of the scale, the pre-
gas trimmer at the minimum (the trimmer is inside the
board).
Press the torch push-button:
The high frequency and the gas electrovalve should excite.
If after two seconds the welding arc does not strike, the
high frequency will automatically disexcite. On the other
hand, if the arc strikes, the current should reach the
value of about 80 A; when releasing the torch push-
button the current decreases gradually for about 2-3
seconds. From this time on, the electrovalve remains
excited for about 3 seconds.
Repeat the same testing procedure, however turning the pre-
gas trimmer clockwise and setting it at the maximum. By
pressing the torch push-button, the electrovalve will excite
but the high frequency will set off after a 4-second delay.
Set this trimmer as to have a 2-second delay or
according to the customer's needs.
Set the commutator at 4 phases (
).
Repeat the preceding testing procedures, keeping in mind
that, in order to strike the arc you must press the torch push-
button. When releasing it, the welding current will remain at
the preset value (80 A). If the operator presses and releases
the torch push-button for a second time, the gradual
decreasing of current and the post-gas phases will begin.
Bring the electrode in contact with the element to be welded; if
you do not press the torch push-button, the yellow led
(D26) located on the front panel should switch on.
Set the welding current of the post-gas and the gradual decreasing
of current potentiometers as you did for the two-phase cycle.
A) Set the switch on front panel at two-phase(
) bring the
tugsteno electrode in contact with the element to be
welded, the led located on the front panel will switch on,
press the torch push-button. Through the plier-shaped
amperometer connected to the mass cable, check whether
there is a flow of current of about 20 A +/- 3 A. Should you
need to reset this value, act on trimmer R53. (In this phase,
the yellow led is switched off.)
a) Bring the tugsten electrode in contact with the element to
be welded, press the torch push-button and lift the
electrode by about 2 mm. If the lift current (20 A trimmer
A)
B)
1)
2)
3)
4)
A) Checking the Tig 165 DC/HF machine cycle
1)
2)
3)
4)
5)
B) Checking the Tig 161 DC-LIFT machine cycle
1) Checking the lift current:
2) Checking lift striking and the 2-phase cycle.