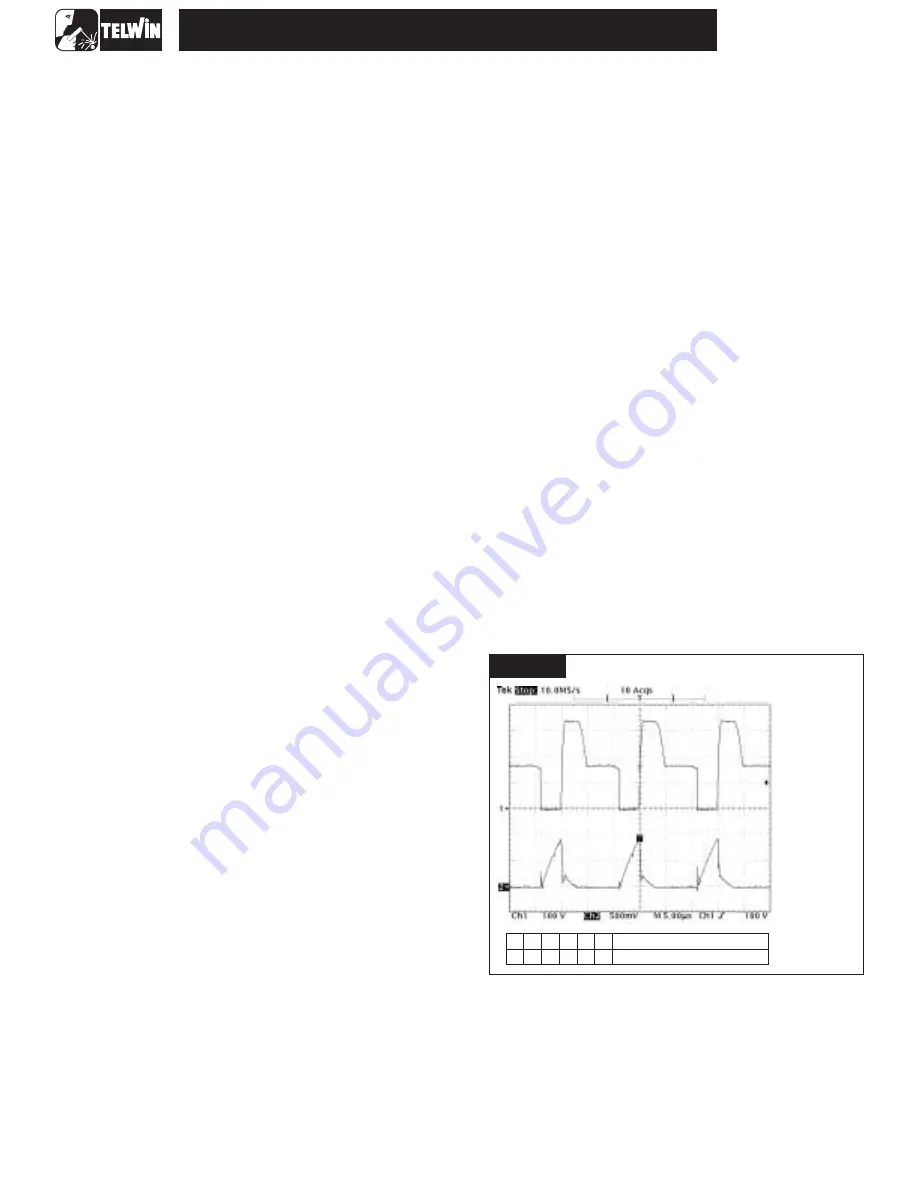
instructions.- Insert the new IGBT's between the
dissipator and the spring, taking care not to damage the
component during assembly (the spring should be
inserted under pressure on the dissipator so as to lock the
component);
-
place the dissipators with the new IGBT's and primary
diodes D40 and D41 (
Make sure there is
insulation between the case of diode D41 and the
dissipator) in the PCB bump contacts, placing 4 spacers
between the dissipator and the PCB (2 for each dissipator)
and fasten them down with the screws (torque wrench
setting for screws 1 Nm ±20%);
-
solder the terminals taking care not to let the solder run
along them;
-
on the welding side cut away the protruding part of the
rheofores and check they are not shorted (between the
gate and emitter in particular).
The 4 SECONDARY DIODES are attached to the same
dissipator, and when a replacement is required, all of them
should be replaced:
-
undo the screws attaching the dissipator to the board, to
replace diodes D20, D21, D22 and D23;
-
remove the 4 secondary diodes unsoldering the rheofores
and cleaning any solder from the bump contacts on the
board;
-
remove the dissipator from the board;
-
remove the spring locking the 4 diodes;
-
clean any irregularity or dirt from the dissipator. If the
diodes have burst the dissipator may have been
irreversibly damaged: in this case it should be replaced;
-
apply thermo-conductive grease following the general
instructions;
-
insert the new diodes between the dissipator and the
spring, taking care not to damage the component during
assembly (the screw should be inserted under pressure
on the dissipator so as to lock the component);
-
place the dissipator with the new components in the PCB
bump contacts and fasten them down with the screws
(torque wrench setting for screws 1 Nm ±20%);
-
solder the terminals taking care not to let the solder run
along them;
-
on the soldering side cut away the protruding part of the
rheofores and check they are not shorted (between
cathode and anode);
make sure resistor (R20) and capacitor (C20) on the
snubber have been soldered to the PCB correctly (
).
Whatever fault occurs in the control board, we strongly
recommend its replacement without attempts at repair. To
remove it, cut and then unsolder from the power board the
connector keeping it fixed perpendicular to the PCB, replace it
and re-solder the connector.
Tests should be carried out on the assembled machine before
closing it with the top cover. During tests with the machine in
operation never commute the selectors or activate the ohmic
load contactor.
Before proceeding to test the machine, we
should remind you that during these tests the power source is
powered and therefore the operator is exposed to the danger
of electric shock.
The tests given below are used to verify power source
operation under load.
.
A) Connect the power source to the static load generator
using cables fitted with the appropriate dinse connectors
(code 802110).
B)
C) Set up the multimeter in DC mode and connect the prods
to the OUT+ and OUT- bump contacts.
D) Connect the power supply cable to the 230Vac power
supply.
During tests the operator must avoid contact with
the metal parts of the torch because of the presence of
dangerous, high voltage.
-
activate the statico load generator and make sure that:
- the waveforms displayed on the oscilloscope resemble
those in
;
- the output current is +5Adc±20%, and the output
voltage is +20.2Vdc±20%.
-
deactivate the static load generator and switch off the
main switch.
-
set up the ohmic load with the switch settings as in the
table in
;
-
on the front panel turn the current potentiometer to 75A
(approx. half-way);
-
start up the ohmic load and make sure that:
- the waveforms displayed on the oscilloscope resemble
those in
;
- the output current is equal to +75Adc ±10% and the
output voltage is equal to +24Vdc ±10%.
-
switch off the ohmic load.
WARNING!
B) Please read the procedure for replacing the
secondary board diodes carefully (fig. 4):
N.B.
fig. 3
C) Please read the procedure for replacing the control
board (fig. 3):
WARNING!
WARNING!
A) Minimum
Fig. D
B) Intermediate load test:
fig. E
Fig. E
1.1 Preparation for testing
1.2 Tests for the TECNICA 150 - 170 - 168GE
Set up the dual trace oscilloscope, connecting probe CH1
(x100) to the collector on Q1 and probe CH2 (x10) to pin 9 on strip
J11 (plasma control board). The earth terminals are connected
together to the emitter of Q1.
load test:
TESTING THE MACHINE
-
set up the static load generator with the switch settings as
in the table in
;
-
on the front panel position the current potentiometer R23
at (approx.) half way.
-
switch on the main switch;
Fig. D
- 14 -
SETTINGS:
PROBE
PROBE
TIME TOLLERANCES
±20%.
:
AMPLITUDE ON CH1
IS
AMPLITUDE ON CH2
IS
-
CH1 x100
- 100V/Div;
-
CH2 x10;
- 500mV/Div;
- 5 sec/Div.
-
320V ±10%.
-
1V ±10%.
VERIFY THAT
µ
FIGURE D
Position number
Switch number
1
1
2
0
3
0
4
0
5
0
6
0
TECNICA 150-152-170-168GE