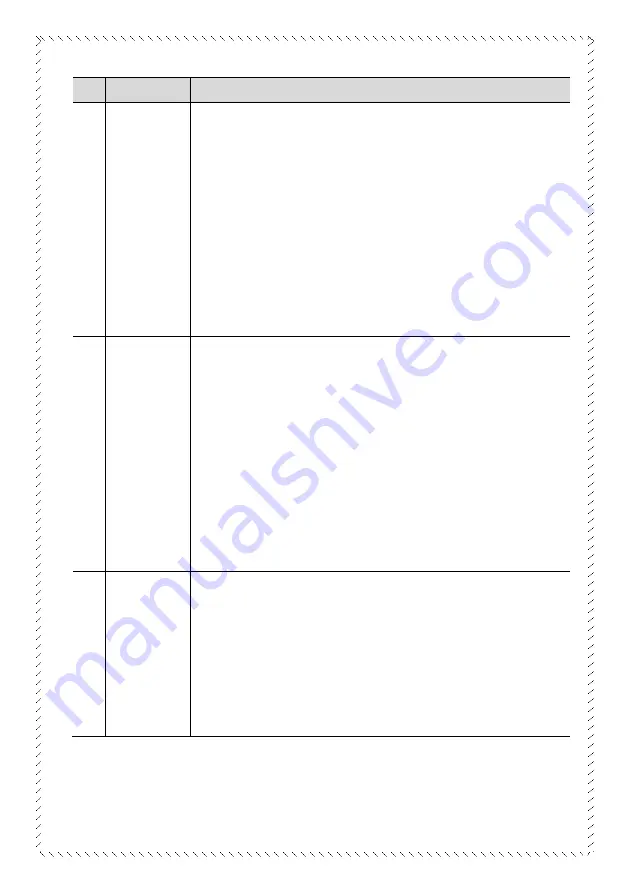
- 32 -
3. Common Welding Imperfections and Analysis
No.
Trouble
Causes
1
Blowhole
1.
Impure gas or insufficient gas supply.
2.
Absorption of air during welding.
3.
Failed preheater.
4.
Poor gas shielding owing to strong wind.
5.
Torch nozzle blocked by spatter.
6.
Too great a distance between nozzle and workpiece.
7.
Polluted welding surface with oil and dust or moisture
caused from insufficient cleaning not sufficiently removed.
8.
Arc length too long and voltage too high.
9.
Insufficient silicon and manganese content in welding wire.
2
Undercut
1.
Impure gas or insufficient gas supply.
2.
Absorption of air during welding.
3.
Failed preheater.
4.
Poor gas shielding owing to strong wind.
5.
Torch nozzle blocked by spatter.
6.
Too great a distance between nozzle and workpiece.
7.
Polluted welding surface with oil and dust or moisture
caused from insufficient cleaning not sufficiently removed.
8.
Arc length too long and voltage too high.
9.
Insufficient silicon and manganese content in welding wire.
3
Incomplete
penetration
1.
Low welding current and uneven wire-feed speed.
2.
Arc voltage too low or too high.
3.
Inside the beveled edge the welding speed is too slow or
too fast.
4.
Beveled gap too small.
5.
Welding wire out of position and not aligned with the centre
of the welding bead.