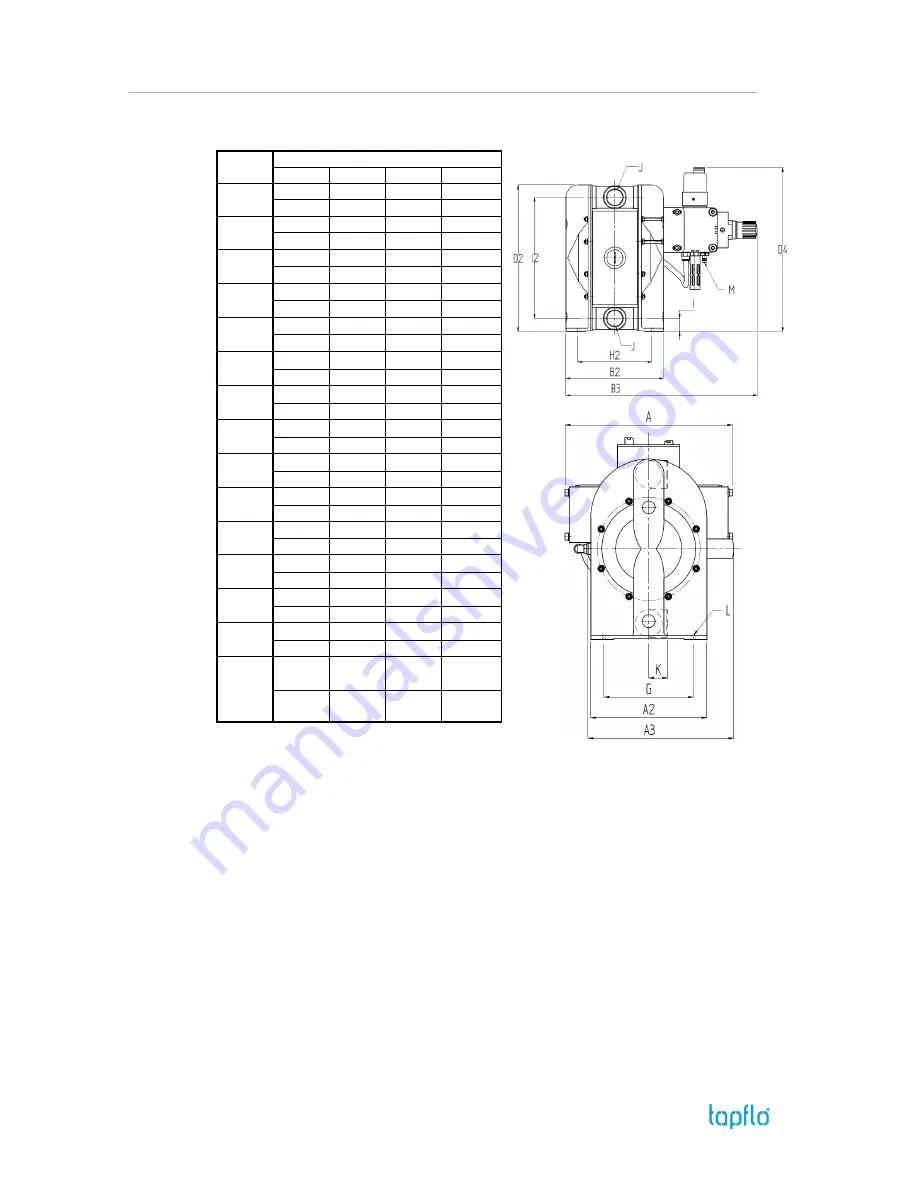
6. DATA
IOM manual Tapflo TF series
38
6.4.2.
Stainless steel pumps
DIM
PUMP SIZE
70
120
220
420
A
172
319
398
398
6.77
12.56
15.67
15.67
A2
150
200
272
352
5.91
7.87
10.71
13.86
A3
160
239
342
389
6.30
9.41
13.46
15.31
B2
156
205
282
347
6.14
8.07
11.10
13.66
B3
253
407
560
624
9.96
16.02
22.05
24.57
D2
229
309
422
529
9.02
12.17
16.61
20.83
D4
165
332
464
551
6.50
13.07
18.27
21.69
G
116
160
210
280
4.57
6.30
8.27
11.02
H2
129
158
214
284
5.08
6.22
8.43
11.18
I
19
27
38
44
0.75
1.06
1.50
1.73
I2
192
257
348
443
7.56
10.12
13.70
17.44
J
1/2"
1"
1 1/2"
2"
1/2
1
1 1/2
2
K
40
52
70
80
1.57
2.05
2.76
3.15
L
8.5
8.5
8.5
10
0.33
0.33
0.33
0.39
M
G1/8" /
DN10
G1/4" /
DN10
G1/2" /
DN10
G1/2" /
DN10
G1/8 /
DN10
G1/4 /
DN10
G1/2 /
DN10
G1/2 /
DN10