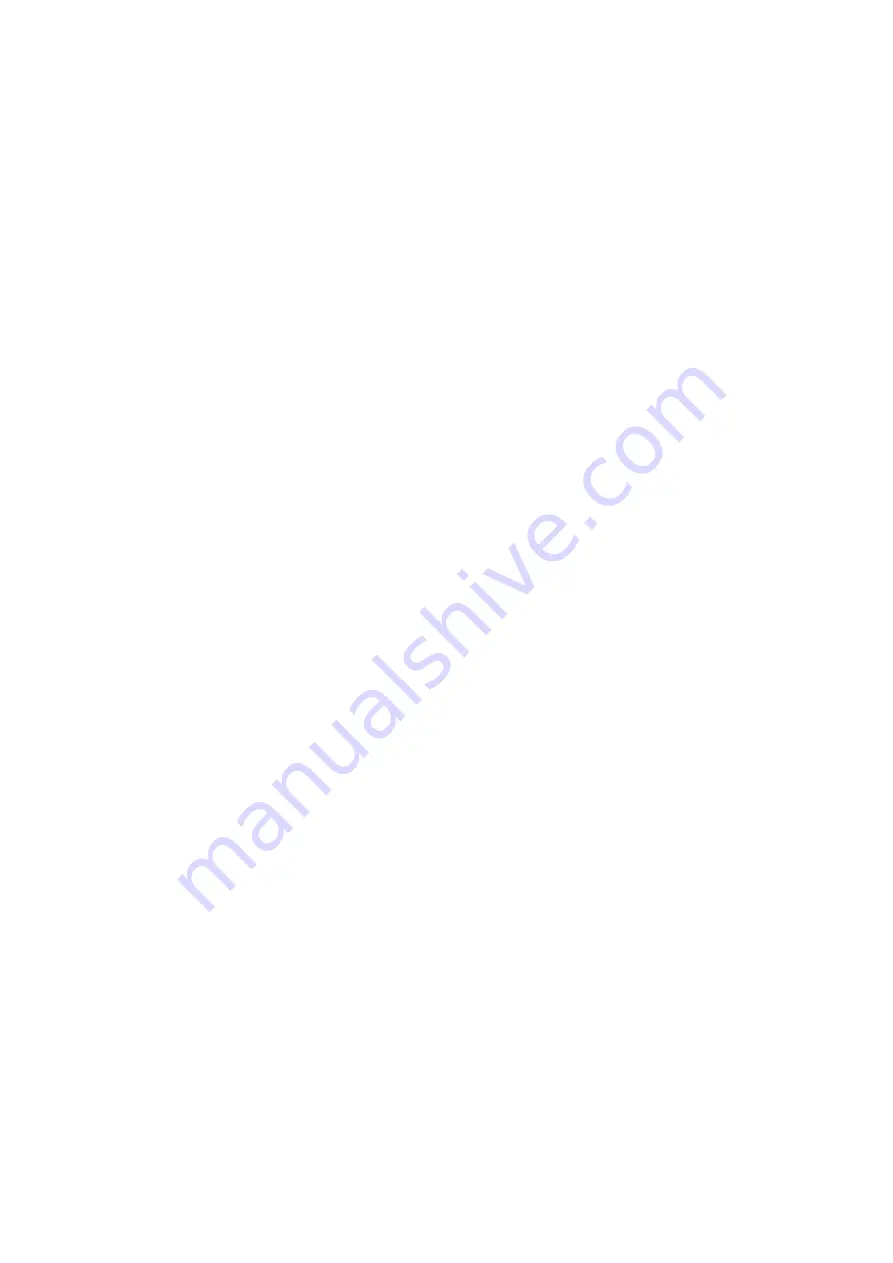
6
3. DETERMINE THE DIMENSIONS
OF THE SENSOR
The dimensions of the sensors and their
layout must be such that, access to the machine
is not possible without stepping on the sensor.
The dimensions of the dangerous area depend
on the particular application. The parameters
to be considered include:
- Speed of walk or arm movement
(typically 1.6m/s).
- Arm length (typically 0.85m).
- Length of stride (typically 0.7m).
- Response time of system.
- Position of dead zones.
- Overtravel of dangerous parts after
stop signal is generated
To determine the size of sensor needed, use
this simple formula below:
60mm = Overall Sensor
Area
length or width
i.e. For a sensor measuring 2000mm x 1000mm
the size of active area = 1940mm x 940mm.
Note that if the sensor is to be supplied and
fitted with AE-13 Aluminium edging then:
Total Area = Overall Sensor + 126mm
Covered with length or width
AE-13 Edging
i.e. For a sensor measuring 2000mm x 1000mm
the total area covered = 2126mm x 1126mm.
In order to determine the position of the front
edge of the active zone it is necessary to
consider the stopping performance of the
machine.
Any machine regardless of the efficiency of its
braking system, will take a certain amount of
time to come to rest after a stop signal is
generated. From the instant that a persons
foot touches the sensor to the instant that the
dangerous motion actually ceases is called the
overall system response time.
The overall system response time, T, is given
by the following calculation:
T = t1 + t2
where t1 = the maximum response time of
the safety device between the
actuation of the sensor and the
generation of the stop signal.
and t2 = the response time of the machine
between receiving a stop signal
from the safety device and the
dangerous parts coming to rest.
The dangerous parts will obviously continue
to move during this time. The sensor must
therefore be dimensioned such that the nearest
point at which a person could first touch the
mat is a certain minimum distance from the
dangerous parts, to prevent the person from
reaching the dangerous parts before they have
stopped.
This must take into account the worst case
conditions illustrated in Figure 4 where a
person could be a full stride onto the sensor
before the sensor is actuated. This means that
a certain distance from the front edge of the
sensor and the dangerous parts must be
maintained.