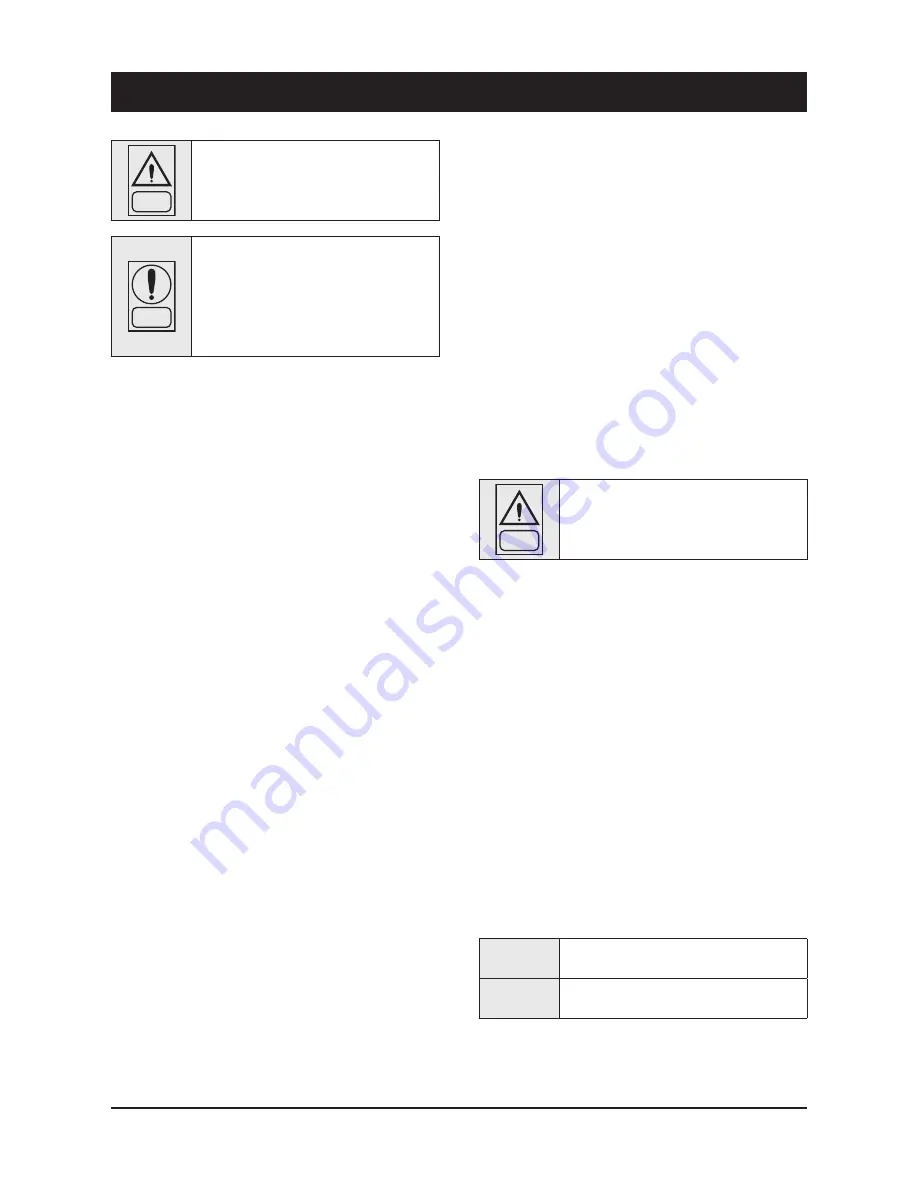
20
5 - Start-up
WARNING
The unit must be started for the first time by
personnel suitably trained by one of Authorised
Service Centre. Failure to meet this requirement
will immediately void the warranty.
NOTE
The operations carried out by authorised
personnel are limited to the start-up of the
unit, and do not include any other operation
on the plant, such as, for example, electrical
and hydraulic connections etc. All the other
operations before start-up, including oil pre-
heating for at least 12 hours, must be performed
by the Installer.
5.1 Preliminary check
The checks listed below shall be performed before starting the unit
and before the arrival of the personnel authorised.
!
Check the section of power supply and grounding cables; make
sure that terminals are tightened and check the correct operation
of contactors, with the main switch open.
!
Check that any voltage and phase variation in the power supply
does not exceed the prefixed thresholds.
!
Connect the contacts of the flow switch and of an external
interlock, to terminals 1-2 and 3-4 (Y1 user terminal), respectively.
!
Check that the components of the external water circuit (pump,
user equipment, filters, power supply tank and reservoir, if any)
have been installed properly, and according to the manufacturer’s
instructions.
!
Check the filling of the hydraulic circuits, and make sure that
the fluid circulation is correct, without any trace of leaks and air
bubbles. If you use ethylene glycol as antifreeze, check that its
percentage is correct (do not exceed 35% glycol percentage).
!
Check that the direction of rotation of the pumps is correct, and
that fluids have been circulating for at least 12 hours for both
pumps. Then, clean the filters on the suction side of the pumps.
!
Adjust the liquid distribution network in such a way that the flow
rate is within the specified range.
!
Check that the water quality is up to the specifications.
!
Check that oil heaters, if any, have been turned on at least 12 hours
before.
5.2 Start-up
Start-up sequence:
!
Turn on the Main switch (at least 12 hours before).
!
Check that the oil in the compressor has reached the requested
temperature (the minimum temperature outside the pan must be
approx. 40°C) and that the auxiliary control circuit is energised.
!
Check the operation of all the external equipment, and make sure
that the control devices of the plant are properly calibrated.
!
Start the pump and check that the water flow is correct.
!
Set the desired fluid temperature on the control board.
!
Start the appliance (see Chapter 6).
!
Check the correct direction of rotation of compressors. Scroll
compressors cannot compress the refrigerant when they rotate in
the opposite direction. To make sure that they are rotating in the
correct direction, simply check that, just after the start-up of the
compressor, the pressure drops on the LP side and rises on the
HP side. Furthermore, if a scroll compressor rotate in the opposite
direction, there is a considerable rise in the sound level of the unit,
as well as in a dramatic reduction of current absorption compared
to normal values. In case of wrong rotation, the scroll compressor
can be definitely damaged. Phase monitor is assembled in the
unit as a standard to prevent wrong compressors rotation.
!
After about 15 minutes of operation check that there are no
bubbles, through the sight glass on the liquid line.
WARNING
The presence of bubbles may indicate that a
part of the refrigerant charge has been released
in one or more points. It is important to remove
these leaks before proceeding.
!
Repeat the start-up procedure after removing the leaks.
5.3 Checking the operation
Check the following:
!
The temperature of the water entering the evaporator.
!
The temperature of the water leaving the evaporator.
!
The level of the water flow rate in the evaporator, if possible.
!
The current absorption upon the start of the compressor and in
case of stabilised operation.
!
The fan’s current absorption.
Check that the condensing and evaporation temperatures, during
operation at high and low pressure detected by the pressure gauges
of the refrigerant, are within the following range :
(On the units not provided with HP/LP pressure gauges for the
refrigerant, connect a pressure gauge to the Shrader valves on the
refrigeration circuit).
HP side
Approx. 15 to 20 °C above the temperature of the
air entering the condenser, for R410A units.
LP side
Approx. 2 to 4 °C below the temperature of the
leaving chilled water, for R410A units.
5.4 Delivery to the customer
!
Train the user according to the instructions provided in Section 6.
Содержание SYSCROLL 20-35 Air
Страница 2: ......
Страница 21: ...19 English SYSCROLL Air CO HP Version Electrical Connections 4 Installation ...
Страница 39: ...37 English 8 7 Space Requirements SYSCROLL 20 35 Air CO HP 8 Technical Data 400 mm 200 mm 800 mm 200 mm 200 mm ...
Страница 46: ...44 Notes ...
Страница 47: ...45 English Notes ...
Страница 48: ...46 Notes ...