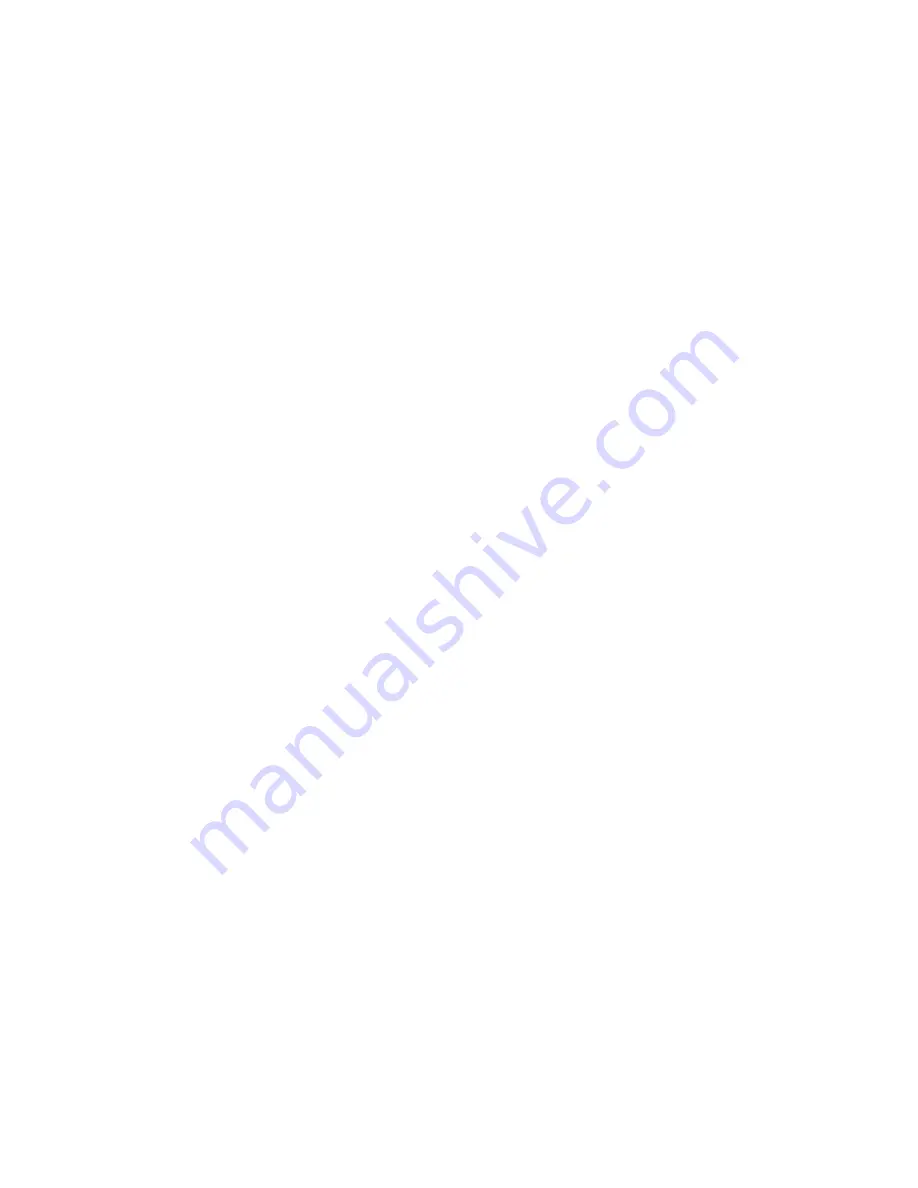
operation
34
SYNRAD OEM v30 Operator’s Manual Version 2
Initial start-up
Without a UC-2000 Controller
When not using a UC-2000 to control the laser, follow the steps below to verify laser operation. For all
v30 lasers, an externally-generated tickle signal is required for optimum laser performance. Connect the
signal generator for both tickle and PWM Command signals to either the Interface A (DB-9) or Interface B
(RJ45) connector. Refer to Interface connections in the Technical Reference chapter for connector pinouts
and see Controlling laser power in the Technical Reference chapter for tickle and PWM signal descriptions.
Note: After applying 30 VDC, but before operating the laser, you must provide a Laser Enable input
signal to either the Interface A (DB-9) or Interface B (RJ45) connector. See Interface connections in
the Technical Reference chapter for pinouts and signal descriptions.
Starting auxiliary equipment
1
Ensure that all personnel in the area are wearing protective eyewear.
2
Remove the red self-adhesive aperture seal from the laser faceplate.
3 Place a power meter, or appropriate beam block, 61 cm (24 in) from the laser aperture to prevent the
beam from traveling beyond the work area.
4
Connect the output of your PWM controller to PWM Positive (Pin 1) on the appropriate interface
connector and connect the ground or return of the Controller to PWM Negative (Pin 6).
Note: Your controller must provide both tickle and PWM Command signals to the laser. See Controlling
laser power in the Technical Reference chapter for tickle and Command signal descriptions.
5
Ensure your controller is set to provide a 1 µs square wave tickle pulse (at a frequency of 5 kHz) after
any 200-µs measurement period where a PWM signal is not applied.
6
Set your PWM controller to a frequency of 5 kHz and ensure that the controller’s duty cycle is set to
zero percent output (0.0%).
Starting your OEM v30 laser
1
If the laser has a Diode Pointer installed, remove its aperture dust cover.
2
Turn on the +30 VDC power supply. The v30’s PWR LED should illuminate green.
3
Apply a Laser Enable signal to the appropriate interface connector. The yellow RDY lamp turns on
to indicate that lasing is enabled when a PWM Command signal is received.
Note: On cold starts, provide five to ten seconds of tickle before sending PWM Commands to the laser.
4
Using your PWM controller, apply tickle pulses (a +5 VDC, 5 kHz square wave of 1 µs duration).
After five to ten seconds, slowly increase the duty cycle of the square wave. The LASE indicator il-
luminates red when PWM pulses are long enough to produce laser output. The spot where the beam
hits the beam block should increase in brightness to indicate increased power output.
5
Remove the PWM Command signal from the laser and re-apply tickle pulses every 200 µs. The
LASE indicator on the laser should turn off.
If your OEM v30 laser fails to lase, refer to Troubleshooting in the Maintenance/Troubleshooting chapter for
troubleshooting information.