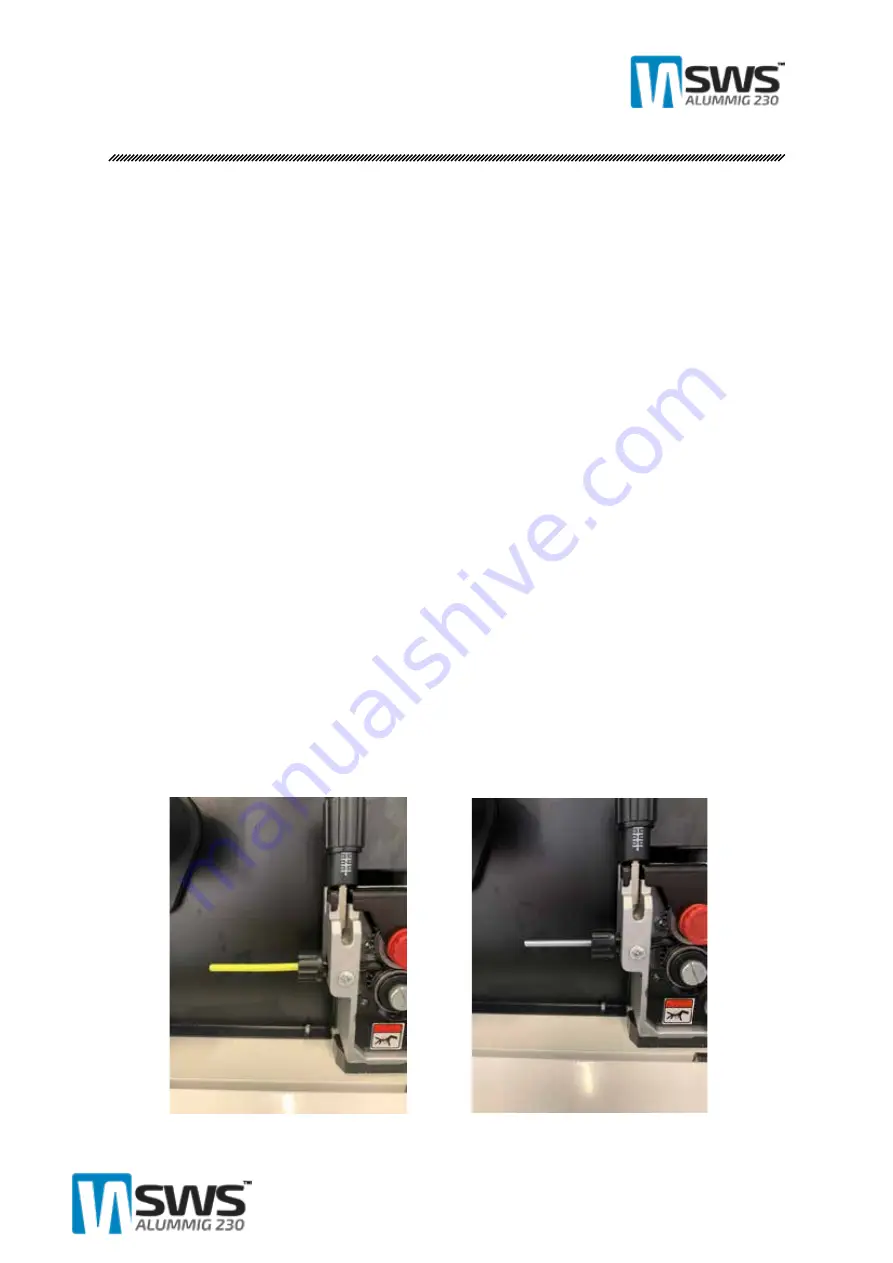
Manual Version 1.0
21
The matching of welding wire and feed roller
Using the wire according to the specification on both sides of the feeding roller, pay
attention to the corresponding relationship of the marking and slot
Feed roller use and replacement
To prevent slippage, the protective grease should be cleaned from the feed roller.
Due to the different diameter of the welding wire, the feed roller should be exchanged
frequently. When disassembling the feed roller, at first turn off the power of the welding
machine, open the pressure adjustment handle, take out the welding wire, unscrew the
fastening nut (screw), remove the feed roller and change to the roller needed. Note that
the flat key cannot fall off, tighten the nut (screw). Then install the welding wire in the
steps of replacing the welding wire.
Daily considerations
- Due to vibration, the tightening nut may loosen during use, check regularly, tighten it if
it is loose.
- Do not touch the feed roller and gear with your hand when it is working.
Use in areas, not exposed to direct sunlight, rain or wind, avoid the welding slag falling
into the wire feeder.
-Frequently clean the dirt and dust in the groove of the feed roller
- There should be no abnormal heating at the cable connection
- All cable joints should be well insulated
Wire feeding guides
(To change unfasten the Phillips head locking screw)
FIGURE 1 - Used for soft wires such as aluminium.
FIGURE 2 - Hard wires such as steel and stainless steel.
WIRE FEEDER
FIGURE 1
FIGURE 2