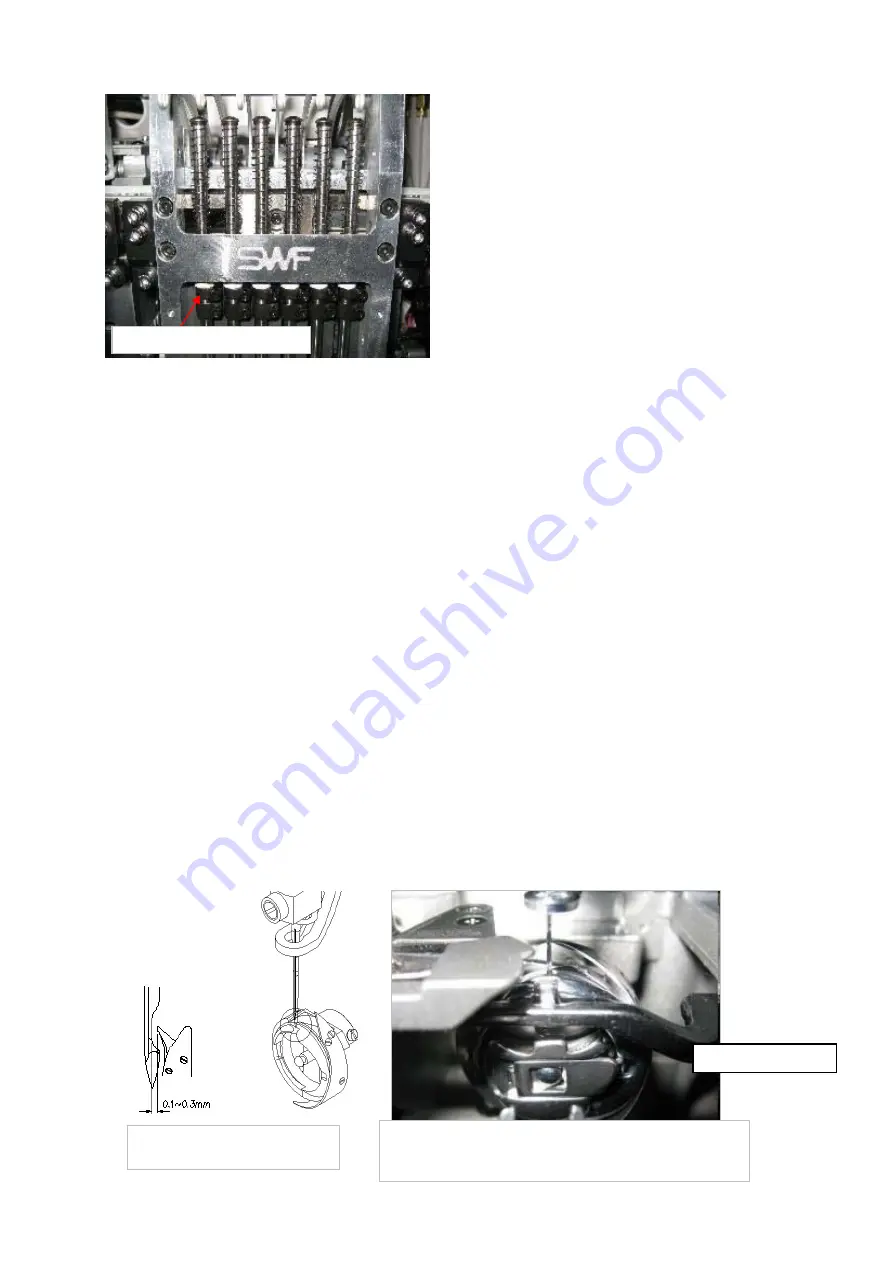
running the machine.)
8
Check and adjust rotary timing.
Check if the needle is bent first before setting the rotary hook. Set the needle to right direction.
(Requirement for optimal loop formation)
(1) Check and adjust rotary hook timing and rotary hook gap. (Use "-" driver)
1) Fix the angle of main shaft at 201degrees. Check the position of the point of rotary hook
and looseness.
- If the point of rotary hook is not in a correct position or the rotary hook distance from needle
is big or none, reset.
- Place the point of rotary hook to the back of needle, and space it with 0.1~0.3mm intervals.
2) Rotary Hook Timing Setting
- Of the three fixing screws of rotary hook (point at 135 degrees and at 75 degrees),
unlock two screws from the center needle bar.
- Fix the angle of main shaft at 201degrees. Check the position of the point of rotary hook
and looseness.
- After setting the rotary hook, check the rotary hook looseness from First and Last Needle.
Lock all rotary hook Screws.
Upper Dead Point Stopper
Rotary Hook Support
Needle
Point of Rotary Hook
Set Gap (0.1~0.3mm)
Projection Part in Rotary Hook Support should be in
the center of Needle.
- Set Gap (0.5~0.7mm) from Hook.
SUNSTAR Co.Ltd
Page 8 Of 11
SWF CS Center