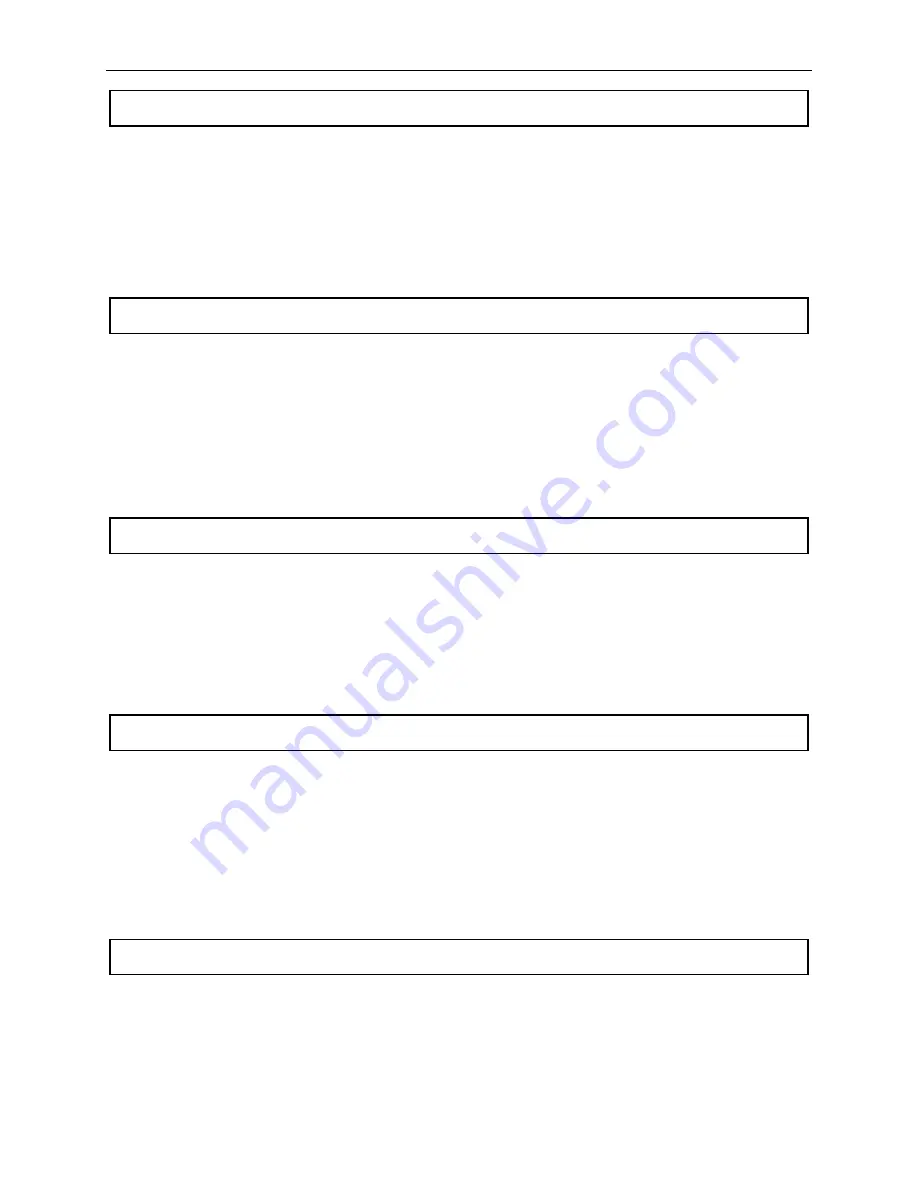
Instruction and Operation Manual
SA-07-11-37 Rev Orig
9
Jan 2009
NPSH - (Net Positive Suction Head and Cavitation)
In order to protect the pump, it is recommended
that NPSH available be at least two-feet greater
than NPSH required. If the pump is operated
beyond the design capacity the increase in
required NPSH with the increase in capacity will
eventually result in cavitation. This is usually
identifiable as a loud rumble, sometimes
described as sounding like gravel is being
pumped. Continuous operation in a state of
cavitation may cause serious damage to the
impeller. Vibration can result in more extensive
damage to the pump.
Recirculation
Centrifugal pumps can experience vibrations
from internal flow separations and recirculation
at low flow conditions. The operator must be
aware of the minimum flow recommendations of
the manufacturer. It is possible for a pump to
operate with some cavitation noise due to
recirculation without harm to the pump.
However, excessive noise and vibration are
signs that the pump may be subject to damage if
operation is continuous. Noise and vibration may
be accentuated by resonance in the discharge
line. This is especially true when a control valve
is located well downstream from the pump.
Prevention
It is essential that the pump be selected to mate
properly with the system head curve to prevent
the pump from operating on its curve where
damage may be sustained from recirculation or
cavitation. It is also essential that once it is
selected that it is properly controlled. Use of flow
control should be used in place of pressure
control if variable flows are to be experienced.
Pressure control is a very difficult and exacting
practice due to the relatively flat head capacity
curve of Sundyne pumps. Flow control, on the
other hand, can be quite precise and effective
.
Temperature Rise
Temperature rise within the pump is unlikely to
become of problem as long as the pump is not
operated below minimum flow
recommendations. If operation at low flows does
become mandatory or if the system causes the
pump discharge line to be blocked for any period
of time, a means of maintaining minimum flow
must be provided. Using either a continuous
bypass or a flow-controlled bypass can
accomplish this. The operator can calculate the
amount of bypass necessary to prevent boiling
liquid in the pump case and at the seal faces.
Please refer to the manufacturer for information
if this becomes necessary.
Suction and Discharge Gauges
It is recommended that suction and discharge
pressure gages be installed on any pump that is
not flow controlled. If no flow-measuring device
is installed there is not a way to determine
accurately where on its curve the pump is
operating.