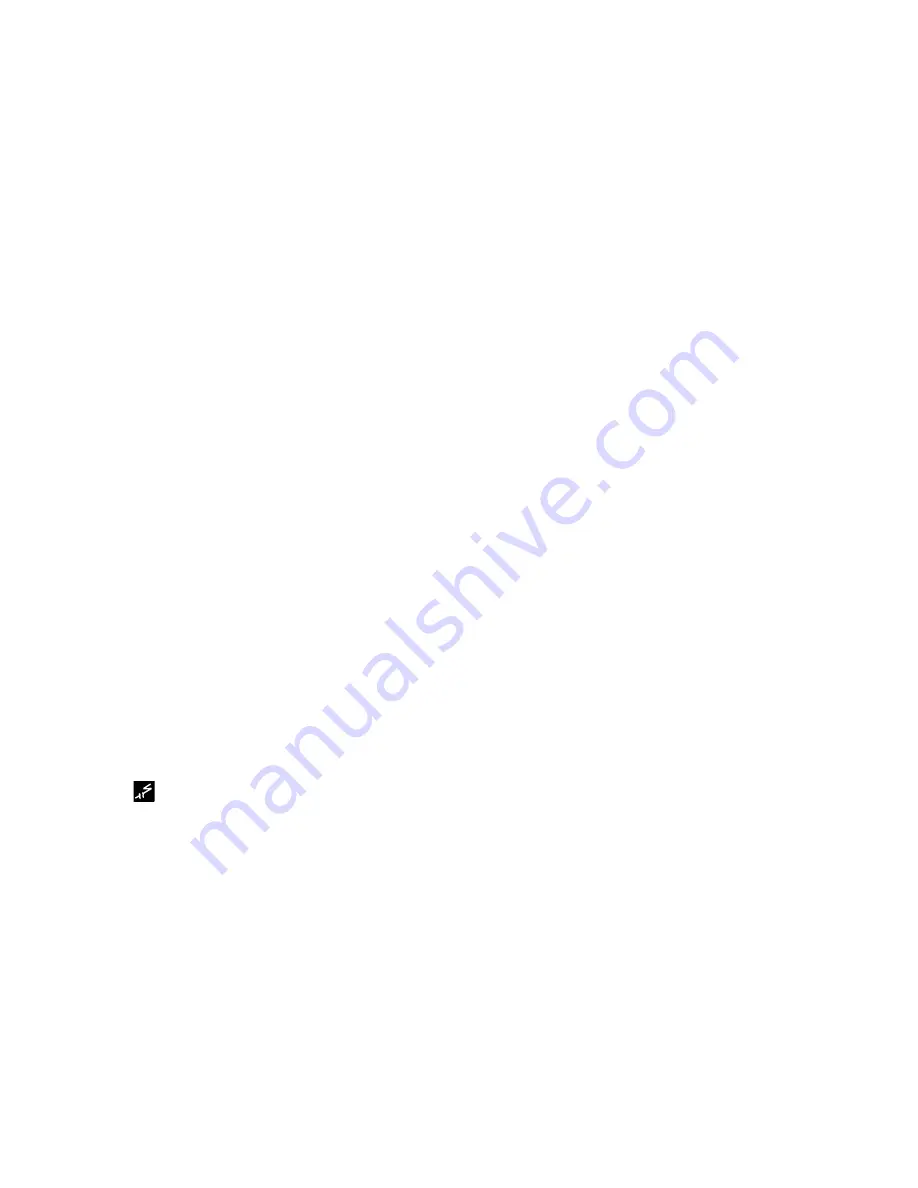
4
Section 2
SEQUENCING WITH MULTIPLE SUPERVISOR CONTROLS
delta pressure) may need to be calibrated to take into account the extra pressure drop of
the down stream equipment.
2.3 CONTROLS WIRING
Control signals are passed along a simple network cable, Belden 9842 or similar. This cable
has two twisted pairs with a shield. One twisted pair is connected to ISO + and ISO - on the
Supervisor Comm module. Twisted pairs usually have one colored wire twisted with a black
or white wire. Make sure that the colored wire is on ISO + and the white or black wire is on
ISO -. Both wires of the other twisted pair are connected to ISO GND. The shield should be
connected to ground at one end only.
For Supervisor II Deluxe controllers, connect the colored wire to J2-16 and the white or
black wire to J2-17. Connect both wires of the other twisted pair is connected to J2-18.
2.4 MACHINE PREPARATION PRIOR TO SEQUENCING
1. Complete all machine startup procedures for stand-alone operation for the machines that
are to be sequenced together per the compressor operator’s manual.
2. Relocate the P2 signal for all machines to read the common header pressure. To recali-
brate the P2 signal for each machine so that they match within 1 psi of each other, use
the system display mode described later to view P2 on all machines. Recalibrate P2 on
each machine to match P2 on the other machines.
3. Program each machine with a different COM ID number (i.e.1, 2, 3, etc.).
4. Set UNLOAD psi, LOAD psi, BAUD RATE (Supervisor is fixed at 9600), SEQUENCE
mode (COM ID or HOURS), LAST COM, LOWEST and RECOVER time (normally set at
10) the same for each machine (except for VSD applications). Leave ROTATE hours dis-
abled except for the specific application described elsewhere. Set all SEQ HRS the same
unless it is desired to force certain machines to initially run more than others in the
HOURS mode.
5. Set the machines to run in AUTO mode. On the Supervisor, also press the Remote key
to arm the machines for sequencing. Machines will start immediately if the P2 system
pressure is low. On a fully pressurized system the machines will go into SEQ STOP until
a demand is seen. The following operation describes how machines are started, fully
loaded and unloaded by the sequencing mode selected. The AUTO mode provides the
means for each machine to SEQ STOP by timing out on its unload timer (UNLD TIM)
when the sequencing order decides the machine is to be unloaded.
2.5 SYSTEM OPERATION
For this example three machines are in a system with the load pressure set at 100, unload
at 110 psig (7.6 bar), lowest pressure at 90 psig (6.2 bar), and Recovery Time at 10 sec-
onds (default value). All machines are in sequence stop (top line of the display is SEQ
STOP). When the pressure drops below 102 psig (7.6 bar) a timer starts counting down from
Содержание Supervisor 2 Deluxe
Страница 6: ......
Страница 26: ...20 NOTES...