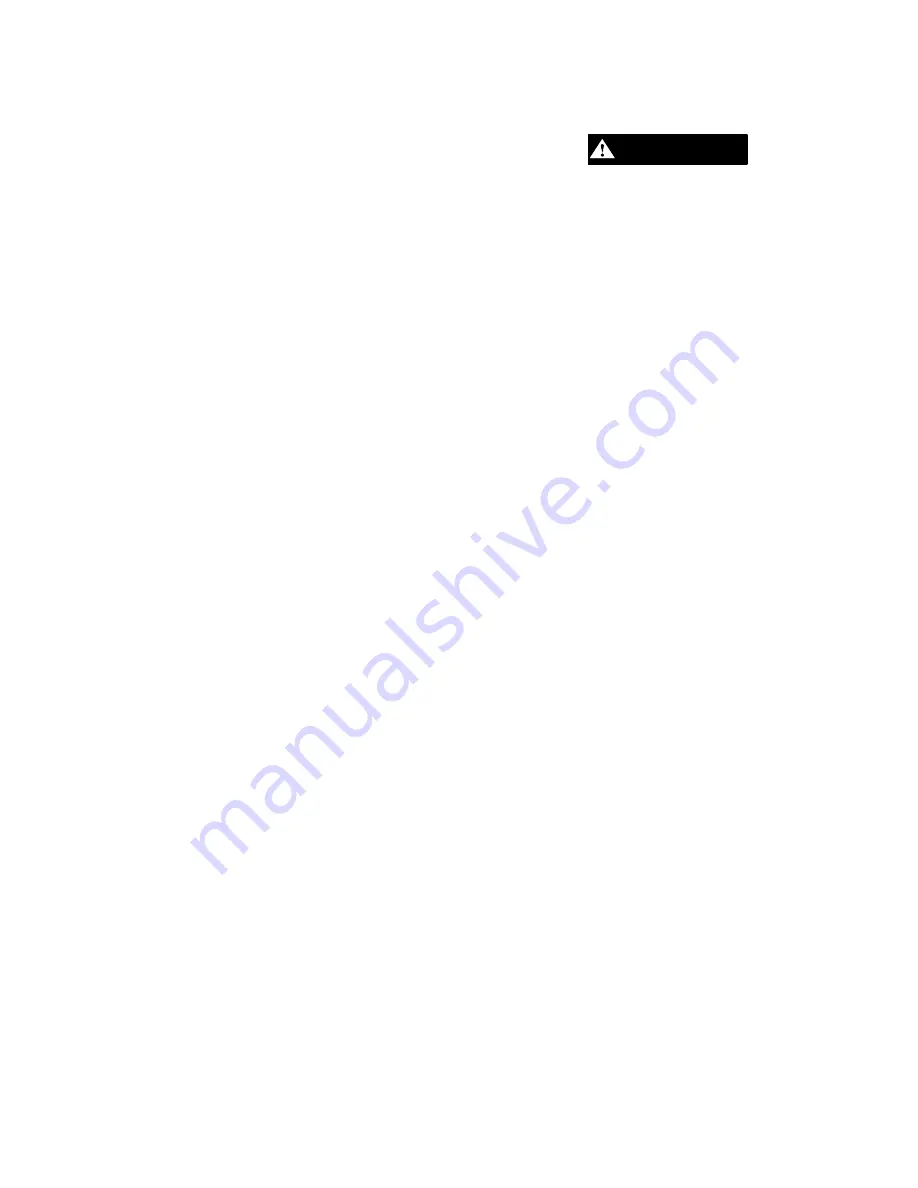
Section 1
DESCRIPTION
4
shut down.
The receiver has three main functions:
•
Acts as the primary coolant separator
•
Serves as the compressor coolant sump
•
Houses the final coolant separator element.
The compressed air / coolant mixture enters the re-
ceiver and is directed against the far end of the
tank. Its direction of movement is changed and its
velocity significantly reduced causing the larger
droplets of coolant to fall to the bottom of the receiv-
er/sump. The fractional percentage of coolant re-
maining in the compressed air collects on the sur-
face of the primary separator element as the com-
pressed air flows through the separator. A secon-
dary separator element is provided to stop any
coolant from reaching the service air. A return line
(or scavenge tube) leads from the bottom of each
separator element to the inlet region of the com-
pressor unit. Coolant collecting on the bottom of
the separator elements is returned to the compres-
sor by the pressure differential between the receiv-
er and the compressor inlet. A visual sight glass is
located in the both return lines to observe this cool-
ant flow. There is also an orifice in each return line
(protected by a strainer) to assure proper flow. An
indicator, (located adjacent to the instrument pan-
el), shows red if abnormal pressure drop through
the primary separator develops. At this time, sepa-
rator element replacement is necessary.
The receiver is ASME Code rated at 150 PSIG work-
ing pressure. A minimum pressure valve, located
downstream
from the separator, assures a minimum receiver
pressure of 40 PSIG during all conditions. This
pressure is necessary for proper fluid/air separa-
tion and to assure proper fluid circulation.
A terminal check valve at the outlet of the receiver
prevents compressed air in the service line from
bleeding back into the receiver on shutdown and
during operation of the compressor in an unloaded
condition.
A pressure relief valve (located on the wet side of
the separator) is set to open if the sump pressure
exceeds 140 PSIG. A fast-acting thermistor-type
temperature switch will shut down the compressor
if the discharge temperature reaches 240
°
F.
All compressor models are equipped with a high
pressure shutdown switch to shut down the com-
pressor at 135 PSIG. This prevents the pressure re-
lief valve from opening under routine conditions,
thereby preventing coolant fluid loss through the
pressure relief valve.
WARNING
DO NOT remove caps, plugs, or oth-
er components when compressor is
running or pressurized.
Stop compressor and relieve all internal pressure
before doing so.
24KT fluid is added to the sump via a capped cool-
ant filler opening, placed low on the tank to prevent
overfilling the sump. A sight-glass enables the op-
erator to visually monitor the sump fluid level.
1.6
CONTROL
SYSTEM,
FUNCTIONAL
DE-
SCRIPTION
Refer to Figure
. The purpose of the compressor
control system is to regulate the compressor air in-
take to match the amount of compressed air being
used. At a 0 to 10 percent air output, the control
system will automatically blow down the machine
and greatly reduce the unload power consump-
tion. The Sullimatic Control system consists of a
Sullicon control, a butterfly valve (located on the
compressor air inlet), a pressure regulator, pres-
sure switch, pilot valve and blowdown valve. The
functional description of the control system is de-
scribed below in four distinct phases of compres-
sor operation. The following descriptive text ap-
plies to all Series 32 24KT machines. For explana-
tion purposes this description will apply to a ma-
chine with an operating pressure range of 100-110
PSI. A machine with any other pressure range
would operate in the same manner excepting
stated pressures.
START MODE -0 TO 40 PSI
When the compressor START button is depressed,
the pressure will quickly rise from 0 to 40 PSI. Dur-
ing this period both the pressure regulator and the
pilot valve are closed and the Sullicon Control is in-
operative. The spring on the control holds the but-
terfly valve fully open and the compressor pumps at
full rated capacity. The rising compressor air pres-
sure is isolated from the service line in this phase by
the minimum pressure valve, set at approximately
40 PSI.
NORMAL OPERATING MODE -40 TO 100 PSI
When the compressed air pressure rises above 40
PSI, the minimum pressure valve opens and deliv-
ers
compressed air to the service line. From this point
on, the line air pressure is continually monitored by
a line pressure gauge. The pressure regulator and
the pilot valve remain closed during this phase,
keeping the Sullicon control inactive.
MODULATING MODE -100 TO 110 PSI
If less than the rated capacity of compressed air is
Содержание 300H Series
Страница 1: ...P N 252433 Operators Manual and Parts List Series 32 250L and 300H Rotary Screw Air Compressor...
Страница 6: ...NOTES...
Страница 11: ...Section 1 DESCRIPTION 5 Figure 1 4 Control System Sequence of Operation...
Страница 14: ...8 NOTES...
Страница 16: ...10 NOTES...
Страница 32: ...Section 6 ILLUSTRATIONS AND PARTS LIST 26 6 3 MOTOR COMPRESSOR FRAME AND PARTS...
Страница 34: ...Section 6 ILLUSTRATIONS AND PARTS LIST 28 6 4 COMPRESSOR AIR INLET SYSTEM...
Страница 36: ...Section 6 ILLUSTRATIONS AND PARTS LIST 30 6 5 COMPRESSOR COOLING AND LUBRICATION SYSTEM WATER COOLED...
Страница 38: ...Section 6 ILLUSTRATIONS AND PARTS LIST 32 6 6 COMPRESSOR UNIT TUBING...
Страница 40: ...Section 6 ILLUSTRATIONS AND PARTS LIST 34 6 6 COMPRESSOR UNIT TUBING...
Страница 42: ...Section 6 ILLUSTRATIONS AND PARTS LIST 36 6 7 UPDRAFT ASSEMBLY...
Страница 44: ...Section 6 ILLUSTRATIONS AND PARTS LIST 38 6 8 COMPRESSOR COOLING AND LUBRICATION SYSTEM AIR COOLED...
Страница 46: ...Section 6 ILLUSTRATIONS AND PARTS LIST 40 6 8 COMPRESSOR COOLING AND LUBRICATION SYSTEM AIR COOLED...
Страница 48: ...Section 6 ILLUSTRATIONS AND PARTS LIST 42 6 9 COMPRESSOR DISCHARGE SYSTEM...
Страница 50: ...Section 6 ILLUSTRATIONS AND PARTS LIST 44 6 9 COMPRESSOR DISCHARGE SYSTEM...
Страница 52: ...Section 6 ILLUSTRATIONS AND PARTS LIST 46 6 9 COMPRESSOR DISCHARGE SYSTEM...
Страница 54: ...Section 6 ILLUSTRATIONS AND PARTS LIST 48 6 10 ELECTRO PNEUMATIC CONTROL SYSTEM...
Страница 56: ...Section 6 ILLUSTRATIONS AND PARTS LIST 50 6 10 ELECTRO PNEUMATIC CONTROL SYSTEM...
Страница 58: ...Section 6 ILLUSTRATIONS AND PARTS LIST 52 6 11 SULLICON CONTROL...
Страница 60: ...Section 6 ILLUSTRATIONS AND PARTS LIST 54 6 11 SULLICON CONTROL...
Страница 62: ...Section 6 ILLUSTRATIONS AND PARTS LIST 56 6 12 INSTRUMENT PANEL ASSEMBLY...
Страница 64: ...Section 6 ILLUSTRATIONS AND PARTS LIST 58 6 13 CONTROL BOX ASSEMBLY...
Страница 66: ...Section 6 ILLUSTRATIONS AND PARTS LIST 60 6 13 CONTROL BOX ASSEMBLY...
Страница 68: ...Section 6 ILLUSTRATIONS AND PARTS LIST 62 6 14 WATER COOLED AFTERCOOLED OPTION BASCO HORIZONTAL MOUNTED...
Страница 70: ...Section 6 ILLUSTRATIONS AND PARTS LIST 64 6 15 AIR COOLED AFTERCOOLED OPTION...
Страница 72: ...Section 6 ILLUSTRATIONS AND PARTS LIST 66 6 15 AIR COOLED AFTERCOOLED OPTION...
Страница 74: ...Section 6 ILLUSTRATIONS AND PARTS LIST 68 6 16 ELECTRICAL SCHEMATIC...
Страница 75: ...NOTES...