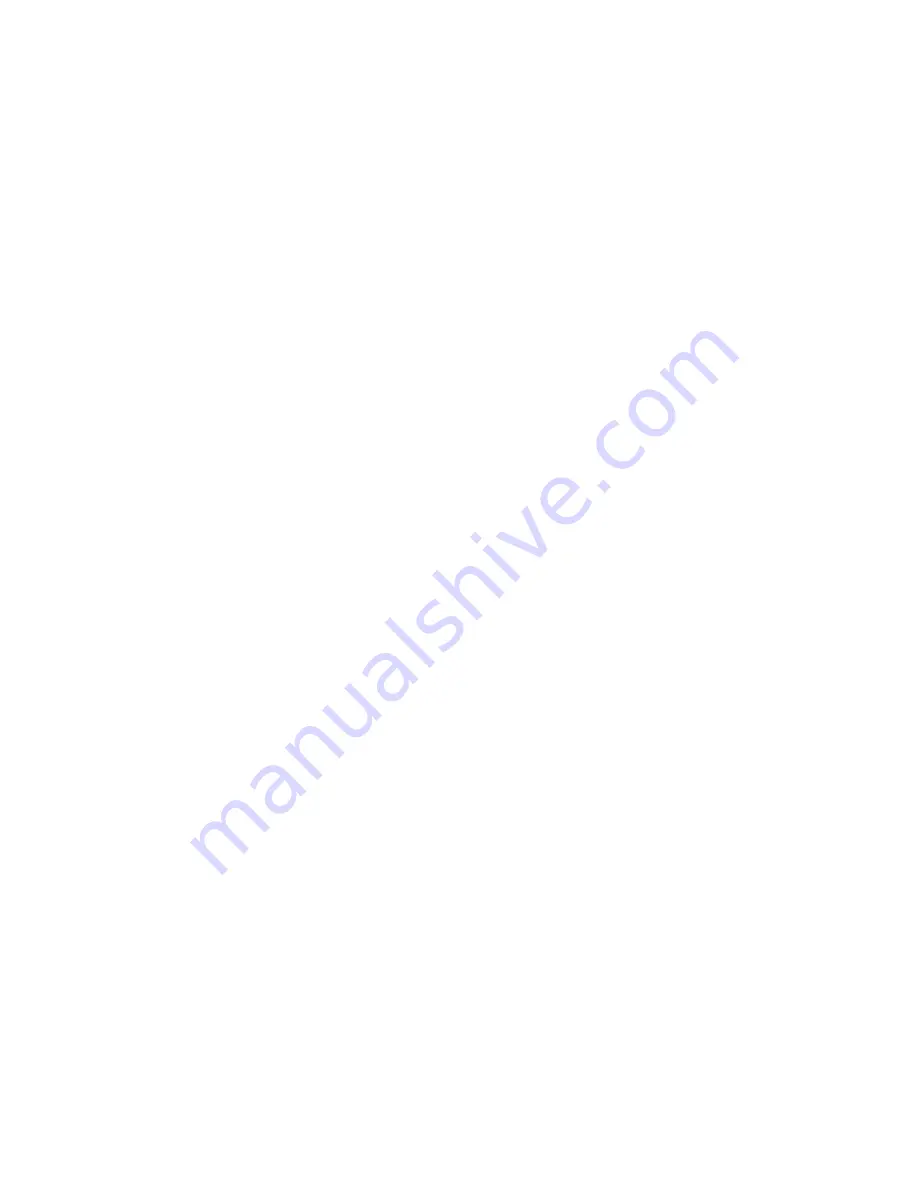
EXACTA 1350-TD SERIES Operating Instructions
Sturtevant Richmont
P/N 857424 Rev
–
07/15/2020
4
The tool will display the target angle in the Idle state. As torque is applied, the measured torque is displayed in large digits,
with an angle of 0°. One yellow LED lights when the Target Torque is reached. The display changes to angle in large digits,
starting at 0°. The other yellow LEDs light up as the angle approaches its target.
•
Target Torque
–
Apply torque to this value to get a yellow LED and start counting angle. This is typically set to the
snug point on the joint (the point at which the head of the fastener has bottomed out).
•
Minimum Torque
–
This is the minimum acceptable torque for the joint.
•
Target Angle
–
This is the minimum acceptable angle. The light band will turn green and status OK when minimum
torque and target angle are met.
•
Maximum Angle
–
This is the maximum acceptable angle. The light band will turn red and status HI if angle exceeds
this setting.
•
Maximum Torque
–
This is the maximum acceptable torque for the joint. While final angle is of primary interest, a
check on final torque may be warranted as well (e.g., to detect a fastener that is too hard to stretch). The light
band will turn red and status HI if the peak value exceeds this setting. Final torque must fall the minimum and
maximum torque settings to be acceptable.
Torque With Angle Monitoring (TAM) Mode
TAM mode is an extension of Peak mode, adding the ability to detect cross-threaded fasteners, double hits on a joint, and
the like. Primarily, it adds the constraint that a fastener must turn through a minimum angle before minimum torque is
reached. TAM mode uses the same settings as Peak mode, plus:
•
Snug Torque
–
This is the torque value at which angle measurement starts. This is typically set to the snug point on
the joint (the point at which the head of the fastener has bottomed out).
•
Target Angle
–
This is the minimum angle needed before minimum torque is reached. The light band will turn red
and status DH (Double Hit) if minimum torque is reached before minimum angle.
•
Maximum Angle
–
This is the maximum acceptable angle. The light band will turn red and status HI if angle exceeds
this setting.
RADIO COMMUNICATIONS - 2.4 GHZ COMMUNICATION OVERVIEW
These tools use the 2.4GHz band for communication with the controller. As with all radio communications, there are limits
on the distance at which reliable bi-directional communication may be obtained. Physical barriers such as steel framing,
sheet metal and other objects that impede radio waves can significantly reduce the reliable communication distance.
Another factor affecting the reliability and distance combination is the radio environment in which the unit will be used.
The controller and torque tool may operate on any of the 12 channels these products use. It is generally best to think about
this even before the unit is installed.
The radio modules in the controllers and torque tooles used with them comply with the IEEE 802.15.4 standard. The
channel numbers loosely match the channels used by the IEEE 802.11b/g WLAN standard. It may be beneficial to use
channels that do not match the channels used by a nearby wireless network. Refer to the controller user manual for the
specific frequencies being used.
Notice that the channels we use have a much smaller footprint than WLAN. Also notice that one WLAN channel radiates
energy onto several of the adjacent WLAN and controller channels. For the most reliable communication between the SR
controller and the tool in an 802.11b/g LAN environment, it is usually best to choose a channel for the controller and tool
that is separated from the channel of the LAN.
ESTABLISHING RF COMMUNICATION WITH SR CONTROLLERS
The transceiver in the controller and the one in the torque tool each have identification numbers. When communication
between the two is first established, the numbers are exchanged and stored in memory. The controller and tool will
thereafter ignore communications from other radios until the number stored in memory is replaced with a different
identification number.
Under all conditions, the controller and the tool to be used with it must be on the same channel. If the channel on the
controller is changed and the channel on the tool is not, they will not communicate or will cease communicating if they
have previously been associated with each other. To establish communication with the controller, it is necessary to follow
the instructions included with the specific controller to be used. Refer to the Global 400 or Global 400mp user manual for
details.