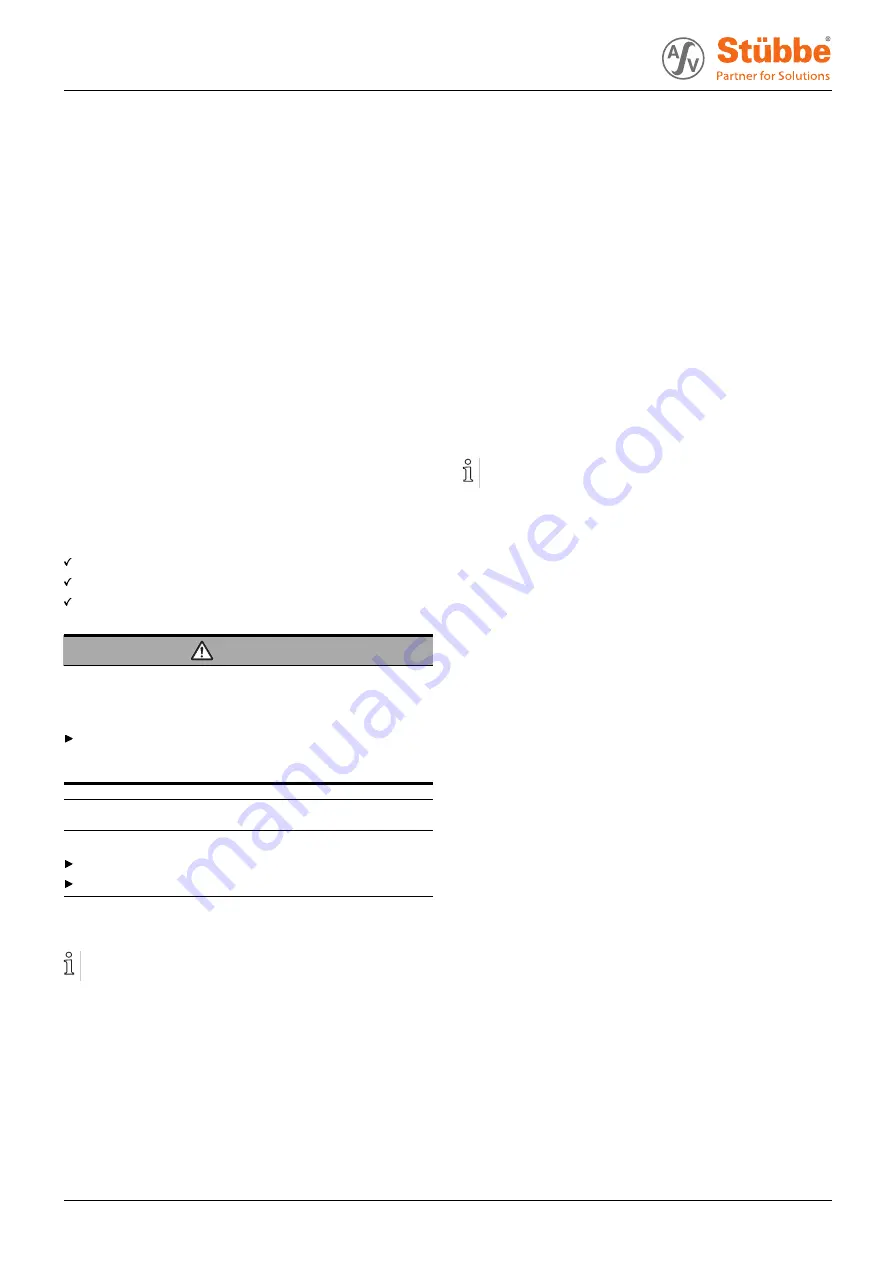
Installation and connection
8. Check the
fi
ll level in the upper part (2) and depending on
the situation proceed as follows:
–
If the
fi
ll level is suf
fi
cient: continue with process step 9.
– OR –
–
If the
fi
ll level is too low: Top up the transmitter
fl
uid
(4) in the upper part (2). Repeat process steps 1 to 8
until there is suf
fi
cient transmitter
fl
uid in the pressure
gauge.
9. Check the thread seal, and depending on the type of thread
proceed as follows:
–
Imperial thread: Ensure that the gasket (3) seals the
pressure gauge.
– OR –
–
Pipe thread and NPT thread: Wrap a maximum of 4
turns of sealing tape around the thread of the pressure
gauge (1).
10. Screw the pressure gauge (1) clockwise into the upper
part (2)
9.4 Tightening torques, Page 12).
11. Ensure the pressure gauge (1) is zeroed.
The
fi
tting is now ready for mounting on the pipeline.
5.4
Installing
fi
tting in pipe
The pressure gauge must be mounted on the
fi
tting.
The
fi
tting must be
fi
lled with the transmitter
fl
uid.
The pressure gauge must be
fi
lled with the transmitter
fl
uid.
WARNING
Risk of poisoning and environmental damage from
medium.
Leak due to faulty installation.
Installation work on the pipes should only be performed
by technicians who have been specially trained for the
pipework in question.
NOTE
Material damage due to contamination of the
fi
tting!
Make sure no contamination reaches the
fi
tting.
Flush the pipe with a neutral medium.
5.4.2
Connection with solvent welding/butt-weld
spigot ends
Use suitable solvent welding/fusion socket ends.
1. Prepare pipe ends according to connection type.
2. Align the
fi
tting together with the pressure gauge, prefer-
ably upwards.
3. Adhesively apply or weld
fi
tting with solvent welding/fusion
socket ends.
5.4.3
Connection with internal thread
fi
xed
1. Prepare pipe ends according to connection type.
2. Check the thread seal on the bottom section of the
fi
tting,
and depending on the type of thread proceed as follows:
–
Imperial thread: Mount a gasket on the threaded con-
nector.
– OR –
–
Pipe thread and NPT thread: Wrap a maximum of 4
turns of sealing tape around the thread of the threaded
connector.
3. Align the
fi
tting together with the pressure gauge, prefer-
ably upwards.
4. Screw the
fi
tting on to the threaded connector
9.4 Tightening torques, Page 12).
5.5
Performing the hydrostatic test
Pressure test using neutral medium, e.g. water.
1. Pressurize the
fi
tting, ensuring
–
Test pressure < permissible system pressure
–
Test pressure < 1.5 PN
–
Test pressure < PN + 5 bar
2. Check the
fi
tting for leaks.
8
MDM 902
BA-2017.09.21 EN
301 287