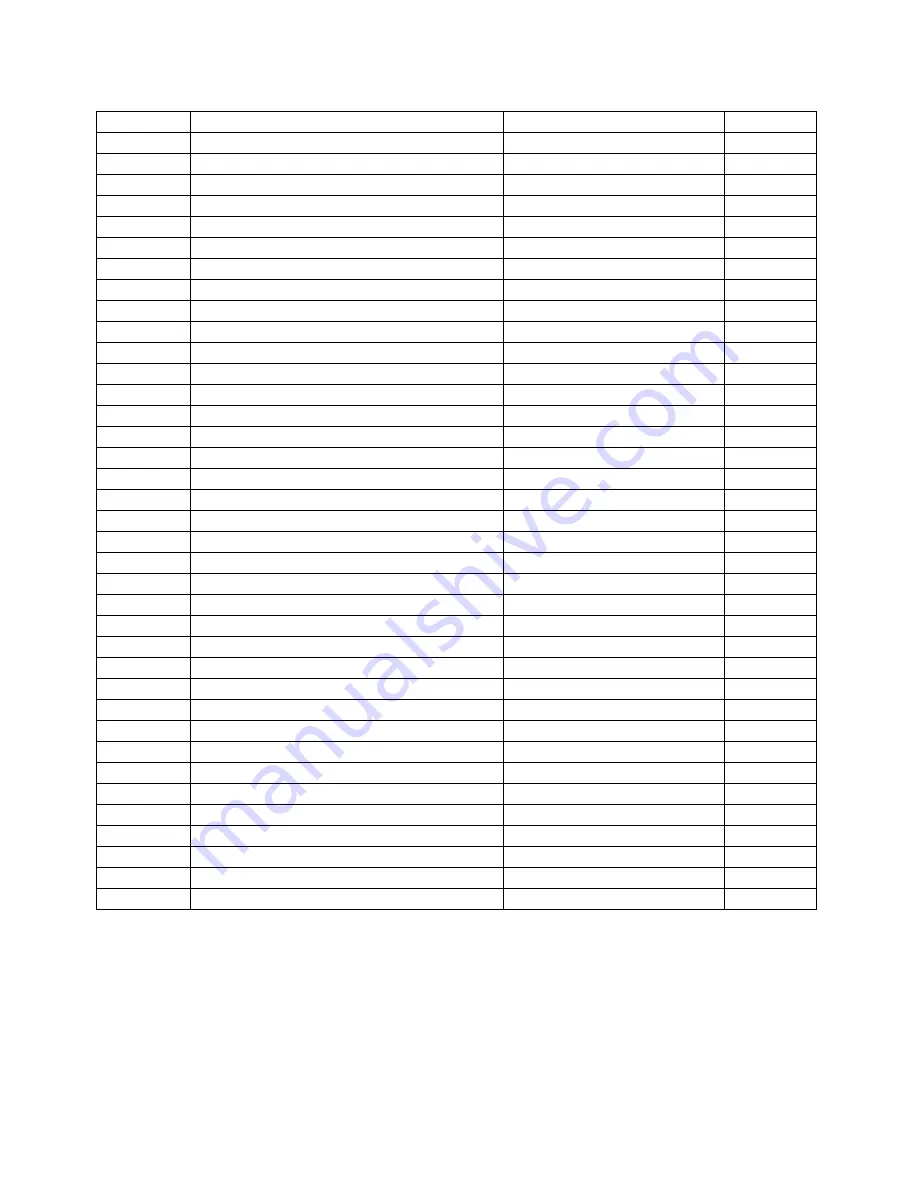
24
PUMP ASSEMBLY PARTS LIST
Index #
Description
Part No.
Qty.
61
Base
TY12001.2-04
1
62
Filter
QF4-16
1
63
Seal
QF4-9
2
64
Reservoir
TY20005.1-01
1
65
Top Nut
QF4-10
1
66
Pump Foot
TY12001.2.5
1
67
Nut M18
GB6172-86
1
68
O-Ring 7.7X1.9
QLQ2.1-17
3
69
Dipstick
QF4.1
1
70
Ball Φ5
GB308-84
1
71
Ball Φ8
GB308-84
2
72
Spring
QF4-13
1
73
Screw M10X1
QF4-12
1
74
Release Valve Stem
QF4.2A
1
75
Seal
QF4-14
1
76
O-Ring 18X3.55G
GB3452.1-92
1
77
Seal
QF4-41
1
78
Clamping Nut
QF4-17
1
79
O-Ring 11.6x2.65
QF4-42
1
80
Seal
QF4-18
1
81
Piston
QF4-2
1
82
Socket
QF4-5a
1
83
Piston Pin
QF4-3
1
84
Pin Φ10
QF4-1
1
85
Snap Ring 10
GB894.1-86
1
86
Handle
TY20005.1-01
1
87
Handle Grip
QF4-7
1
88
Hose
TY12001.2.3
1
89
Coupling
QF4.4
1
90
Dust Cap
QF4-15
1
91
Ball Φ4
GB308-84
1
92
Spring Plunger
QLQ2.1-16
1
93
Spring
QLQ2.1-15
1
94
O-Ring 5.8X2.8
QLQ2.1-14
1
95
Screw M10X1
QF4-20
1
96
Plastic Cap
QF4-21
1
97
Screw M5
QF10-5
2
Содержание 46271
Страница 19: ...19 ASSEMBLY DIAGRAM ...
Страница 21: ...21 RAM ASSEMBLY DIAGRAM ...
Страница 23: ...23 PUMP ASSEMBLY DIAGRAM ...