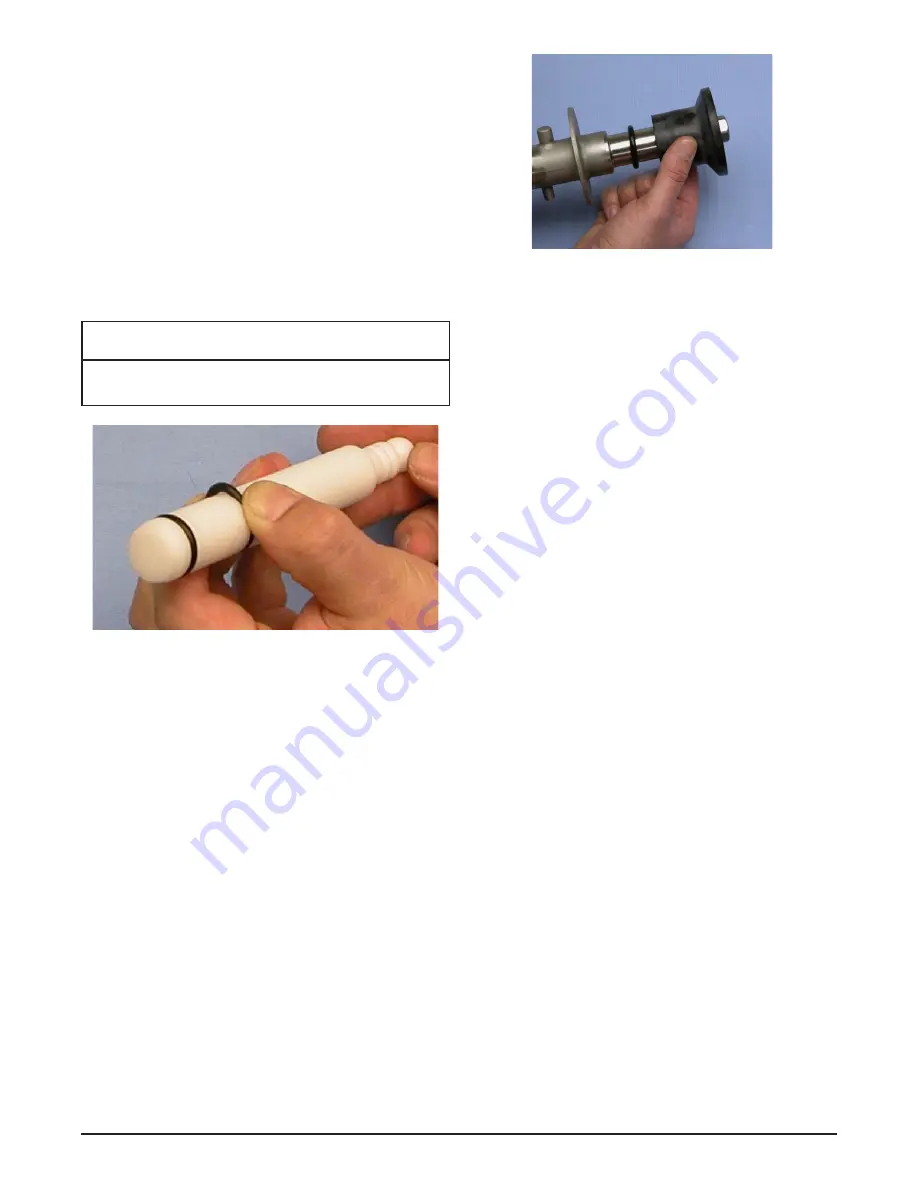
Operators Manual #513686
9
O111-I2F Model Machines
To disassemble the machine, refer to the following steps:
A. DISASSEMBLY OF FRONT DOOR
1.
Press and hold the Main Freezer Power button
for three seconds to turn the power off.
2.
Remove the knobs on the front door.
3.
Remove the front door by pulling it off the studs.
4.
Remove the spigot through the bottom of the front
door.
5.
Remove all o-rings from parts by first wiping off
the lubricant using a clean towel. Then squeeze
the o-ring upward to form a loop (Fig. 3-4). Roll
the o-ring out of the groove.
B. DISASSEMBLY OF AUGER
1.
Remove the front auger support and bushing.
2.
Remove the auger assembly from the machine.
Pull the auger out of the freezing cylinder slowly.
As the auger is being pulled out, carefully remove
each of the plastic flights with springs.
3.
Keep the rear of the auger tipped up once it is
clear of the freezing cylinder to prevent the rear
seal assembly from dropping.
4.
Wipe the spline lubricant off of the hex end of the
auger with a paper towel. Remove the rear seal
assembly (Fig. 3-5).
5.
Wipe any excess lubricant off the rear seal.
6.
Unscrew the springs from the auger flights.
3.5 CLEANING DISASSEMBLED PARTS
Disassembled parts require complete cleaning, sanitizing
and air drying before assembling. Local and state health
codes dictate the procedure required. Some state health
codes require a four sink process (pre-wash, wash, rinse,
sanitize, air dry), while others require a three sink process
(without the pre-wash step). The following procedures
are a general guideline only. Consult your local and state
health codes for the procedures required in your location.
A.
Disassemble all parts. (Refer to Section 3.4 for
the disassembly of machine parts)
B.
Place all parts in 90° to 110°F (32°C to 43°C)
mild detergent water and wash thoroughly. Use
the brushes that shipped with the machine to
clean all holes in the front door, flights, mix pickup
assembly, etc.
C.
Rinse all parts with clean 90° to 110°F (32°C to
43°C) water.
D.
Place all parts in a sanitizing solution for at least
1 minute, then remove and let air dry completely
before assembling in machine.
3.6 CLEANING THE MACHINE
The exterior should be kept clean at all times to preserve
the luster of the stainless steel. A high grade of stainless
steel has been used on the machine to ease cleanup. To
remove spilled or dried mix, wash the exterior with 90° to
110°F (32°C to 43°C) mild detergent water and wipe dry.
Do not use highly abrasive materials, as they will mar the
finish. Use a soft cloth or sponge to apply the solution.
For best results, wipe with the grain of the steel.
A.
Clean the rear seal surface on the inside of the
freezing cylinder.
B.
Using sanitizing solution and the large barrel
brush provided, sanitize the freezing cylinder by
dipping the brush in the sanitizing solution and
brushing the inside of the freezing cylinder.
C.
Wrap the brush in a clean sanitized cloth and
thoroughly dry the freezing cylinder.
D.
Remove the drip tray from the front panel. Clean
and replace the drip tray.
Figure 3-4 Removing O-Ring
Figure 3-5 Rear Seal Assembly
CAUTION
Do not use any type of sharp object to remove the
o-rings.
Содержание O111-I2F
Страница 1: ...Model O111 I2F OPERATORS MANUAL Manual No 513686 Rev 1 ...
Страница 2: ......
Страница 6: ......
Страница 12: ...Operators Manual 513686 6 O111 I2F Model Machines ...
Страница 24: ...Operators Manual 513686 18 O111 I2F Model Machines ...
Страница 28: ...Operators Manual 513686 22 O111 I2F Model Machines ...