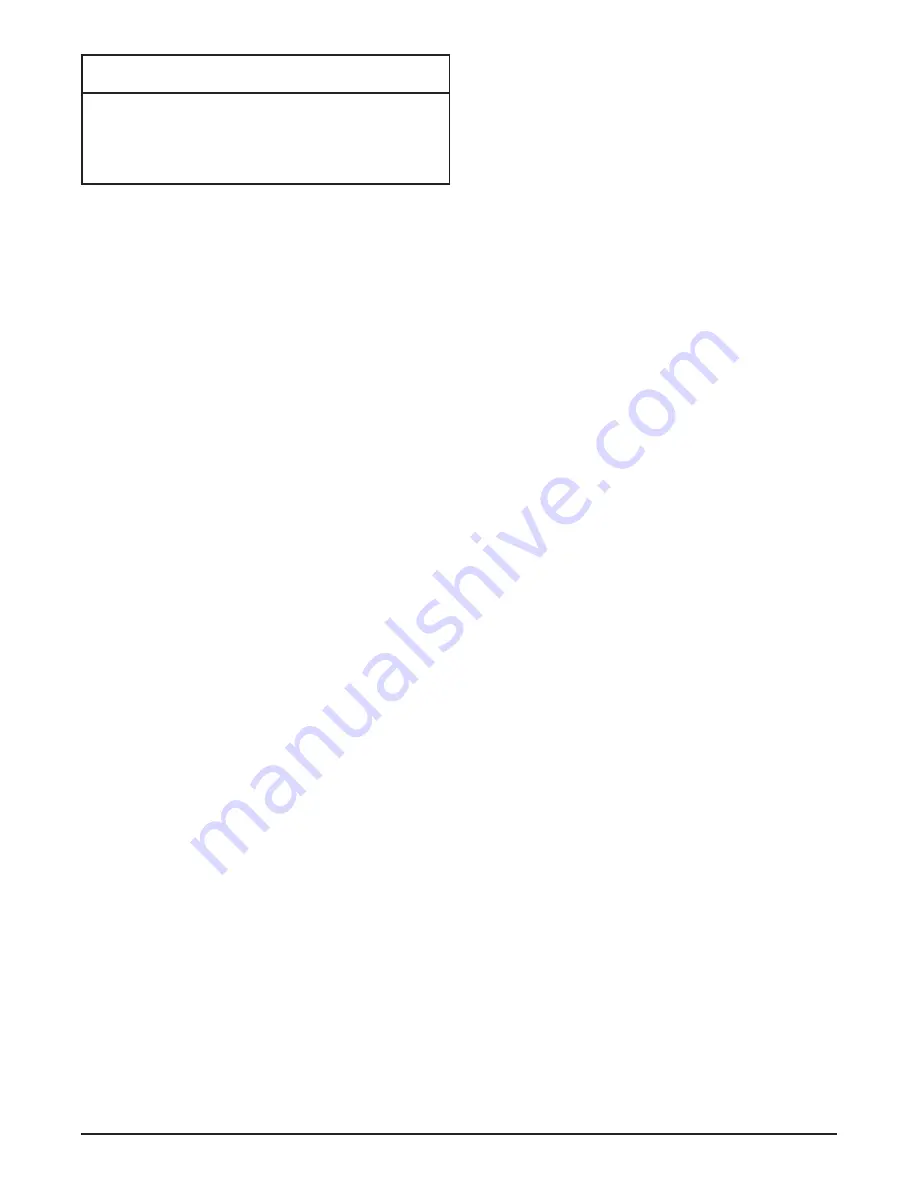
Owner’s Manual #513613
13
E112/F112 Model Machines
N.
Insert the spigot handle so the hole lines up and
insert the spigot pin.
O.
Install the mix inlet regulator into the hopper if
using shake mix. If using slush mix, the mix inlet
regulator is not required.
P.
Install the hopper cover, drain tray, drip tray, and
drip tray grid.
3.12 ROUTINE CLEANING
To remove spilled or dried mix from the machine exterior,
wash in the direction of the fi nish with warm soapy water
and wipe dry. Do not use highly abrasive materials as
they will mar the fi nish.
3.13 PREVENTIVE MAINTENANCE
Stoelting recommends that a maintenance schedule be
followed to keep the machine clean and operating properly.
CLEANING AND SANITIZING INFORMATION
Special consideration is required when it comes to food
safety and proper cleaning and sanitizing.
The following information has been compiled by Purdy
Products Company, makers of Stera-Sheen Green La-
bel Cleaner/Sanitizer and specifi cally covers issues for
cleaning and sanitizing frozen dessert machines. This
information is meant to supplement a comprehensive
food safety program.
SOIL MATERIALS ASSOCIATED WITH FROZEN
DESSERT MACHINES
MILKFAT/BUTTERFAT – As components of ice-cream/
frozen custard mix, these soils will accumulate on the
interior surfaces of the machine and its parts. Fats are
diffi cult to remove and help attribute to milkstone build-up.
MILKSTONE – Is a white/gray fi lm that forms on equip-
ment and utensils that come in contact with dairy products.
These fi lms will accumulate slowly on surfaces because of
ineffective cleaning, use of hard water, or both. Milkstone
is usually a porous deposit, which will harbor microbial
contaminants and eventually defy sanitizing efforts.
Once milkstone has formed, it is very diffi cult to remove.
Without using the correct product and procedure, it is
nearly impossible to remove a thick layer of milkstone.
(NOTE: general-purpose cleaners DO NOT remove
milkstone.) This can lead to high bacteria counts and a
food safety dilemma.
IT IS BEST TO CONTROL MILKSTONE ON A DAILY BA-
SIS BEFORE IT CAN BECOME A SIGNIFICANT FOOD
SAFETY PROBLEM.
In addition to food safety, milkstone can cause premature
wear to machine parts which can add to costs for replace-
ment parts or possibly more expensive repairs if worn
machine parts are not replaced once they have become
excessively worn.
IMPORTANT DIFFERENCES BETWEEN CLEANING
AND SANITIZING
CLEANING vs. SANITIZING
It is important to distinguish between cleaning and sanitiz-
ing. Although these terms may sound synonymous, they
are not. BOTH are required for adequate food safety and
proper machine maintenance.
CLEANING
•
Is the removal of soil materials from a surface.
•
Is a prerequisite for effective sanitizing.
NOTE
An UNCLEAN surface will harbor bacteria that can
defy sanitizing efforts.
Bacteria can develop and resist sanitizing efforts within
a layer of soil material (milkstone). Thorough cleaning
procedures that involve milkstone removal are critical for
operators of frozen dessert machines.
SANITIZING
• Kills
bacteria.
•
Can be effective on clean surfaces only.
NOTE
Using a SANITIZER on an unclean surface will not
guarantee a clean and safe frozen dessert machine.
PROPER DAILY MAINTENANCE: THE ONLY WAY TO
ASSURE FOOD SAFETY AND PRODUCT QUALITY
Proper daily maintenance can involve a wide variety
of products and procedures. Overall, the products and
procedures fall into three separate categories. (Please
note that this is a brief overview intended for informational
purposes only.)
1.
CLEANING – This involves draining mix from
the freezing cylinder and rinsing the machine
with water. Next, a cleaner is run through the
machine. Then, the machine is disassembled
and removable parts are taken to the sink for
cleaning.
2.
MILKSTONE REMOVAL – Since almost all
cleaners do not have the ability to remove
milkstone, the use of a delimer becomes
necessary. Although this procedure may not be
needed on a daily basis, it will usually follow the
cleaning procedure. It requires letting a delimer
solution soak in the machine for an extended
period of time. Individual parts are also soaked in
a deliming solution for an extended period of time
(more about delimers in Additional Information).
CAUTION
Do not place the mix inlet regulator into the hopper
before installing the auger. Attempting to install the
auger with the mix inlet regulator in place will dam-
age the regulator.
Содержание E112
Страница 1: ...Model E112 F112 OPERATORS MANUAL Manual No 513613 Rev 7...
Страница 2: ......
Страница 6: ......
Страница 10: ...Owner s Manual 513613 4 E112 F112 Model Machines...
Страница 22: ...Owner s Manual 513613 16 E112 F112 Model Machines...
Страница 30: ...Owner s Manual 513613 24 E112 F112 Model Machines...