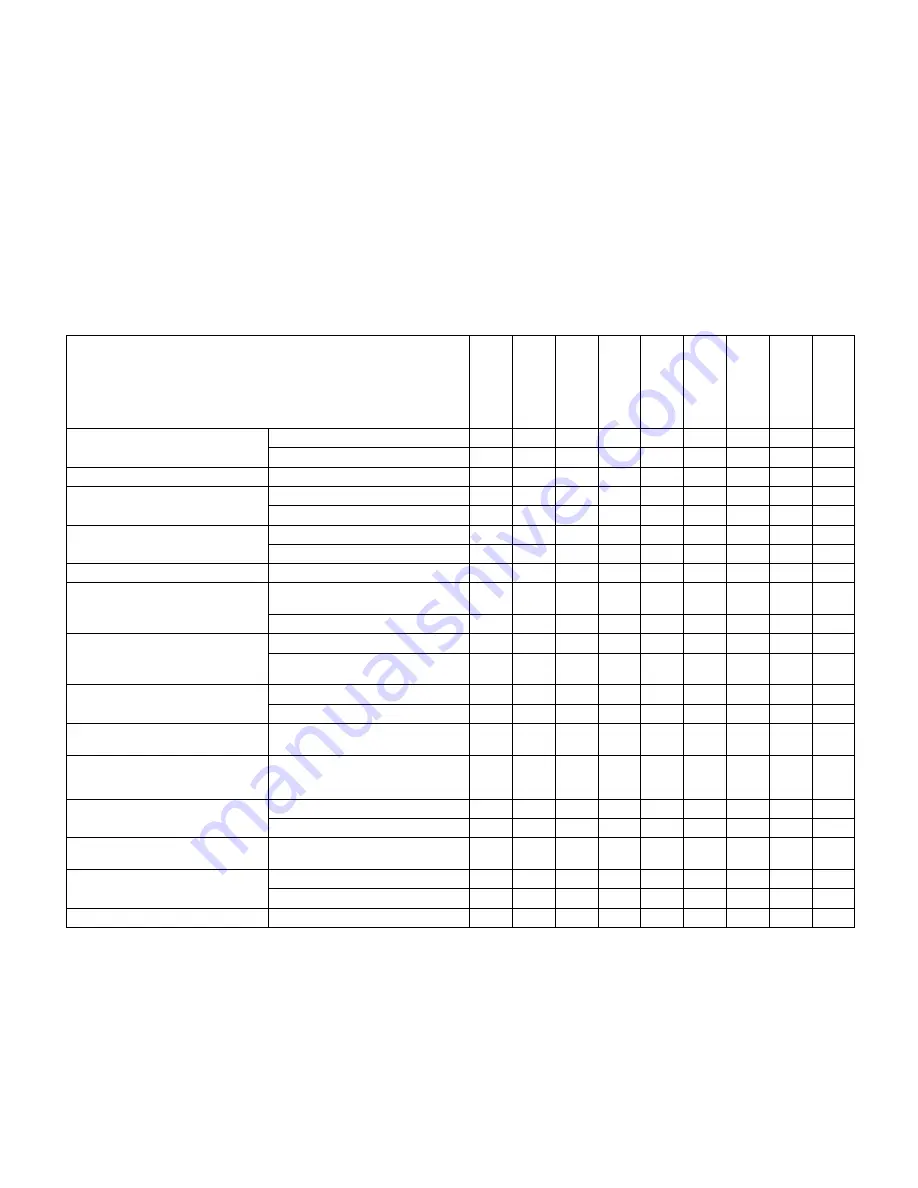
29
KM 110, KM 130
English / USA
1) STIHL recommends the STIHL
dealer
*
see “Guide to Using this Manual“
Maintenance Chart
Please note that the following maintenance intervals apply for normal operating
conditions. If your daily working time is longer than normal or cutting conditions
are difficult (very dusty work area etc.), shorten the specified intervals accordingly
bef
ore
st
art
ing work
af
te
r fin
ishing
w
ork or
d
a
ily
af
te
r each
ref
uelin
g st
op
we
e
kl
y
m
ont
hly
e
ver
y 12
m
on
ths
if pro
b
lem
if dama
ged
as re
quire
d
Complete machine
Visual inspection (condition, leaks)
X
X
Clean
X
Control handle
Check operation
X
X
Air filter
Clean
X
X
Replace
X
Pick-up body in fuel tank
Have checked by dealer
1)
X
Have replaced by dealer
1)
X
X
X
Fuel tank
Clean
X
X
Carburetor
Check idle adjustment - tool must not
move
X
X
Readjust idle
X
Spark plug
Readjust electrode gap
X
Replace after about 100 operating
hours
Cooling inlets
Inspect
X
Clean
X
Valve clearance
Check, readjust if necessary, after first
139 hours of operation
X
Combustion chamber
Decarbonize after first 139 hours of
operation, then every 150 hours of
operation
X
Spark arresting screen* in muffler
Inspect
X
X
Replace
X
X
All accessible screws and nuts
(not adjusting screws)
Retighten
X
Anti-vibration element
Check
X
X
Have replaced by dealer
1)
X
Safety labels
replace
X
Содержание HL-KM
Страница 1: ... i 1 f _ __ _______ ____J ...
Страница 62: ...40 English USA KM 110 KM 130 ...