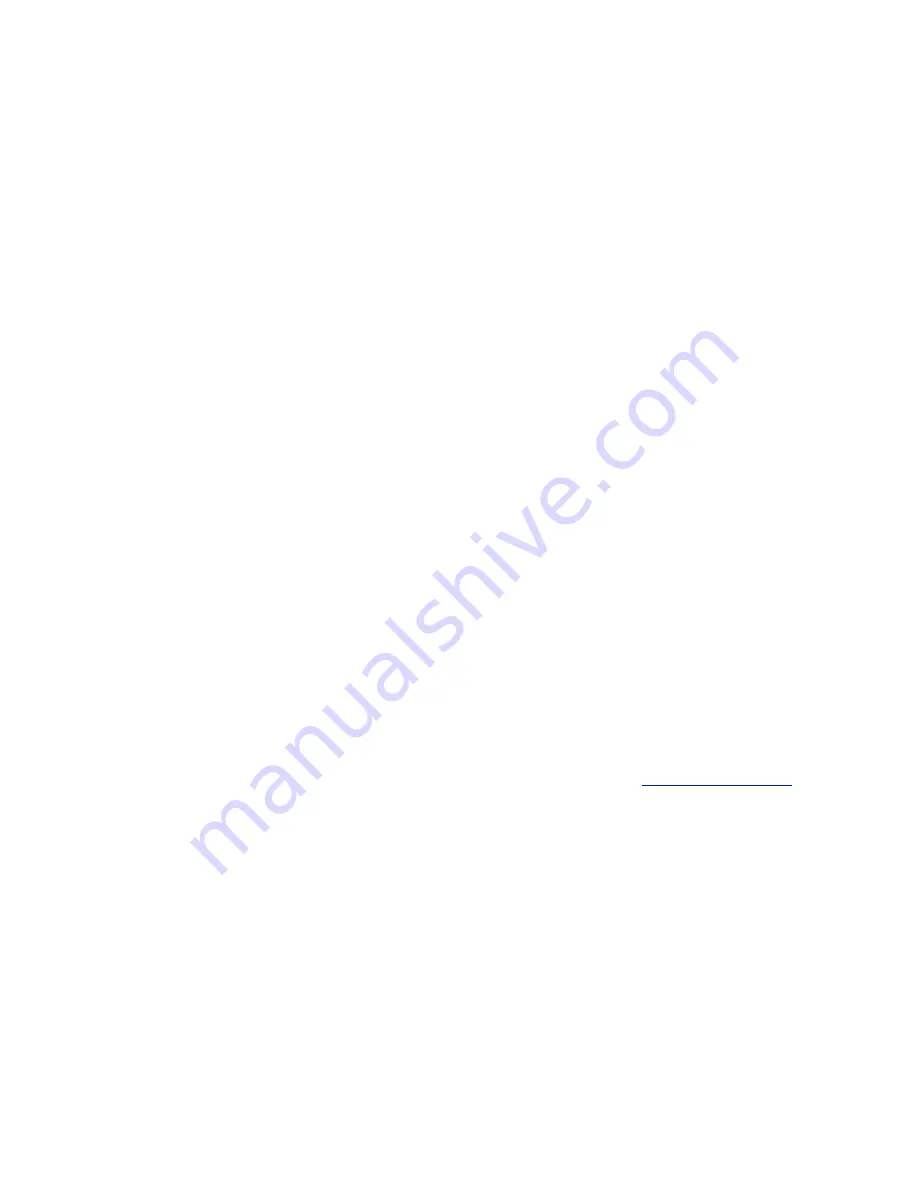
General Assembly Instructions
Thank you, for purchasing this Stevens
Rockette
™ (100). A micro indoor flyer based
upon the Rocketeer A. This product has been
developed and manufactured using state of the
art CAD/CAM systems and features a unique
interlocking construction process that, when
compared to traditional methods found in other
model aircraft kits, save countless hours of
measuring, cutting, sanding, and fitting. We are
certain that you’ll find our kit to offer a truly
exceptional build experience. As this kit is
recommended for the novice model builder and
pilot; we invite beginners who have purchased
this kit to seek the help of a seasoned builder and
pilot. At any time should one run across a term or
technique that is foreign please don’t hesitate to
contact our staff with your questions.
READ THIS!
Please
READ
and
RE-READ
these instructions
along with any other included documentation prior
to starting your build and/or contacting our staff
for builder support.
Pre-sanding
Do not skip this step. Prior to removing any parts
from the laser cut sheet wood use a sanding
block loaded with 250-400 grit paper and lightly
sand the back side of each sheet of wood. This
step removes any residue produced as a result of
the laser cutting process and, as we have found
that most stock wood sizes run several
thousandths of an inch over sized, slightly
reduces the thickness of each sheet.
Leave your pre-sanded parts in the sheet until
required in the assembly process.
Protecting your worktable
Use the poly tube that this kit was shipped in as a
non-stick barrier between your worktable and the
product assembly. Promptly clean up any epoxy
spills with rubbing alcohol and a disposable towel.
Bonding the assembly
As this product tabs, notches, and otherwise
interlocks like a 3D puzzle we suggest that when
fitting parts you dry fit (use no glue) the parts
together first. It’s advised to work 1-2 steps
ahead in the instructions using this dry-fit
technique which allows ample opportunity to
inspect the fit and location of assembled
components and realizes a benefit as each
successive part contributes to pulling the entire
assembly square. Once you arrive at the end of a
major assembly sequence square your work on
top of a flat building table and revisit the dry fit
joints with glue. Using the dry-fit process you’ll be
able to recover from a minor build mistake and
will ultimately end up with a more square and true
assembly.
Unless otherwise noted in the instructions we find
it easier to tack glue part (temporarily bonding
parts in assembly using a small dot of glue) using
medium CA glue applied with a fine-tip CA glue
applicator tip. Tight fitting joints should be bonded
using thin CA glue applied, sparingly, with a CA
glue applicator tip.
Never force the fit!
Remember this is a precision cut kit our machines
cut to within 5 thousandth of an inch in accuracy.
Yet the wood stock supplied by the mill may vary
in thickness by up to 20 thousandths. This
variance in the wood stock can cause some tabs/
notches to fit very tight. With this in mind,
consider lightly sanding, or lightly pinching, a tight
fitting tab rather than crushing and forcing your
parts together. You’ll break fewer parts in
assembly and will end up with a more square and
true airframe.
Manual Updates
Please check our web-site for updates to these
instructions prior to commencing the build.
While not required for proper assembly of this
model, full-color photos following the build
sequence given in this instruction manual are
available to download at
www.stevensaero.com
To obtain downloads and updates relative to this
model aircraft kit, please visit the corresponding
product page at StevensAero.com
Build Instructions
© 2011 Stevens AeroModel all rights reserved.
!
Page 4 of 10