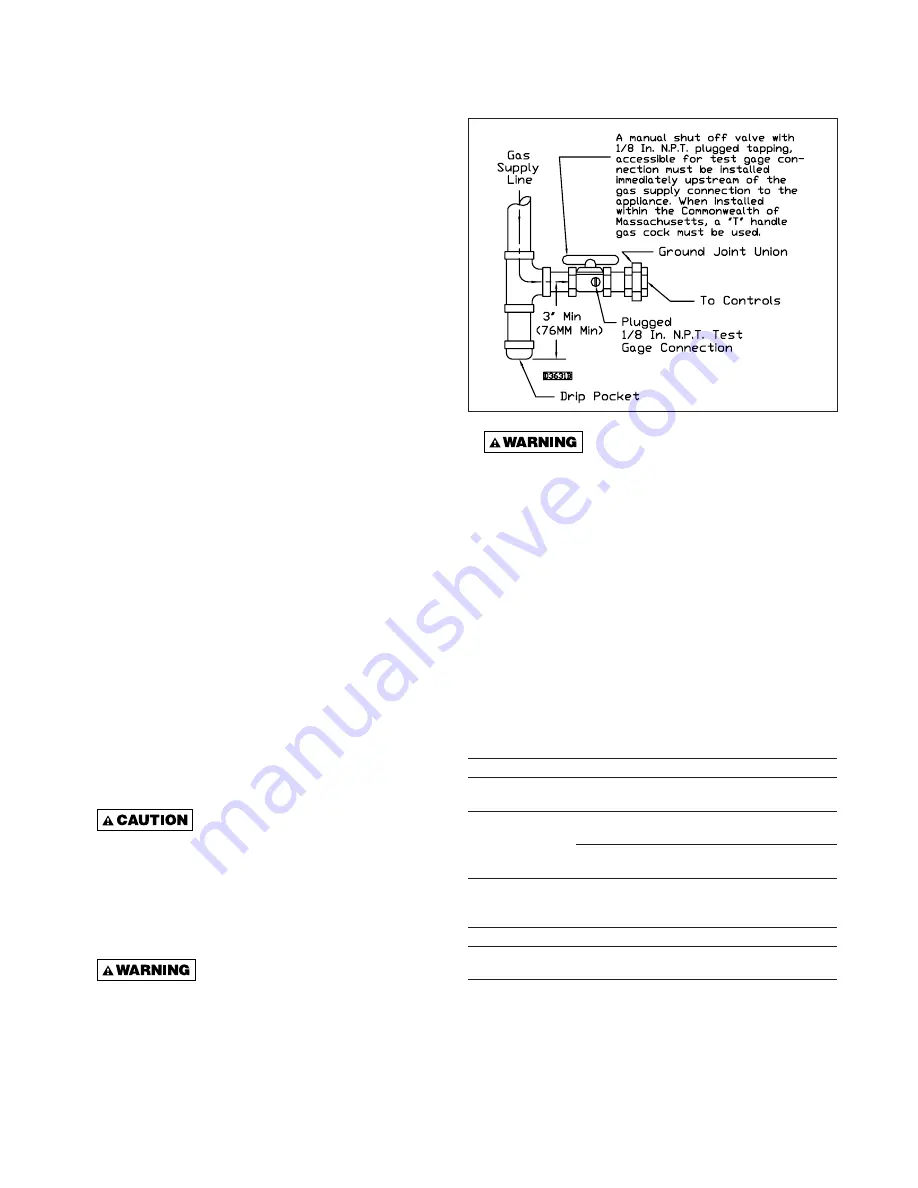
Figure 4 - Pipe Installation, Standard Controls
Never use an open fl ame to detect
gas leaks. Explosive conditions may exist which
would result in personal injury or death.
The appliance and its individual shutoff valve must
be disconnected from the gas supply piping system
during any pressure testing of that system at test
pressures in excess of 1/2 psig (3.5 kPa).
The appliance must be isolated from the gas supply
piping system by closing its individual manual shutoff
valve during any pressure testing of the gas supply
piping system at test pressures equal to or less than
1/2 psig (3.5 kPa).
Table 4 - Gas Piping Requirements
SINGLE STAGE GAS PIPING REQUIREMENTS*
Gas Type
Natural Gas
Propane (LP) Gas
Manifold
3.5 in. W.C.
10.0 in. W.C.
Pressure
(0.9 kPa)
(2.5 kPa)
14.0 in. W.C. Max.
14.0 in. W.C. Max.
Supply Inlet
(3.5 kPa)
(3.5 kPa)
Pressure
5.0 in. W.C. Min.
11.0 in W.C. Min.
(1.2 kPa)
(2.7 kPa)
*
For single stage application only at normal altitudes.
TWO STAGE GAS PIPING REQUIREMENTS**
Gas Type
Natural Gas
Propane (LP) Gas
Supply Inlet
6.5 in. W.C. Min.
11.5 in. W.C. Min.
Pressure
(1.6 kPa)
(2.9 kPa)
**For two stage applications only at normal altitudes; two stage
applications do not apply to the 30/75 MBH models.
8
PIPE INSTALLATION
1. Install the gas piping in accordance with applicable
local codes.
2. Check gas supply pressure. Each unit heater must
be connected to a manifold pressure and a gas
supply capable of supplying its full rated capacity
(see tabe 4). A field LP tank regulator must be
used to limit the supply pressure to maximum of
14 in. W.C. (3.5 kPa). All piping should be sized in
accordance with the latest edition of ANSI Standard
Z223.1, National Fuel Gas Code; in Canada,
according to CAN/CGA B149. See Tables 1 and 3
for correct gas supply piping size. If gas pressure
is excessive on natural gas applications, install a
pressure regulating valve in the line upstream from
the main shutoff valve.
3. Adequately support the piping to prevent strain on
the gas manifold and controls.
4. To prevent the mixing of moisture with gas, run
the take-off piping from the top, or side, of the
main.
5. Separated combustion unit heaters optional two-
stage units, and hydraulic modulating units are
supplied with a combination valve which includes:
(a) Manual “A” valve (b) Manual “B” valve
(c) Solenoid valve (d) Pilot safety (e) Pressure
regulator
Pipe directly in to combination valve (see Figure 4).
6. A 1/8 in. N.P.T. plugged tapping, accessible for test
gauge connection, must be installed immediately
upstream of the gas supply connection to the
appliance.
7. Provide a drip leg in the gas piping near the gas
unit heater. A ground joint union and a manual gas
shutoff valve should be installed ahead of the unit
heater controls to permit servicing. The manual
main shutoff valve must be located external to the
jacket. See Figure 4.
8. Make certain that all connections have been
adequately doped and tightened.
Do not overtighten the inlet gas
piping into the valve. This may cause stresses
that would crack the valve!
NOTICE: Use pipe joint sealant resistant to the
action of liquefied petroleum gases regardless of
gas conducted.
Check all pipe joints for leakage
using a soap solution or other approved method.
Never use an open flame or severe personal
injury or death may occur.
Содержание QVSF 100
Страница 10: ...10 Figure 6...
Страница 11: ...11 Figure 7...
Страница 12: ...12 Figure 8...
Страница 13: ...13 FIGURE 9...