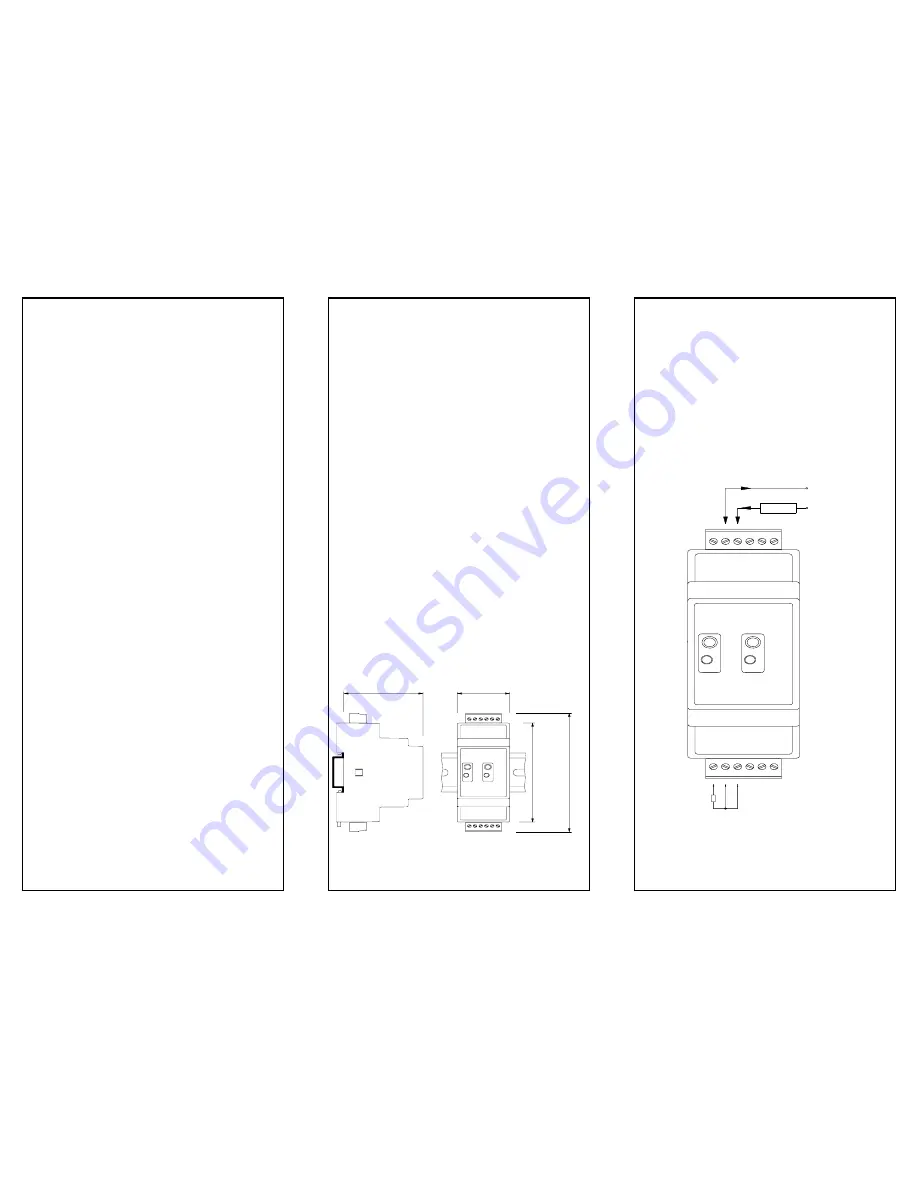
1.0 DESCRIPTION
The transmitter is a dual channel DIN rail mounted 4-20mA transmitter
that connects to any standard Pt100 sensor and converts the sensor
temperature to a 4-20 mA signal.
An LED provides a visual indication of sensor fault and programming
mode. The transmitter is simply ranged and calibrated on the bench by
using a single on-board push button switch, without the need for soldering
links. Digital technology ensures accurate and drift free linearisation to all
common curves, providing a level of performance not possible with earlier
analogue types.
2.0 SPECIFICATION @ 20ºC
2.1 Input
Input Type
3 Wire Pt100
(Pt500 or Pt1000 to special order)
Linearisation
BS EN 60751 (IEC751)
BS 1904 (DIN 43760)
JISC 1604
Excitation Current
1mA Maximum
Range
-200 to 850ºC
Minimum Span
20ºC
Lead Resistance
<10 R per leg (balanced)
Burnout Upscale
22mA
(Downscale preset current to order)
Red programming LED illuminates when
temperature is outside -200 to 850ºC range
Accuracy
±0.1ºC ± 0.1% of reading range -100 to 500
±0.2ºC ± 0.1% of reading range -200 to 850
Thermal Drift
Zero ± 0.01C / ºC
Span 50 ppm
Connections
Screw Terminals Two part
2.2 Output
Output
4 to 20 mA, 2 wire loop powered
Maximum Output Range
3.8 to 22 mA
Operating Voltage
8 to 30 V DC
Accuracy ±
5uA
Thermal Drift
± 1uA/°C
Response Time
500mS to reach 70% of final value
Loop Resistance
800R @ 24 V DC
Loop Sensitivity
0.4 µA / volt
Loop Noise
±0.001 µA
Protection
Reverse Polarity Protected
Connections Screw
Terminals
Input/Output Isolation
Not isolated
Channel to
Warm-up Time
2 Minutes to full accuracy
EMC
Emissions BS EN50081-1
Susceptibility BS EN50082-2
Ambient Temp. Range
0 to 70 ºC
Ambient Storage
-40 to 70 ºC
Ambient Humidity
0 to 95 % (Non condensing)
Default Range
0-100ºC. Contact sales office for factory
configuration to any other range.
3.0 INSTALLATION
3.1 Mechanical
This transmitter has been specifically designed to be mounted on a
universal DIN rail inside an enclosure, which must provide adequate
protection from moisture, corrosive atmosphere etc. All cable entries
should be sealed using the correct size cable gland. Care must be taken
when locating the transmitter to ensure the ambient temperature will
remain inside the specified range of 0 to 70 ºC. The diagrams show the
mechanical layout and a typical application of the transmitter mounted on
a universal DIN rail, with sensor wires entering at the top and bottom of
the unit.
Side View
Front View
Rail (DIN EN 50022-35)
3.2 Electrical
Connections to the transmitter are made by screw terminals. To maintain
CE compliance, input and output wiring must be screened cable with the
screen earthed at one end only. All three input wires must have the same
core diameter to maintain equal lead resistance in each wire.
The transmitter is protected against reverse connection, therefore
incorrect connection of the output wires will result in near zero current
flowin the loop. Incorrect connection of the sensor wires will result in the
transmitter output going to burnout condition.
Figure 2 shows the method of connection to provide a 4-20 mA current
loop output. The Pt100 sensor shown would normally take the form of a
probe assembly with a three wire output. The output loop shows a 24
VDC power supply, used to provide loop excitation, the transmitter, and a
load, all connected in series. The load symbol represents other equipment
in the loop e.g. indicators, controllers, loggers etc.
5 2 .9
3 5 .0
CH1
CH2
9
10
11
12
8
7
1
2
6
3
4
5
8 6 .0
1 0 3 .0
S W IT C H
L E D
Figure 1
+ 2 4 V
0 V
C H 1
C H 2
9
10
11
12
8
7
1
2
6
3
4
5
SW IT CH
LED
L O A D
P T S E N S O R
Figure 2
52-214-2320-01