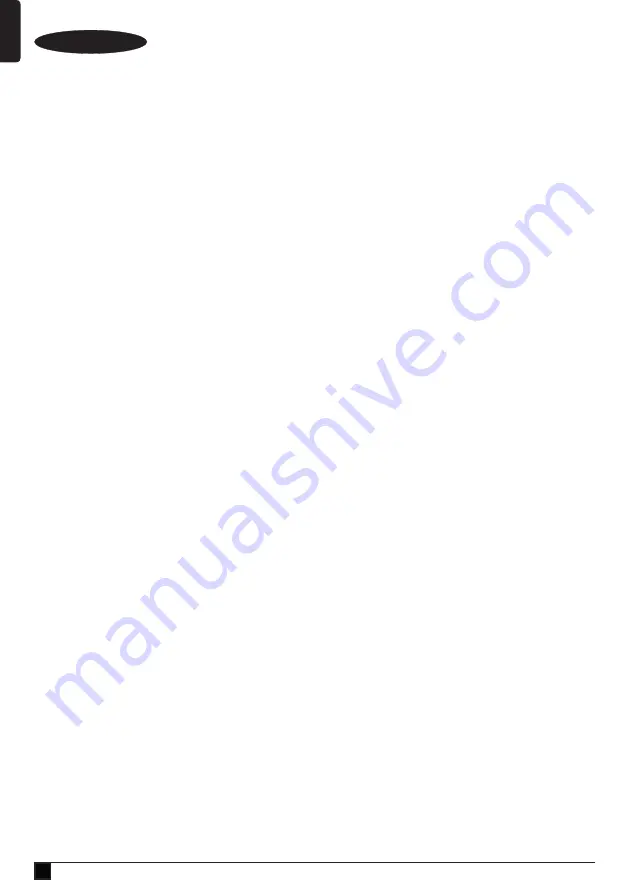
8
ENGLISH
(Original instructions)
Voltage drops
Inrush currents cause short-time voltage drops. Under
unfavourable power supply conditions, other equipment may
be affected.
If the system impedance of the power supply is lower than
0.107 Ω, disturbances are unlikely to occur
Features
This tool includes some or all of the following features.
1. On/off switch
2. Spindle lock
3. Guard
4. Side handle
Assembly
Warning!
Before assembly, make sure that the tool is
switched off and unplugged.
Fitting and removing the guard (fig. A)
The tool is supplied with a guard intended for grinding
purposes only (type 27). If the unit is intended to perform
cutting off operations, a guard specific for this operation (type
41) must be fitted. A suitable guard part numbers N551980
(for 115mm cutting wheel) and N542445 (for 125mm cutting
wheel) are available and can be obtained from Stanley Fat
Max service centres.
Fitting
u
Place the tool on a table, with the spindle (4) facing up.
u
Release the clamping lock (5) and hold the guard (3) over
the tool as shown.
u
Align the lugs (6) with the notches (7).
u
Press the guard down and rotate it counterclockwise to
the required position.
u
Fasten the clamping lock (5) to secure the guard to the
tool.
u
If required, tighten the screw (8) to increase the clamping
force.
Removing
u
Release the clamping lock (5).
u
Rotate the guard clockwise to align the lugs (6) with the
notches (7).
u
Remove the guard from the tool.
Warning!
Never use the tool without the guard.
Fitting the side handle
u
Screw the side handle (4) into one of the mounting holes
in the tool.
Warning!
Always use the side handle.
Fitting and removing grinding discs
(fig. B - D)
Always use the correct type of disc for your application.
Always use discs with the correct diameter and bore size (see
technical data).
Fitting
u
Fit the guard as described above.
u
Place the inner flange (9) onto the spindle (4) as shown
(fig. B). Make sure that the flange is correctly located on
the flat sides of the spindle.
u
Place the disc (10) onto the spindle (4) as shown (fig. B).
If the disc has a raised centre (11), make sure that the
raised centre faces the inner flange.
u
Make sure that the disc locates correctly on the inner
flange.
u
Place the outer flange (12) onto the spindle. When fitting
a grinding disc, the raised centre on the outer flange must
face towards the disc (A in fig. C). When fitting a cutting
disc, the raised centre on the outer flange must face away
from the disc (B in fig. C).
u
Keep the spindle lock (2) depressed and tighten the outer
flange using the two-pin spanner (13) (fig. D).
Removing
u
Keep the spindle lock (2) depressed and loosen the outer
flange (12) using the two-pin spanner (13) (fig. D).
u
Remove the outer flange (12) and the disc (10).
Surface grinding with grinding discs
u
Allow the tool to reach full speed before touching the tool
to the work surface.
u
Apply minimum pressure to the work surface, allowing the
tool to operate at high speed. Grinding rate is greatest
when the tool operates at high speed.
u
Maintain a 20˚ to 30˚ angle between the tool and work
surface as shown in figure F.
u
Continuously move the tool in a forward and back motion
to avoid creating gouges in the work surface.
u
Remove the tool from work surface before turning tool off.
Allow the tool to stop rotating before laying it down.
Edge grinding with grinding discs
Wheels used for cutting and edge grinding may break or kick
back if they bend or twist while the tool is being used to do
cutoff work or deep grinding. Edge grinding/ cutting with a
Type 27 wheel must be limited to shallow cutting and notching,
less than 13 mm in depth when the wheel is new. Reduce the
depth of cutting/notching equal to the reduction of the wheel
radius as it wears down. Refer to the 'Grinding and cutting
accessory chart' at the end of ths manual for more
information. Edge grinding/cutting with a Type 41 wheel
requires usage of a Type 41 guard.
u
Allow the tool to reach full speed before touching the tool
to the work surface.
Содержание FATMAX KFFMEG220
Страница 1: ...www stanley eu 1 13 4 2 3 KFFMEG220...
Страница 2: ...2 13 12 10 3 4 7 5 8 7 6 12 15 14 9 4 4 9 11 12 4 9 10 12 11 A E B C D F A B...
Страница 3: ...3 G H I J K L...
Страница 14: ...14 ENGLISH Original instructions...
Страница 15: ...15 ENGLISH Original instructions...