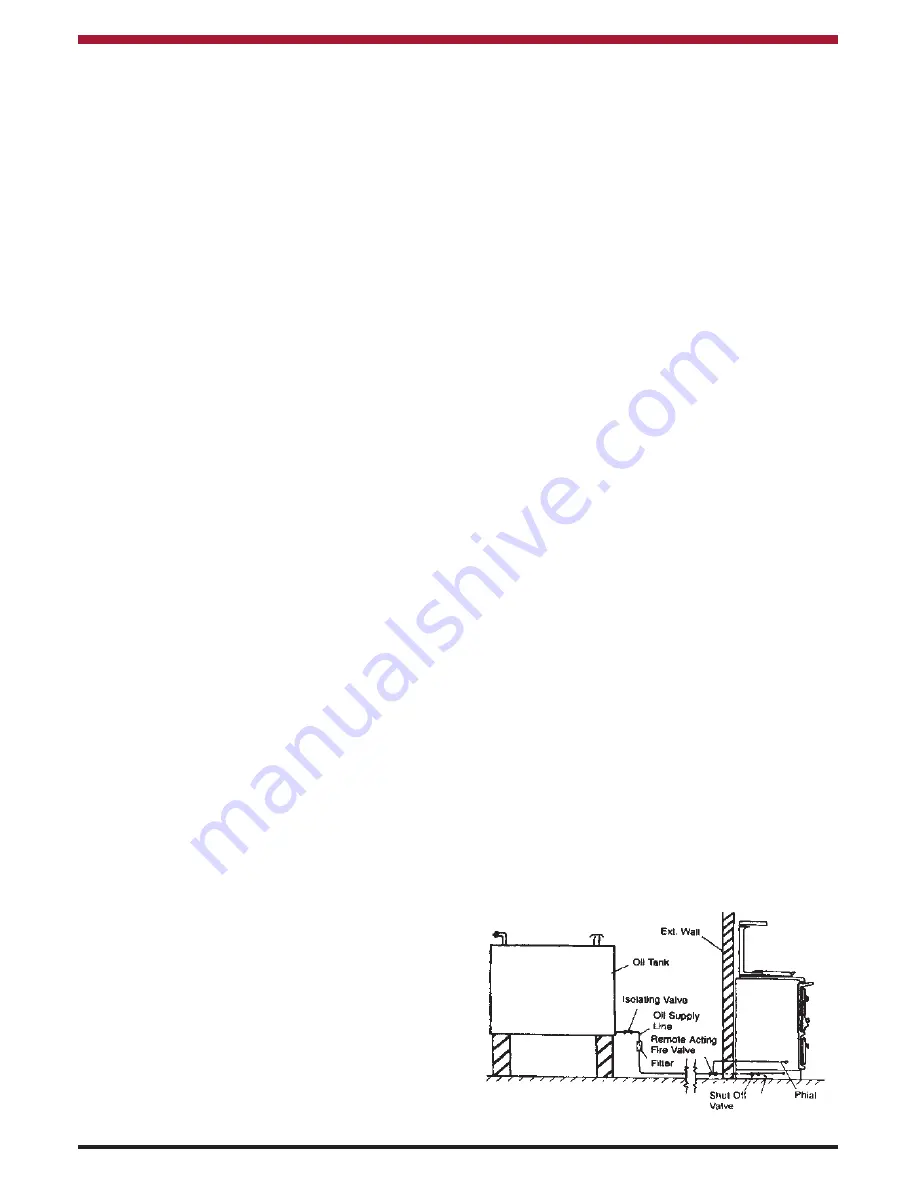
15
FUEL INSTALLATION
OIL STORAGE TANKS
Oil storage tanks made of steel and all connecting
equipment (e.g. filling pipes, and vent pipes) should
comply with B.S. 799 Part 5. Galvanised steel must
not be used. Polyethylene (Plastic) tanks should
comply with OFTEC standard OFS T100 and or
equivalent. Oil should never be stored in transulent
plastic containers.
An isolating valve should be fitted at the tank outlet,
in an accessible position so that the oil supply to the
appliance can be shut off if required. This isolating
valve must be of a type suitable for use with oil.
(See Fig. 20, 21, 22 & 23).
Oil storage tanks support must be carried out in
accordance with the tank manufacture recommen-
dations. Tanks should be located in the most unob-
structive position possible having taken safety, fill-
ing, maintenance and the need, if any, to provide a
head of oil for the burner into consideration.
FUELS
THE RECOMMENDED FUEL FOR THE COOKER
BURNER IS KEROSENE 28 (CLASS 2) SECOND
VISCOSITY FUEL OIL.
FUEL SUPPLY LINE
The oil supply line from the oil storage tank to the
appliance should be of an approved and suitable
pipe with a minimum internal diameter of 9mm
(3/8”), using the flexible oil line supplied, as the final
connection to the pump.
Oil supply pipes are normally run in annealed cop-
per tube complying to E.N. 1057. It can be obtained
in coil or half hard form for use with bending
machines. This pipe can also be obtained with pro-
tective plastic sheathing applied. Fittings for copper
pipe should be of the flared manipulative type to
B.S. 864: Part 2. Steel pipes complying with B.S.
1387, if used, must be protected from corrosion.
Galvanised pipe and fittings must not be used.
Screwed joints must only be made with taper
threads complying to B.S. 1740: Part 1.
Jointing materials must be of types intended for use
with oil fuel. Special petroleum - resisting com-
pounds and PTFE tape are suitable. External pipes
should preferably be run with a continuous rise
towards the direction of flow, so that air can be vent-
ed off. It is important to avoid high points which
could cause air locks.
Exposed lengths of oil supply pipe must be properly
supported by purpose made clips securely fixed in
place. Metal clips formed so as to hold the pipe on
to a saddle are preferred. Consideration should be
given to avoiding routes which expose the pipe to
severe chilling which could cause freezing of the oil.
Where pipes are buried, they must be protected from
accidental damage. The use of joints underground
should be avoided if at all possible. If joints have to
be fitted in pipes laid below ground, access to them
must be provided.
An oil filter (5 -10 micron) and stop valve must be fit-
ted to the fuel feed line and located near the supply
tank and facilities should be provided to enable it to
be serviced without draining down the oil supply sys-
tem. (See Figs. 20, 21, 22 & 23).
At the point where the oil line enters the building, the
oil line must be fitted with an approved remote act-
ing fire valve e.g. Teddington KBB, which meets the
requirements of B.S. 5410 : Part 1, fitted with the
appropriate length of capillary. The heat sensoring
phial of the fire valve must be fitted to the clip provid-
ed in the burner compartment. It is absolutely
essential that the fire valve is located externally and
is as close as possible to the appliance. For existing
installations where the oil supply is built into the
structure internally, the remote acting fire valve
should be fitted where the oil supply line is first
exposed internally. This type of layout is not recom-
mended for new installations.
When gravity feed is used (the most common) the
minimum head should not be below 1m (3’3”) and
the maximum head should not exceed 6.5m (21’ 3”).
NOTE:
The pump is factory set for a single pipe
installation.
Single pipe supply system: Tanks servicing this
appliance by means of a single pipe need to be posi-
itioned so that they will apply the minimum head
required 1 meter (3’ 3”) of oil to the burner when the
fuel level is at its lowest point.
Fig.20