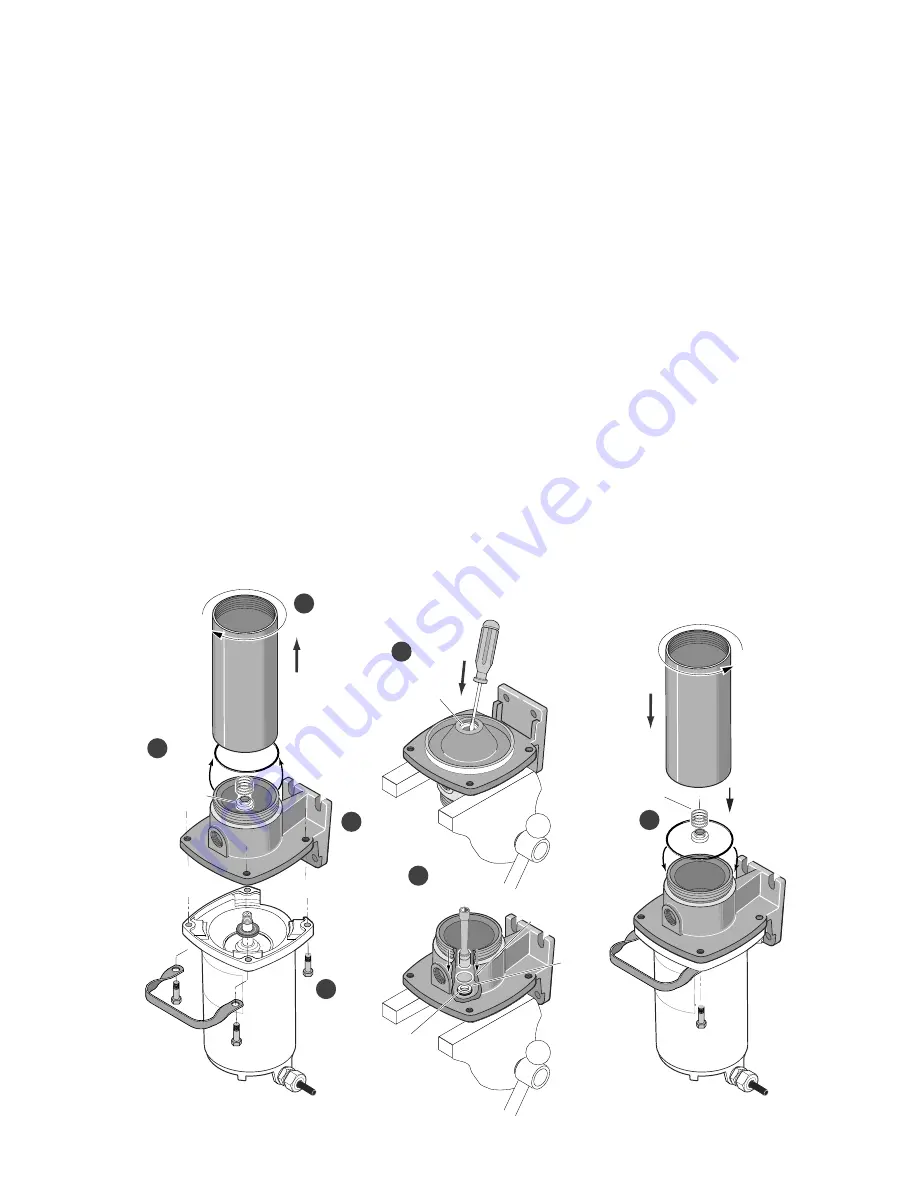
9
Mechanical Seal Changeout
(refer to Figures 7 and 8)
This procedure is best completed with the pump held in
a vertical position, motor down.
First complete
“Disassembly”
instructions 1 through 5
under
“Impeller Stack Changeout.”
(see Figure 7).
6. Remove 4 capscrews holding pump body to motor.
Pump handle will come off with top capscrews.
7. Unscrew pump shell from pump body, turning
clockwise (left hand threads).
8. Remove mechanical shaft seal spring and rotating
half from motor shaft. Use care not to scratch motor
shaft when removing rotating half.
9. Remove pump body from motor and place on flat
surface, face down. Again, use care not to scratch
motor shaft.
10. Use a screwdriver to push ceramic seat out from
seal cavity as shown.
11. Installation of ceramic seat:
A. Turn pump body over so seal cavity is up; clean
cavity thoroughly.
B. Clean polished surface of ceramic seat with a
clean cloth.
C. Lubricate outside rubber surface of seat with
soapy water. Place cardboard washer over
polished face of seat and press into seal cavity
using a 3/4” socket or a piece of 3/4” standard
pipe.
D. Be sure polished surface of seat is free of dirt
and has not been damaged by insertion. Re-
move excess soapy water. Dispose of card-
board washer.
12. Installation of rotating half and spring:
A. Reinstall pump body on motor using extreme
caution not to hit ceramic portion of seal on
motor shaft. Reattach pump body to motor using
capscrews. Be sure to reinstall pump handle at
this time.
B. Inspect shaft to make sure that it is clean.
C. Clean face of rotating half of seal with a clean
cloth.
D. Lubricate inside diameter of rotating half with
soapy water and slide onto motor shaft (sealing
face first).
E. Place spring over motor shaft so it rests on
rotating half.
13. To complete reassembly from this point, reverse
instructions 1 through 5 under
“Impeller Stack
Changeout.”
NOTICE:
Lubricate suction and discharge O-Rings
with soapy water for easier installation of shell.
Ceramic Seat
3/4" pipe or
3/4" socket
with extender
Polished
Face
Rotating
Half
Cardboard
washer (supplied
w/seal)
Rotating Half
of Mechanical
Seal
Remove shell;
turn clockwise.
Push ceramic
seat out of
pump body
Remove
Pump Body
6
8
7
9
10
11
12
1212 0894
Figure 8 – Mechanical seal changeout.