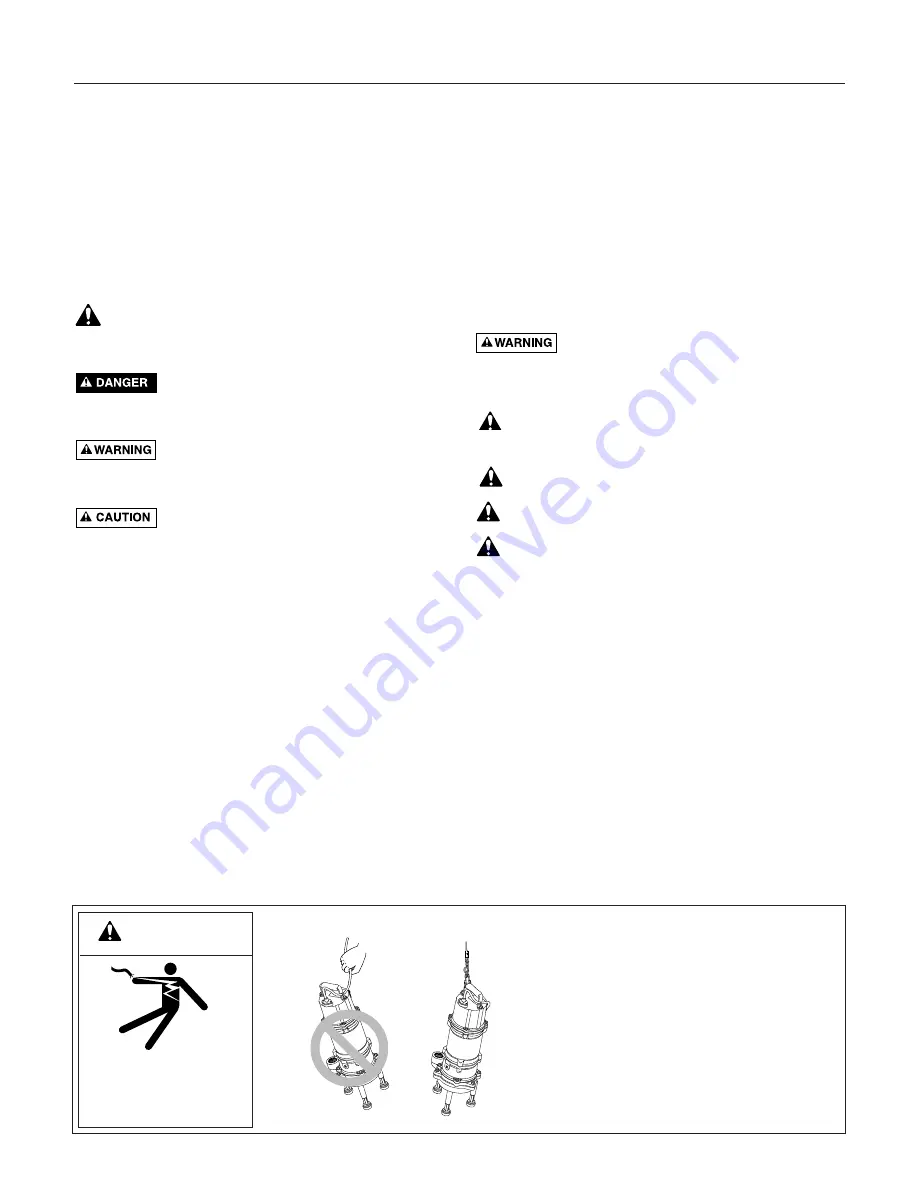
Safety
2
UNPACKING AND INSPECTION
Handle with care. Check the items received against the
packing list to be sure that all equipment has been
received. Inspect the pump for shipping damage. If any is
found, file a claim with the carrier immediately.
GENERAL SAFETY INFORMATION
READ AND FOLLOW
SAFETY INSTRUCTIONS!
This is the safety alert symbol. When you see this
symbol on your pump or in this manual, look for
one of the following signal words and be alert to the
potential for personal injury.
Warns about hazards that
will
cause seri-
ous personal injury, death, or major property damage if
ignored.
Warns about hazards that
can
cause serious
personal injury, death, or major property damage if
ignored.
Warns about hazards that
will
or
can
cause
minor personal injury or property damage if ignored.
NOTE:
Indicates special instructions which are important
but not related to hazards.
NOTE:
Install the pump in the vertical position only.
Installing the pump in any other position will void the
warranty.
NOTE:
This unit is not designed for applications involving
salt water or brine! Use with salt water or brine will void
warranty.
1. To avoid serious injury and/or property damage, read
these rules and instructions carefully.
2. Check your local codes before installing. You must
comply with their rules.
3. Vent any sewage or septic tank according to local
codes.
4. Do not install the pump in any location classified as
hazardous by National Electrical Code, ANSI/NFPA
70-1984.
5. The pump can run hot. To avoid burns when servic-
ing the pump, allow it to cool for 20 minutes after
shut-down before handling it.
6. Do not run the pump dry. Dry running can overheat
the pump and will void the warranty.
7. The pump is permanently lubricated. Check the oil
level in the seal plate periodically. Check for water in
the oil in the seal plate. See instructions under
"Operation/Lubrication”, Page 4.
Hazardous voltage. Can shock, burn, or kill.
During operation the pump is in water. To avoid fatal
shock, proceed as follows if the pump needs servicing:
Electrically ground the pump to a suitable ground
such as a grounded water pipe, a properly ground-
ed metallic raceway, or a ground wire system.
Do not remove cord or strain relief.
Do not connect conduit to pump.
Do not lift the pump by the power cord (See ‘Cord
Lift Warning’, below).
A. Ground the pump according to all applicable codes
and ordinances.
B. Disconnect the power to the outlet box or circuit
breaker before servicing.
C. To reduce the risk of electric shock, take care when
changing fuses or resetting the circuit breaker. Do not
stand in water when working on the control box or
with the circuit breaker.
D. This pump is intended for permanent connection only.
Provide a strain relief at the control box for the power
supply cord connection to box. All control compo-
nents must be UL or CSA listed and suitable for end
use application. Only qualified personnel should
install the pump and associated control equipment.
Risk of electrical shock and fire.
1. Attempting to lift or support the pump by
the power cord can damage cord and cord
connections, expose bare wires, and cause
a fire or electrical shock.
4. Use handle on top of pump for all lifting or
lowering of pump. Disconnect the power to
the pump before doing any work on it or
attempting to remove it from the pit.
3. Lifting or supporting the pump by the power
cord will void the warranty.
Risk of electrical shock.
Can burn or kill.
Do not lift pump by
power cord.
WARNING
CORD LIFT WARNING