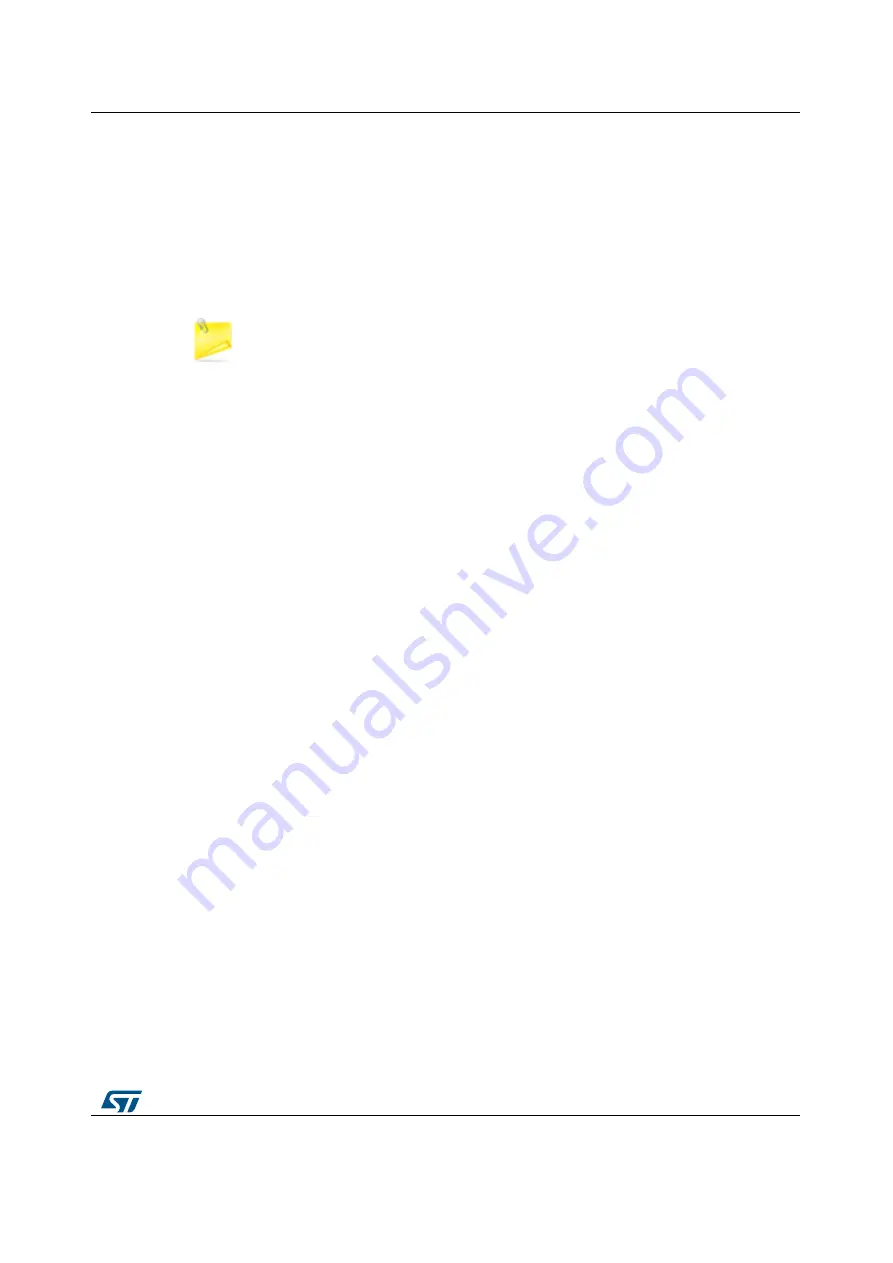
UM2082
Getting started
DocID029504 Rev 1
7/14
2.3.1
Hardware connections and equipment
A suitable external power supply or external battery for the stepper motor used,
connected between J1 connector pin 5 (Vin) and pin6 (ground)
A secondary supply from one of the following sources:
An external power supply providing 3.3 V (recommended), connected between
TP3 (+VDD) and TP1 (ground).
If a secondary power supply is not available, you can connect the VDD net to the
Vin supply voltage by adding the R2 resistor (not mounted by default); in this
configuration, Vin must be lower than 5 V.
In both cases, the R4 resistor must be replaced with a 10 kΩ resistor
(recommended value) for a VDD below 2.5 V.
A waveform generator providing the signal step clock, connected between TP4 (CLK
test point) and TP1 (GND); refer to the STSPIN220 datasheet for amplitude and
frequency limits
Stepper motor connect to J1 motor phase connector (A+, A-, B+, B-).
2.3.2
Operating mode
You can adjust the following parameters:
Step mode
: set the desired step mode via the S1, S2, S3 and S4 switches (refer to
the step mode selection table in the STSPIN220 datasheet)
Motor torque
(according motor requirements): using the R35 trimmer, you can set the
voltage value at REF input of STSPIN220 (the maximum value is 0.5 V with VDD =
3.3 V).
Motor speed
: you can change this parameter through the step clock signal frequency.