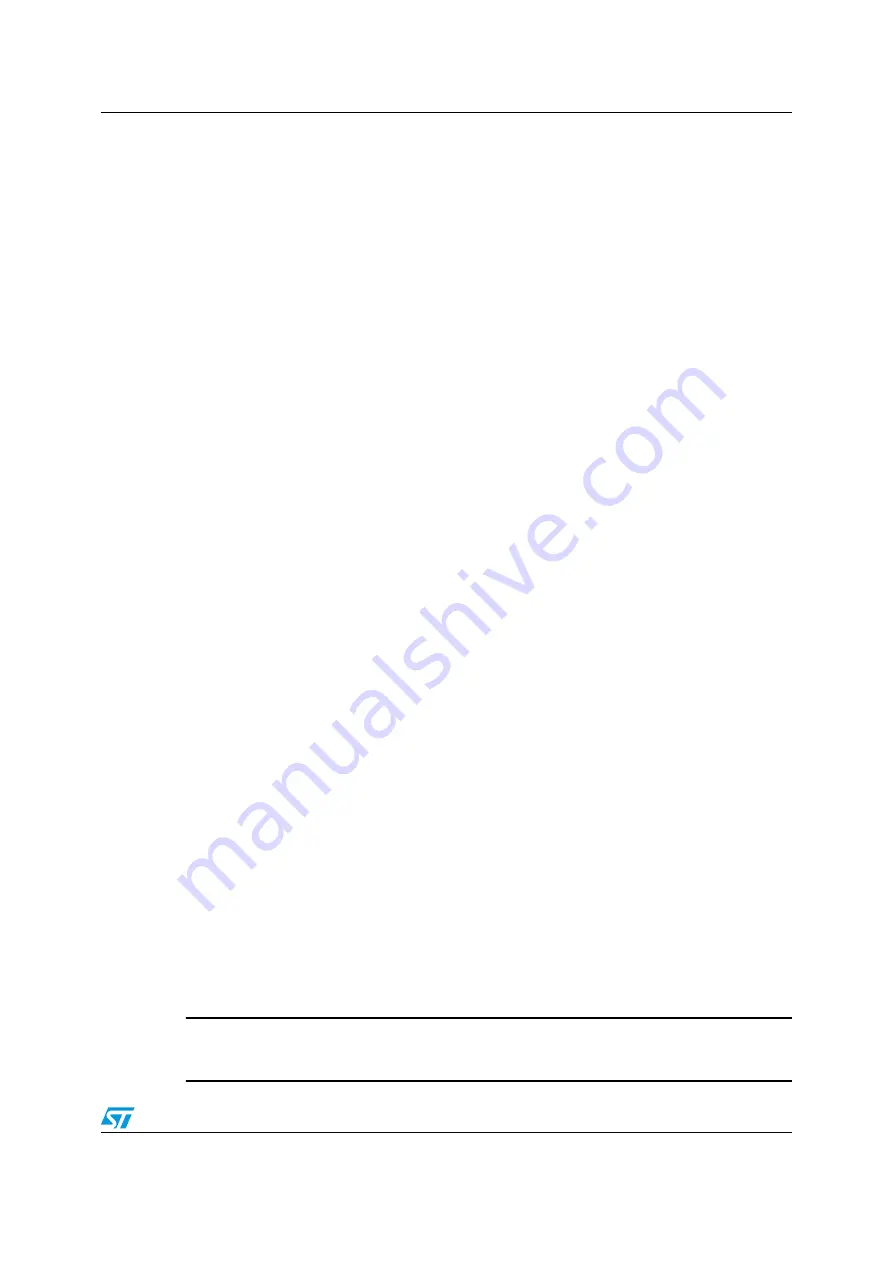
UM0933
Safety and operating instructions
Doc ID 17386 Rev 1
11/16
In
the electronic schematic of the control board is depicted.
●
Three basic blocks can be identified in the schematic of the welding machine control
board:
–
Analog amplification and computation block based on the TSM102
–
PWM generator based on the SG3525
–
Welding current dynamic reference based on discrete components
The analog amplification and computation block are based on the TSM102. This chip has
two operation amplifiers, two voltage comparators, and a voltage reference inside. The
operational amplifiers are used to implement an analog current control made up of a PID
and an integrator. The working principle is well described and explained in the application
note dedicated to the welding machine system (see AN3200;
2.5 kW MMA welding
machine)
.
One of the two amplifiers is used to implement the error amplifier for the current control. A
voltage representative of the output welding current is subtracted to a voltage level
representative of the wanted target current level. The error signal is amplified and
represents the PWM level to be set as the control variable to the power converter.
This is a standard PID control.
The measurement of the output current is obtained by an indirect estimation. By measuring
only the peak current on the primary side of the power insulation transformer, information on
the peak current at the output is obtained, following the relation between the primary and
secondary turn number on the windings.
To obtain information regarding the mean current on the load, information regarding the
current ripple on the output inductor is required. This information can be obtained by
acquiring the voltage reflected to the output inductor and integrating this information. (For a
more detailed explanation and mathematical model see the AN3200 application note
dedicated to the MMA welding machine. The last block is dedicated to giving the right target
to the current control, according to the MMA process status. In particular, two trimmers can
be found on the control board. The welding current setup trimmer and the short-circuit
current setup trimmer. The trimmer dedicated to setting the welding current is also
replicated on the power board in order to be free to solder three wires, and to position the
trimmer on the front panel of the welding machine for easy setting during the work.
The second trimmer, is dedicated to setting the maximum current wanted to force on the
output in case of a short-circuit condition.
Normally, in case of a short-circuit, the current is set to a higher value in order to fuse, as
soon as possible, the cause of the short-circuit, therefore avoiding the rod sticking to the
metal piece being welded. This behavior is totally automatic and dynamic, thanks to the
signal from the optocoupler previously mentioned. In the case of a short-circuit lasting for
more than 2 seconds, the circuit limits the current on the output to a small value, allowing
the operator to remove the rod and restart the plasma operation welding. This function can
be disabled if some laboratory tests must be carried out without taking into account the right
output voltage generated by the system. Connecting pins 15 or 16 of connector J12 to
ground the SC_Detection signal is also fixed to ground. In this condition it is simulating that
the voltage at the output of the welding machine is at the right level.
Warning:
In this case no kind of short-circuit protection or duty cycle
limitation is present.
www.BDTIC.com/ST