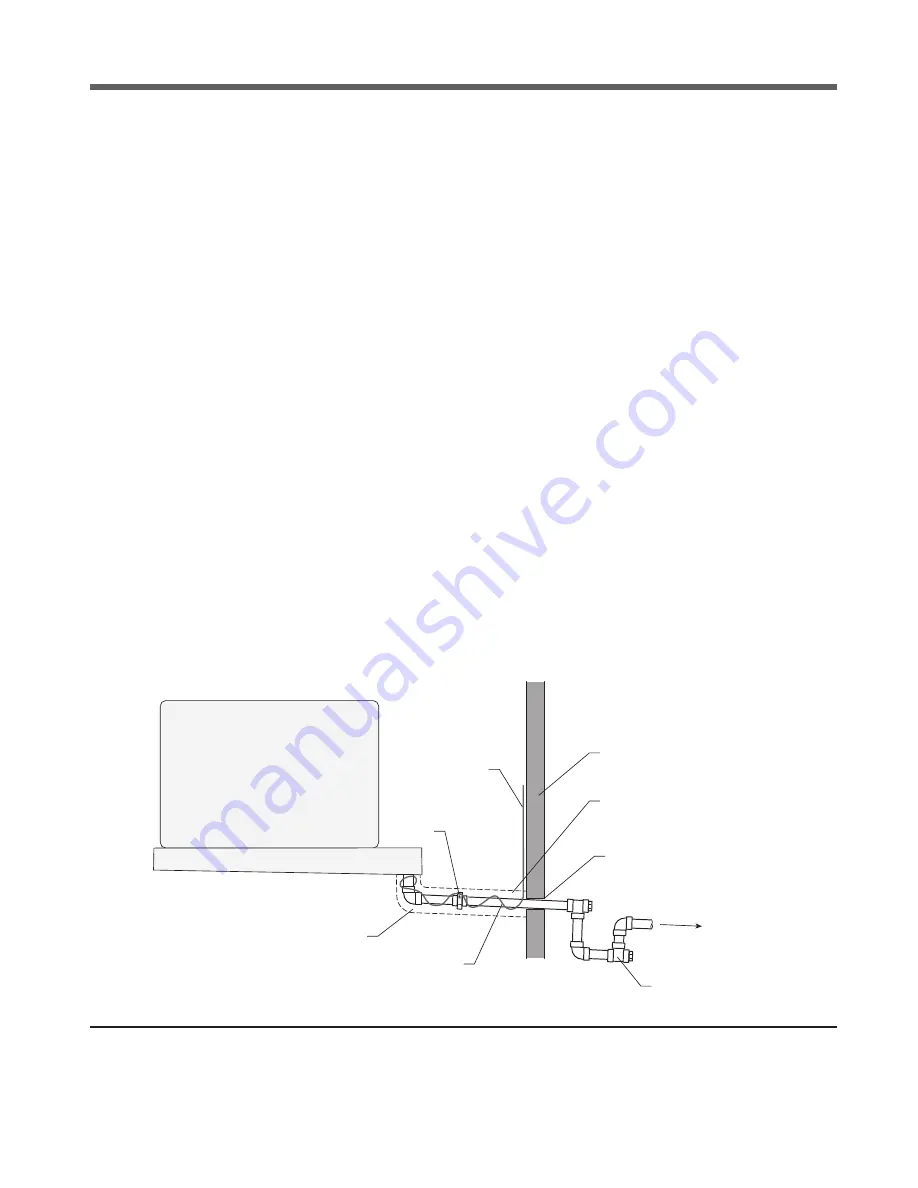
6
FIGURE 2
Drain Line
installation
5 REFRIGERANT WARNING
The use of any refrigerant can be dangerous under certain
conditions. Where people or product can be exposed to hazardous
conditions, daily inspections should be made for the detection
of any defect or malfunction that could cause the escape of the
refrigerant and cause harm. In the case of halocarbon refrigerants,
electronic detection devices are available for sensing the presence
of such refrigerants in the atmosphere.
Ammonia
is a “self-alarming” gas with its strong odor but detection
devices are strongly recommended. People and product are a
concern based on the concentration levels (ppm) of ammonia
along with OSHA and EPA regulations. An ammonia gas detection
device connected to an external alarm system to warn that a
leak is occurring is recommended. Refer to local codes and Fire
Department for additional local regulations.
Only experienced, qualified personnel should install, operate, and
maintain detection and alarm equipment.
6 PIPING INSTALLATION
6.1 DRAIN LINE
The drain line should be connected to both drain pans, and should
be as short and as steeply pitched as possible with a minimum
of ¼” drop per running foot. The drain line should be the same
size, or one size larger then drain pan connections. A drain line
trap should be installed to prevent warm moist air from migrating
through the drain line. The trap should be located in the warmest
and/or lowest section of the piping to avoid freezing and provide
sufficient liquid head for flow through the trap. If the temperature
surrounding the drain line is below freezing (32°F) it must be
wrapped with a drain line heater and insulation. Be sure to also wrap
the drain pan coupling. The drain line heater should be energized
continuously, but to avoid the possibility of overheating heat tape
manufacturers recommend a thermostat be installed. Be sure to
follow the manufacturer’s recommendations. The drain line trap
should be outside of the freezing space. See Figure 2.
A union at the drain pan connection is recommended for future
servicing. The union should be located outside the edge of the
drain pan so that when the pan is lowered for cleaning or repair the
drain line run is not in the way. Use two wrenches when tightening
to prevent the drain fitting from twisting and damaging the drain
pan. See Figure 3.
Long runs of drain line, i.e. more than a few feet, should be supported
by hangers to avoid damage to the drain pan. For cleaning and
inspecting the drain, tees with plugs are recommended instead
of elbows.
Insulated
Wall
Evaporator
Drain pan
Heating cable
power line
Drain line wrapped
with insulating material
Thermostatically controlled
heating cable
Union
Vapor seal the
pipe penetration
4" to 6"
drain trap
with access
Condensate
drain line
Slope drain pipe down
and away from evaporator
(1/4" per foot of pipe)