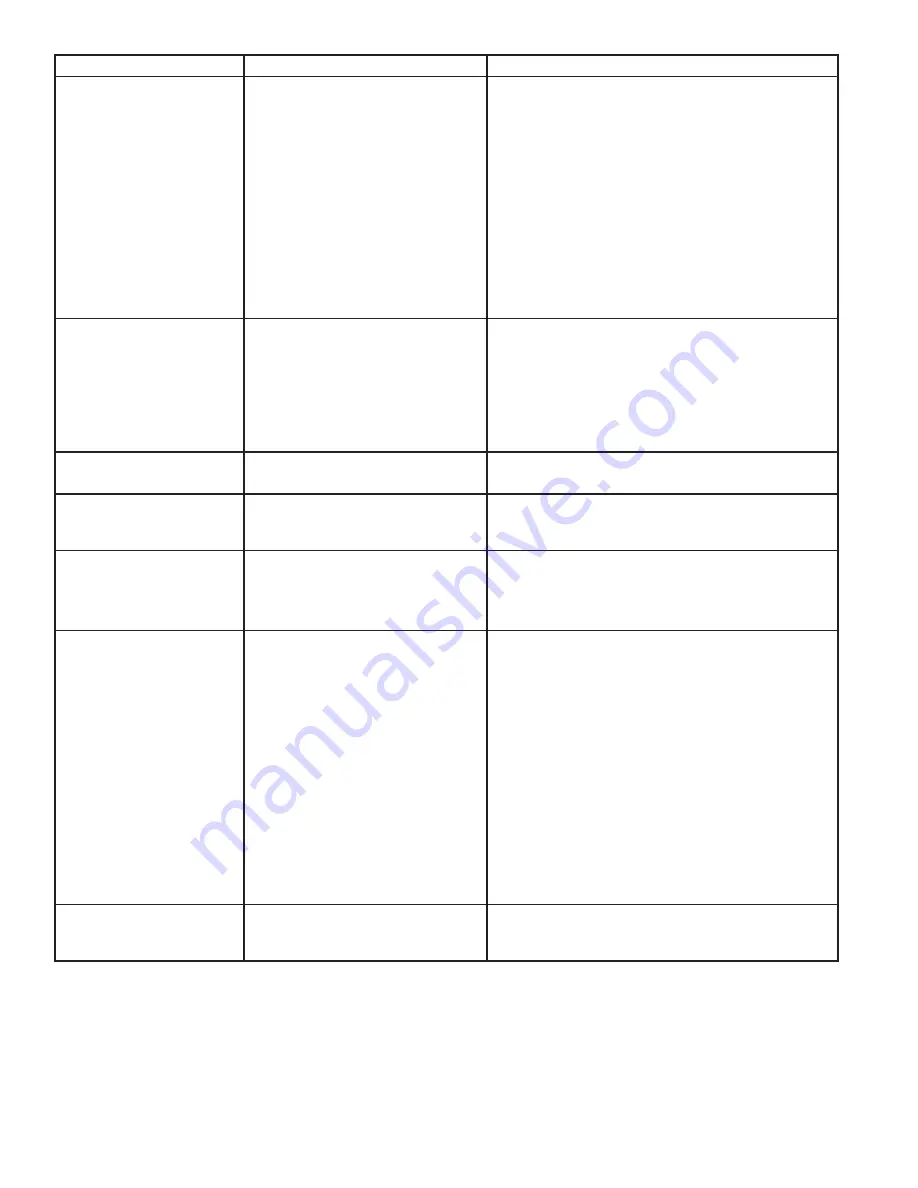
32
SYMPTOM
POSSIBLE CAUSE(S)
CORRECTIVE ACTION
Outlet Dew Point Alarm
Left Tower or Right Tower
1. Inlet air flow higher than the sizing
condition.
2. Liquids entering the dryer inlet.
3. Inlet air temperature higher than the
sizing condition.
4. Desiccant dusting.
5. Contaminated desiccant (e.g. with oil).
6. Heater temperature set too low.
7. Heating malfunction due to heater
failure or heater contactor failure.
1. Reduce inlet flow to sizing condition.
2. Check the inlet air line for liquids. Inspect prefilter and
drain valve. Clean, repair or replace automatic drain valve.
3. Check the compressor aftercooler and cooling system.
Reduce inlet air temperature to sizing condition.
4. Check air pressure, airflow and airflow surges and correct
as necessary. Replace desiccant.
5. Check prefilter and automatic drain valve. Replace prefilter
element. Clean, repair or replace drain valve as necessary.
Consult factory concerning need for desiccant replacement.
6. Adjust controller set point.
7. Replace heater or heater contactor.
High Humidity Alarm
Left Tower or Right Tower
1. Desiccant bed overloaded.
2. Dew point sensor or monitor damaged
or defective.
3. Loss of desiccant drying capacity
1. Check inlet air flow rate, temperature and pressure. Higher
than design flow, and temperature, and lower than design
pressure will result in overloading of the dryer.
2. Examine sensor for physical damage and check monitor/
sensor operation. Replace sensor or monitor as necessary.
3. Inlet air improperly filtered causing desiccant contamination
- examine filter elements and drains. Repair or replace as
necessary. Useful life of desiccant has been exceeded.
Heater Over-Temperature
Alarm
1. Insufficient purge gas flow.
2. Temperature sensor failure.
1. Check for purge blockage, temperature sensor failure, etc.
2. Repair and replace as required.
Heater Low-Temperature
Alarm
1. Heating malfunction due to heater
failure or heater contactor failure.
2. Temperature sensor failure.
1. Replace heater or heater contactor.
2. Repair and replace as required.
Energy Management Under-
Range Alarm
or
Energy Management Over-
Range Alarm
1. Energy Management sensor failure.
1. Check circuit for continuity. Repair or replace as neces-
sary.
Blower Motor Overload Alarm
1. Restricted or blocked purge air flow.
2. Line failure
1a. Dirty intake filter on blower - examine filter element and
clean or replace.
1b. Regenerating tower purge exhaust valve failed to open -
1) Check for loss of pilot air - ensure manual drain valve on
bottom of pilot air filter is fully closed, ensure pilot air filter
cartridge is not clogged, ensure pilot air shut-off valve is
open.
2) Check for purge pilot air solenoid valve failure. Check valve
operation. Repair or replace as necessary.
3) Check for regenerating tower Purge Exhaust Valve failure -
examine valve and actuator for damage. Repair or replace
as necessary.
1c. Purge exhaust piping obstructed - ensure piping is free of
obstructions.
1d. Regenerating tower purge check valve failed to open - ex-
amine valve internals. Repair or replace as necessary.
2. Check voltages and currents in the motor circuit.
Heater High Inlet Temperature
(models 3200, 3600, & 4300
only)
1. On-line tower purge check valve is
leaking.
2. Temperature sensor failure.
1. Examine valve internals. Repair or replace as required.
2. Repair and replace as required.
Содержание Pneumatic Products IBP Series
Страница 50: ......