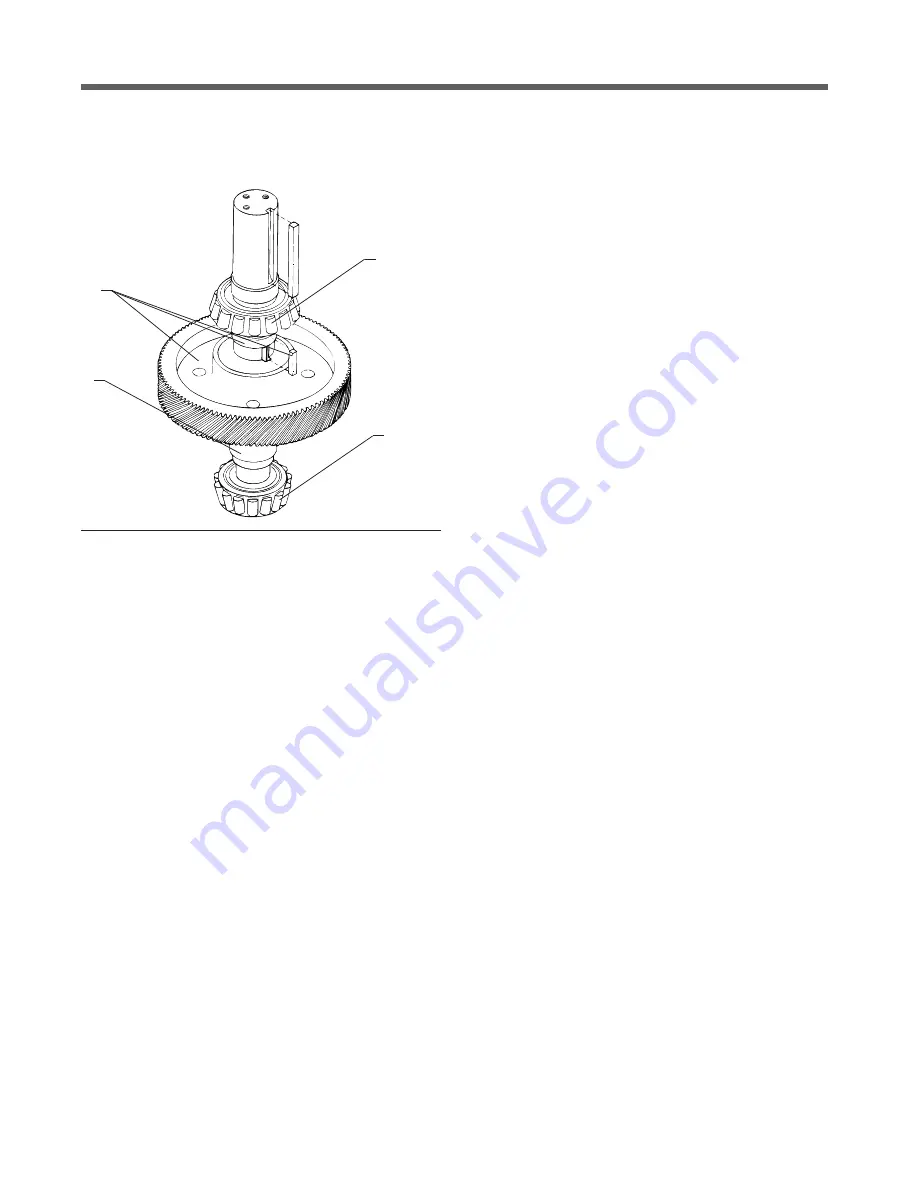
15
Figure 13
Fan Shaft Assembly
1
2
field repair
Fan Shaft Assembly
Part numbers and references—refer to
Figures 3, 4 and 13.
1. Install key (306) and press helical gear (201) on fan shaft.
2. Install lower bearing spacer (40) on fan shaft.
3. Press bottom bearing cone (421) onto fan shaft.
4. Press upper bearing cone (422) on fan shaft.
Model 34.4 – Install water slinger spacer (307) on top of
bearing cone.
5. Install lower fan shaft bearing cup (421) into Geareducer
case (not illustrated).
6. Install upper fan shaft bearing cup (422) into Geareducer
case cover (not illustrated).
Final Assembly–3400 Series
Part numbers and references—refer to
Figures 3 and 14.
1. Install O-ring (702) onto pinion cage subassembly.
2. Bolt pinion cage subassembly to case using proper number
of shims to give indicated pinion setting distance which is
etched on front face of pinion gear. See Figure 10. Tighten
to 75 ft·lbƒ (102 N·m) torque.
3
4
3. Lower fan shaft and interstage shaft subassemblies into case
simultaneously. Engage marked spiral bevel ring gear teeth
with marked spiral bevel pinion tooth. The gear and pinion
are match-marked when lapped and must be assembled the
same way. The ring gear has the end of two teeth marked
“X” and the pinion has one tooth so marked— the gears
should be engaged with the X-marked pinion tooth between
those marked on the ring gear. Match mark location can be
checked through the inspection opening.
4. Apply a coat of Permatex® Form-a-Gasket No. 2 to surface
of Geareducer case which mates with case cover. Lower
case cover subassembly onto case, piloting both shaft
subassemblies into their respective bores.
5. Install dowel pins (20) to align bearing bores. Fasten
case cover to case with cap screws tightening to 75 ft·lbƒ
(102 N·m) torque.
6. Position top interstage cap shims (500) and install interstage
bearing cap with place bolts tightening to 85-90 ft·lbƒ (116-
122 N·m) torque.
7. Adjust shims to give proper backlash—.007–.009" normal
(.178–.228mm)—between spiral bevel gears. See Gear
Setting Procedure, page 18.
8. Fan shaft bearing must be preloaded to .001–.003" (.025–
.076mm) in the following manner:
a–Install labyrinth ring with sufficient quantity of shims (500)
to insure axial bearing endplay exists.
b–Mount a dial indicator to measure axial movement of fan
shaft. Support indicator stand on the cover or interstage
cap adjacent to fan shaft and position indicator to read on
machined top surface of fan shaft
c–Rotate the fan shaft slowly in one direction until all down-
ward movement stops. Rotation is necessary to align the
bearing rollers and seat roller ends on cone lip. Record the
dial indicator reading or zero the indicator.
d–Move shaft in the opposite axial direction by attaching to
the shaft with a swivel joint and hoist or by turning Geareducer
over, allowing the weight of the shaft assembly to seat the
bearings. If a hoist is used, the lifting force should be 800 lb
(363 kg) to sufficiently overcome the weight of the fan shaft
assembly. Rotate the shaft slowly in one direction until all axial
movement stops. Record the dial indicator reading.
e–The difference in dial indicator readings (steps c and d)
is the initial fan shaft bearing end play. In order to achieve
➠