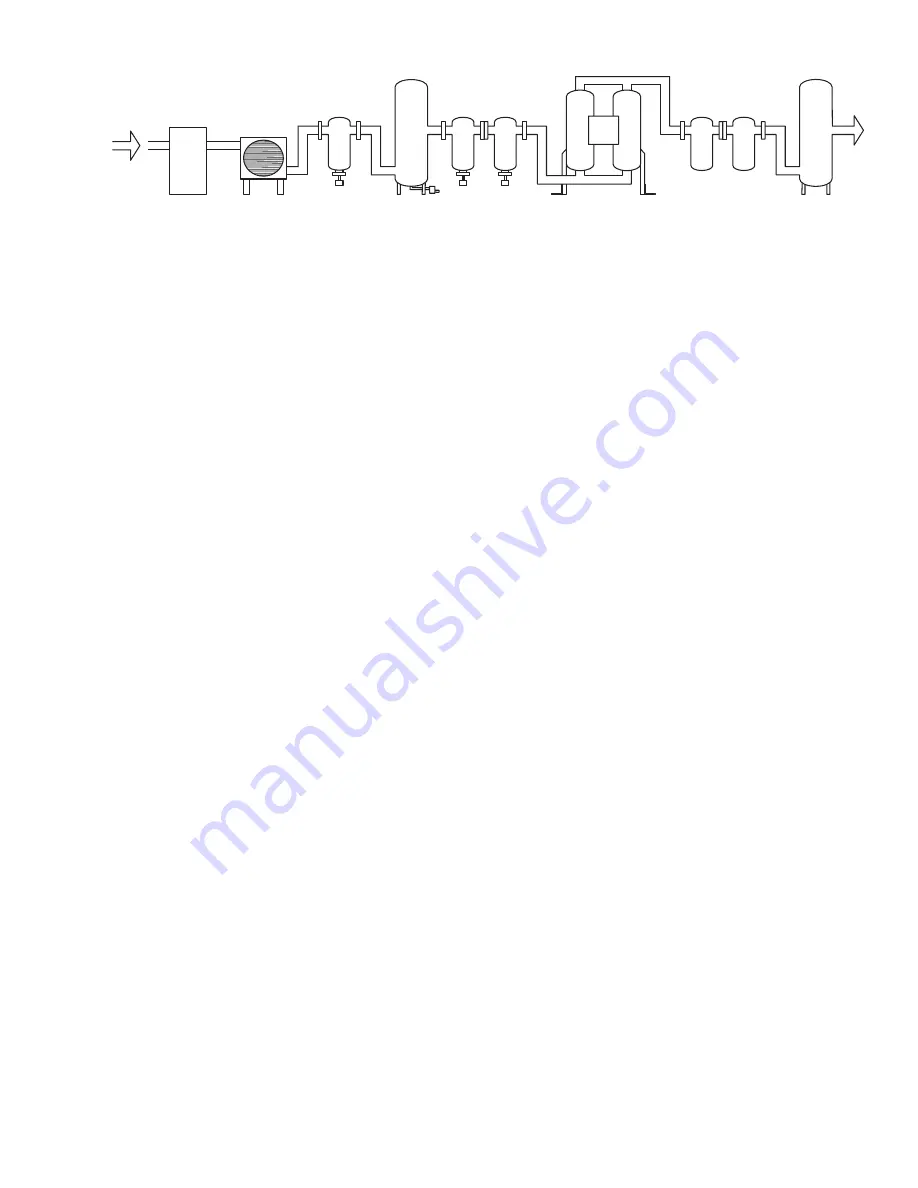
3
4.3 Location and Clearance
Install the dryer on a level pad. Ensure the dryer is level
by grouting or shimming as necessary. Holes are provided
in the dryer base members for floor anchors. Securely
anchor the dryer frame to the floor. Allow 24 inches clear
-
ance on all sides of the dryer for servicing. Provide ad-
equate clearance for prefilter element, afterfilter element
and heater element replacement. Provide protection for
the dryer if it is installed where heavy vehicles or similar
portable equipment is likely to cause damage.
4.4 Piping and Connections
All external piping must be supplied by the user unless
otherwise specified. Refer to Figures 2 for connection
sizes. Inlet and outlet isolation valves and a vent valve
are recommended so the dryer can be isolated and
depressurized for servicing. The connections and pipe
fittings must be rated for or exceed the maximum operat
-
ing pressure given on the dryer nameplate and must be in
accordance with industry-wide codes. Be sure all piping is
supported. Do not allow the weight of any piping to bear
on the dryer or filters. Piping should be the same size as
or larger than the dryer connection. Piping smaller than
the dryer connections will cause high pressure drop and
reduce drying capacity.
If the purge exhaust piping must be extended outside the
dryer area, choose a combination of diameters, lengths,
and turns that limits the additional pressure drop to 1/4
psid or less.
BACK PRESSURE WILL CAUSE DRYER
MALFUNCTION.
Consult the factory for piping details
if required.
WARNING — Do not operate dryer without installed
mufflers. Exhausting compressed air directly to
atmosphere will result in noise levels above OSHA
permissible levels and rapidly expanding gas could
potentially cause harm to persons or property.
Dryer bypass piping may be installed to allow uninter-
rupted airflow during servicing. If the downstream appli
-
cation cannot tolerate unprocessed air for short periods,
install a second dryer in the bypass line.
Compressor
Aftercooler
Separator
Receiver
Prefilters
Afterfilters
Receiver
Desiccant Dryer
Figure 1
Typical System Configuration
CAUTION — Do not hydrostatically test the piping
with the dryer in the system. The desiccant will be
damaged if saturated with water.
4.5 Electrical Connections
WARNING — These procedures require entering
gaining access to the dryer’s electrical enclosure(s).
All electrical work must be performed by a qualified
electrical technician.
Connect the proper power supply to the dryer according
to the electrical drawings which accompany this manual.
Be sure to follow all applicable electrical codes.
NOTE:
A disconnect switch is not provided as standard
equipment and therefore, must be supplied by the cus-
tomer.
Dry contacts (voltage free) are provided in the low ten-
sion electrical enclosure for a remote alarm. The contact
ratings are shown on the electrical drawing.
Connections to voltage-free common alarm contacts with
a minimum 5-amp rating can be made at terminals TB4-1
through 3.
• Terminal TB4-3 is the common alarm connection.
• Terminal TB4-1 is the N.O.. (normally open) contact
connection.
• Terminal TB4-2 is the N.C. (normally closed) contact
connection.
• The alarm relay coil is energized when power is sup
-
plied to the controller input terminals and there is no
alarms.
• The coil is de-energized when power is removed or
when an alarm condition exists.
• The common alarm is designed to activate on:
a) either a dryer fault condition or a service reminder,
or b) a dryer fault condition. This is user selectable.
• For the common alarm to activate on either a dryer
fault condition or a service reminder, the jumper at
JP6 is removed. This is the default configuration.
Содержание HPD Series
Страница 46: ......