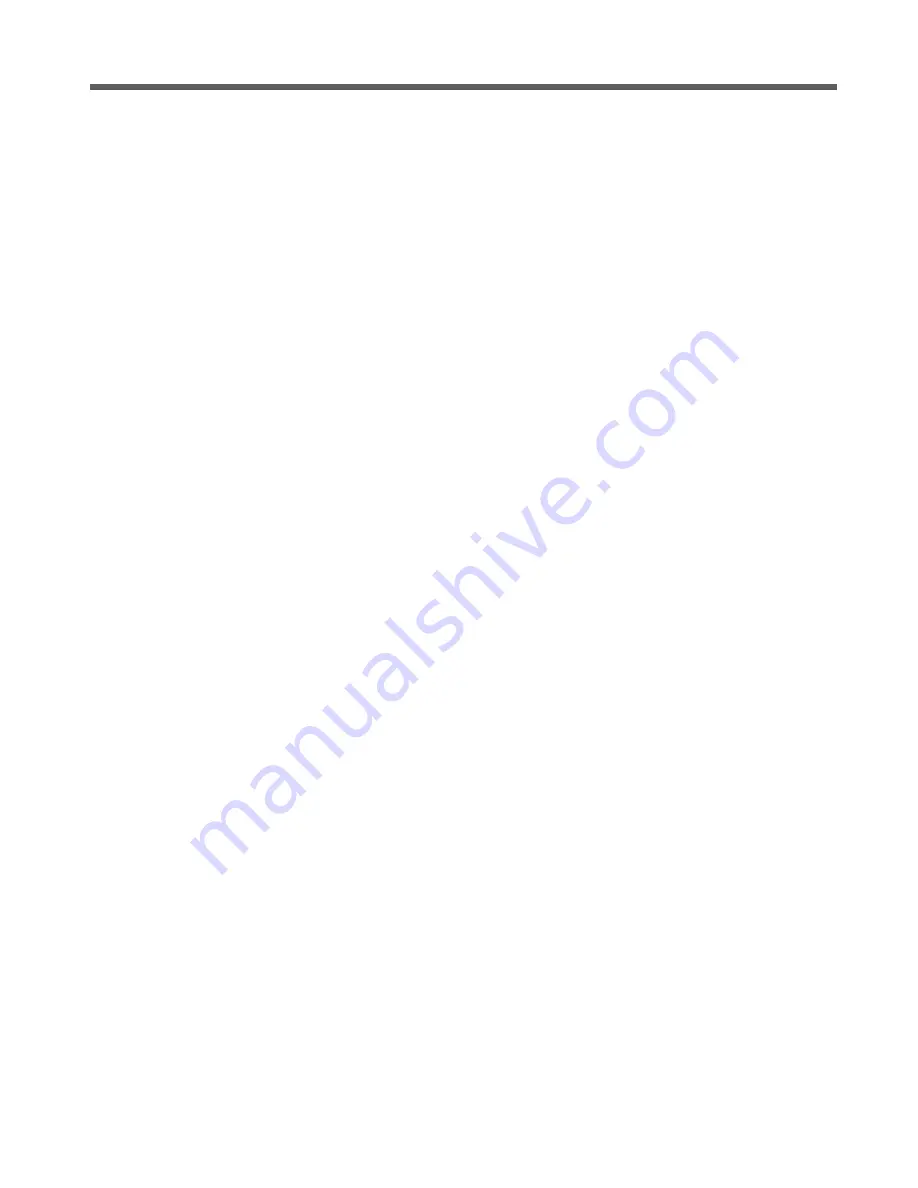
8
field repair
General
Geareducers can be repaired in the field—however, major repairs
require the use of a fully equipped machine shop. When field repair
or replacement of parts is necessary, the following procedure is
recommended for the disassembly and assembly of the unit. If any
O-ring, oil seal or gasket is to be reused, care should be taken
not to damage it during disassembly. Parts which contain O-rings
or seals should not be jerked or twisted past a shoulder or edge.
These parts are marked with an asterisk (*) in the description
below. O-rings, oil seal and gaskets should be carefully inspected
for damage before being reinstalled. Always use new O-rings and
oil seal during a major overhaul.
Disassembly
Part numbers and references—refer to Figure 2 and 3.
1. Remove drain plug and drain oil.
2. Remove outer ring of bolts in pinion cage cap and remove
pinion subassembly*.
Note
—The thickness of the shim pack (320) is important in reset-
ting the gears. The shim pack should either be saved or carefully
measured with a micrometer. If the gears are to be replaced, record
the pinion setting distance that is etched on the pinion gear.
3. Remove water slinger*.
4. Turn case upside down and remove bearing retainer cap* and
shim pack (
420
).
Note
—The thickness of this shim pack is important in the back-
lash setting of the gears. The shim pack should either be saved
or carefully measured with a micrometer.
5. Remove bottom cap and fan shaft assembly.
6. Turn Geareducer case right side up and remove bearing retainer
and shim pack (
420
).
Note
—The thickness of this shim pack is important in setting the
fan shaft bearing endplay. This pack should be saved or carefully
measured with a micrometer.
7. Remove bearing cups (
411
and
412
) from the bottom cap and
Geareducer case using a soft metal punch or mallet.
8.
For "S" Models Only:
Remove fan shaft lip seal (
520
) from
upper bearing retainer, and sleeve (
521
) from water slinger.
Pinion Cage Disassembly
1. Remove pinion cage cap* from pinion cage.
2. Remove O-rings* (
504
and
505
).
3. Remove locknuts and lockwasher (
103
and
104
) then press
pinion shaft (
101
) out of pinion cage. This will free tail bear-
ing cone (
312
). A hydraulic press or jack is recommended for
removing or assembling press fit parts.
4. Press oil slinger*, O-rings* (
301
and
506
), and head bearing
cone (
311
) from the pinion shaft. Bearings must not be exposed
to dirt, dust or moisture.
5. Press bearing cups (
311
and
312
) out of pinion cage.
Fan Shaft Disassembly
1. Remove ring gear (
101
) from the ring gear hub (
8
).
2. Press ring gear hub and lower bearing cone (
411
) off of the
fan shaft (
201
).
3. Remove lower fan shaft key (
202
).
4. Press the top bearing cone (
412
) off of the shaft.
Assembly
Before assembling a new pinion gear in the pinion cage, check
match numbers on pinion gear and spiral bevel ring gear to be
certain that they are a matched set. Gears are lapped in matched
sets at the factory and should not be separated. Numbers are
etched on both the pinion and ring gear as illustrated in
Figure 4
.
All parts that are to be reused should be thoroughly cleaned before
being reinstalled. Do not remove new bearings from packaging
until ready to use. Clean all bearings (new or used). Do not spin
dry bearings. Take each bearing set and roll the cup on the cone
to note any roughness. Replace bearing if necessary. If bearings
cannot be installed immediately after cleaning, lubricate and cover
to protect against dust, moisture, etc.
If a press is not available to install bearing cones, they can be
heated as long as the temperature does not exceed 275°-300°F
(135°-149°C). If the bearings get hotter than this, they will begin
to draw and soften. Bearings can be heated with infrared lamps
or with oil baths. If an oil bath is used, the bearing should be sup-
ported an inch or so above the pan to prevent local overheating.
Содержание Marley Geareducer 2200
Страница 2: ......