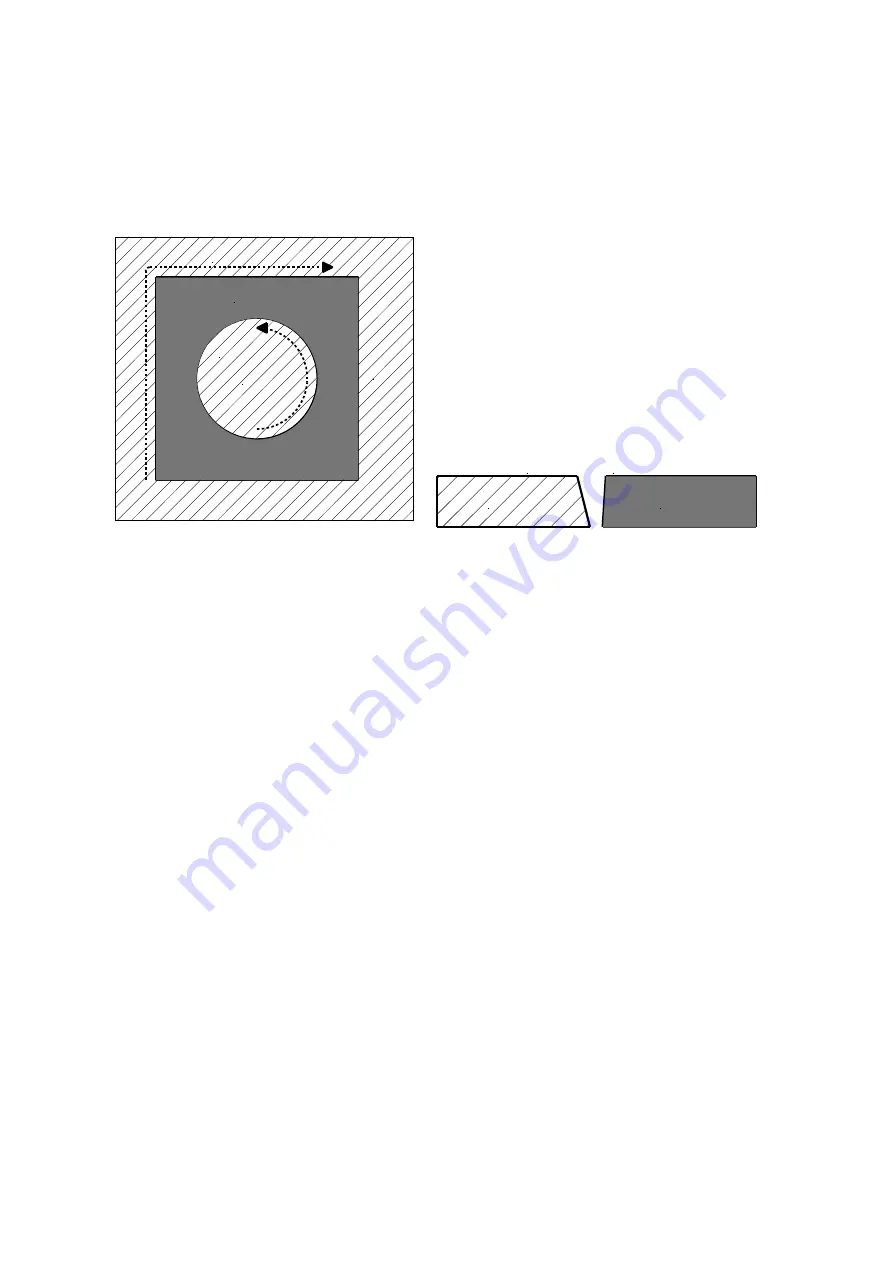
27
Wrong cutting direction. The plasma is rotating and as a result there is more angle on
one side than the other. Make sure that the machine is properly programmed so that
the bigger angle is on the scrap side of the cut.
Correct cutting direction
Scrap
Scrap
Cut part
Clockwise
C-Clockwise
Scrap
Part
Right side
Left side
Too high cutting speed. By cutting slower the angle can be straightened.
Too high amperage for the material thickness. Choose different cutting parameters.
Inconsequent angle deviation
Worn or damaged consumables. Check and exchange worn or damaged parts.
The torch is not perpendicular in relation to the work piece. Check the torch alignment
and adjust if necessary.
Magnetic remanence in the material. Materials that are handled with magnetic lifting
devices can become magnetic. The plasma arc may be attracted or repelled by the
magnetism. Make sure that the material is not magnetic.
Slag adherence
Slag free cuts requires that all the parameters for the cutting process are optimized.
Slag adherence as a result of too low cutting speed.
This slag arises when the cutting speed is too low. The slag is excessive and porous. It
can however easily be removed. By increasing the cutting speed the slag can be
minimized.
Slag adherence as a result of too high cutting speed.
This slag arises when the cutting speed is too high. The slag looks like drops of molten
metal and is difficult to remove. By lowering the cutting speed the slag can be
minimized. If that does not remove the slag it may help to lower the torch distance to
the work piece.
Содержание SPARCIN 4000
Страница 25: ...25 TORCH DIMENSIONS X Cut 400...