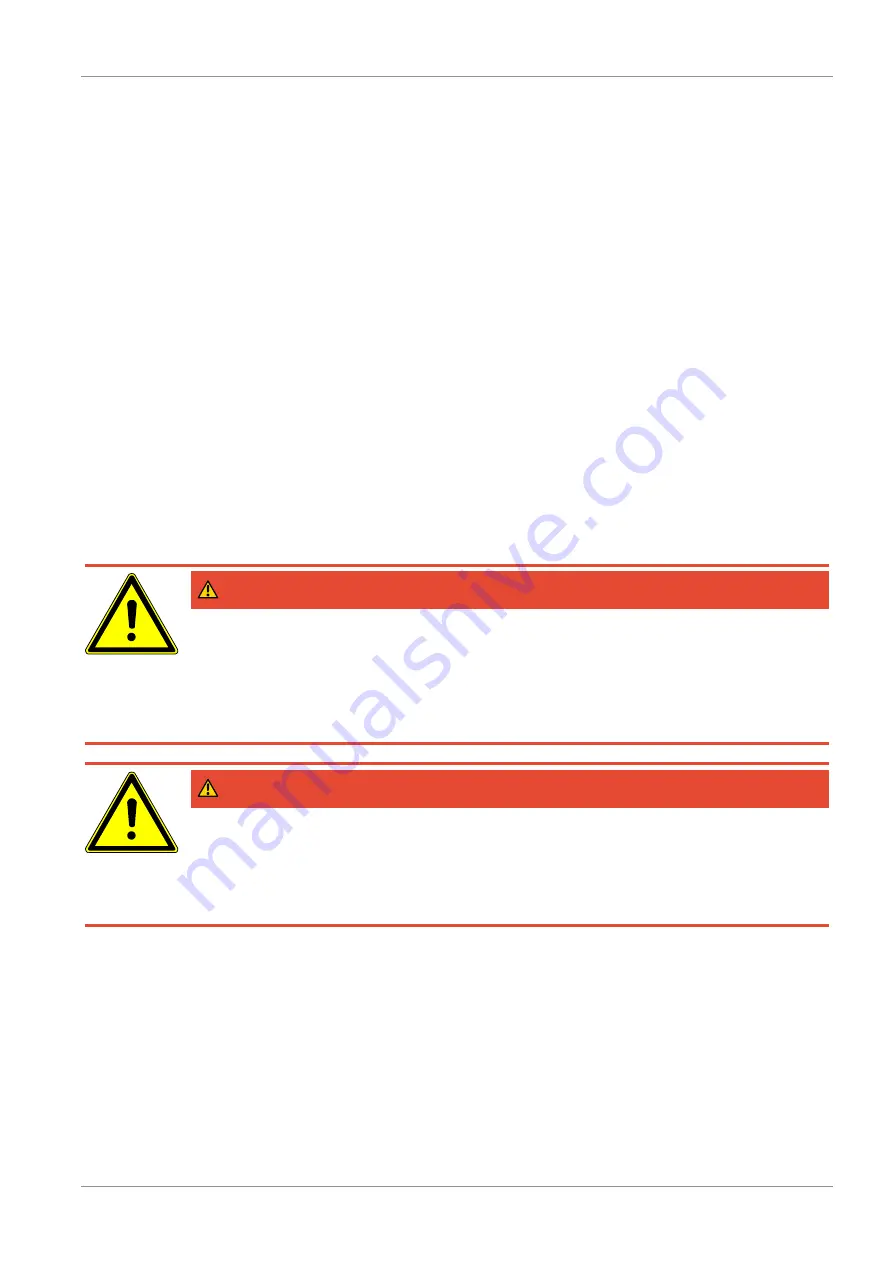
Spectron Gas Control Systems GmbH
Commissioning | 6
GES_BE56-2U-VCR_1020
19
6.2.2 Flushing in the process gas to the process
Flushing in the entire line network to the consumer must be implemented via a waste gas valve
on the process. To do this, refer to the system documentation for the consumer. This procedure
does not apply to fluorine or fluorine mixtures.
1. Close all valves and fully depressurise the pressure regulator by turning the handwheel anti-
clockwise as far as it will go.
2. Open the process gas source valve and then the HPI and PLI valves, to fill the entire area in
which the process gas is to penetrate up to the process and fill it (pressure build-up).
3. First slowly set the pressure regulator step by step to a low outlet pressure.
In this process, the process source pressure and the gas type properties are to be taken
into account.
4. Open shut-off valve on the process. Ensure that the process gas can be discharged safely
via the process.
The pressure control panel is now in a condition ready for operation.
If operation is not to be continued following the flushing process, the pressure regulatur must be
fully depressurised. This is carried out by turning the handwheel anti-clockwise as far as it will
go.
When system operation is then started, set the pressure regulator step by step to the required
outlet pressure.
6.2.3 Passivation and flushing for fluorine mixtures
DANGER
Fluorine mixtures
Fluorine mixtures are extremely toxic and corrosive gases. Heavy reactions may occur if fluorine
mixtures are applied to non-passivated surfaces or in combination with (air) humidity.
a) If the fittings are used for gas mixtures with a fluorine content of up to 10%, the purging and
passivation regulations must be strictly observed.
b) Do not use for gas mixtures with a fluorine content > 10%.
DANGER
Passivation
During passivation, local heating occurs as a result of the chemical reaction taking place.
a) Before passivation, the entire gas-wetted surface must be flushed with purge gas!
b) The temperature of the armatures must be monitored throughout the process. It may not ex-
ceed 50°C.
The passivation must be carried out in stages. In the first stage, the fluorine content may not ex-
ceed 1%. In the further stages, the concentration may be increased by a maximum of 1% in
each stage. Overall, this passivation must consist of at least 3 stages.
If the entire system is filled after the first stage, the gas mixture must remain in the system at
about 1 bar for at least 12 hours.
The entire system must then be purged and the next stage can be introduced.
When the concentration corresponds to the process gas and the last stage is completed, the
outlet pressure can be slowly increased to the required process gas pressure.