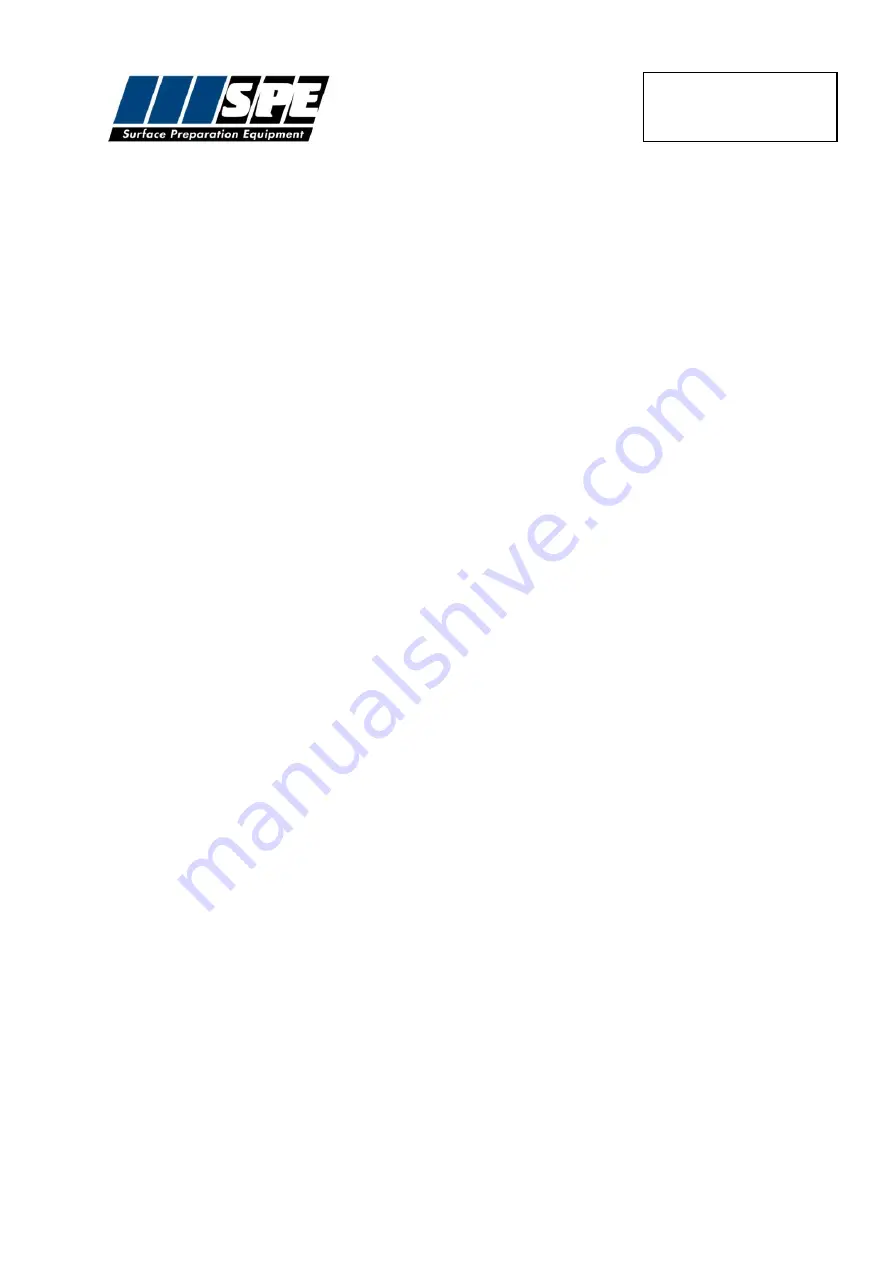
BEF320-1A
Operating Manual
MAINTENANCE
PRIOR TO ANY MAINTENANCE OR ADJUSTMENT ISOLATE POWER SUPPLY AND
STOP EQUIPMENT
After use:
Clean the machine to remove all build up of dust and surface residues. If using a
hose pipe or pressure washer take care that water is not directed onto electrical components
and switches.
Note:
Motors and switches are not waterproof
Drum Removal:
Remove bolts on side plate and then screw two bolts back into the two tapped holes in the side
plate. Continue winding in and this will push side plate off dowel pins. Pull off side plate,
remove key from shaft. Pull out cutting drum. Fitting a new cutter head is simply a reversal of
the above procedure, a little care must be taken to align the drive shaft, cutter drum and
support end drive bush.
EXCESSIVE FORCE SHOULD NOT BE NEEDED TO REFIT THE CUTTER DRUM.
Cutter Drum Maintenance:
When changing cutter drum always check that the flail shafts are not worn with pronounced
grooves and also that the centres of cutters and spacers are not elongated and beginning to
"mushroom". The drum assembly is hitting concrete with great force 650 times every minute!
Expenditure on consumables must be expected and built into all job costing.
While changing the drum the condition of the drive shaft and side plate bearings should be
checked. If any roughness, side play or leakage of grease is detected then new bearings
should be fitted. Lightly oiling the drive shaft will prevent a build up of rust which could cause
difficulty when changing the drum. At the same time check belt tension and condition also
checking the pulley grooves are clean and undamaged.
The drive shaft is manufactured from high quality steel to produce the special properties
required. The shaft is extremely strong and virtually unbreakable when used as intended. If
however sideways pressure is exerted on the shaft while it is not supported by the side plate
bearing it can be bent.
With the drum removed check that the vacuum port is free from blockages and that the dust
skirts are in good condition.
Remove all build up and deposits of material from the under side of the drum housing. On
certain applications, e.g. the removal of damp self levelling compounds, it may be necessary
to clean away deposits hourly! Failure to do so could result in overload of the drum assembly,
drive motor and drive belts
Cont’d
……
4
Содержание BEF320-1A
Страница 13: ......
Страница 14: ......
Страница 15: ......
Страница 16: ...BEF320 1A Operating Manual 13 ...
Страница 17: ......
Страница 18: ......
Страница 19: ......
Страница 20: ......
Страница 21: ......
Страница 22: ......
Страница 23: ......
Страница 24: ......
Страница 25: ......
Страница 27: ......