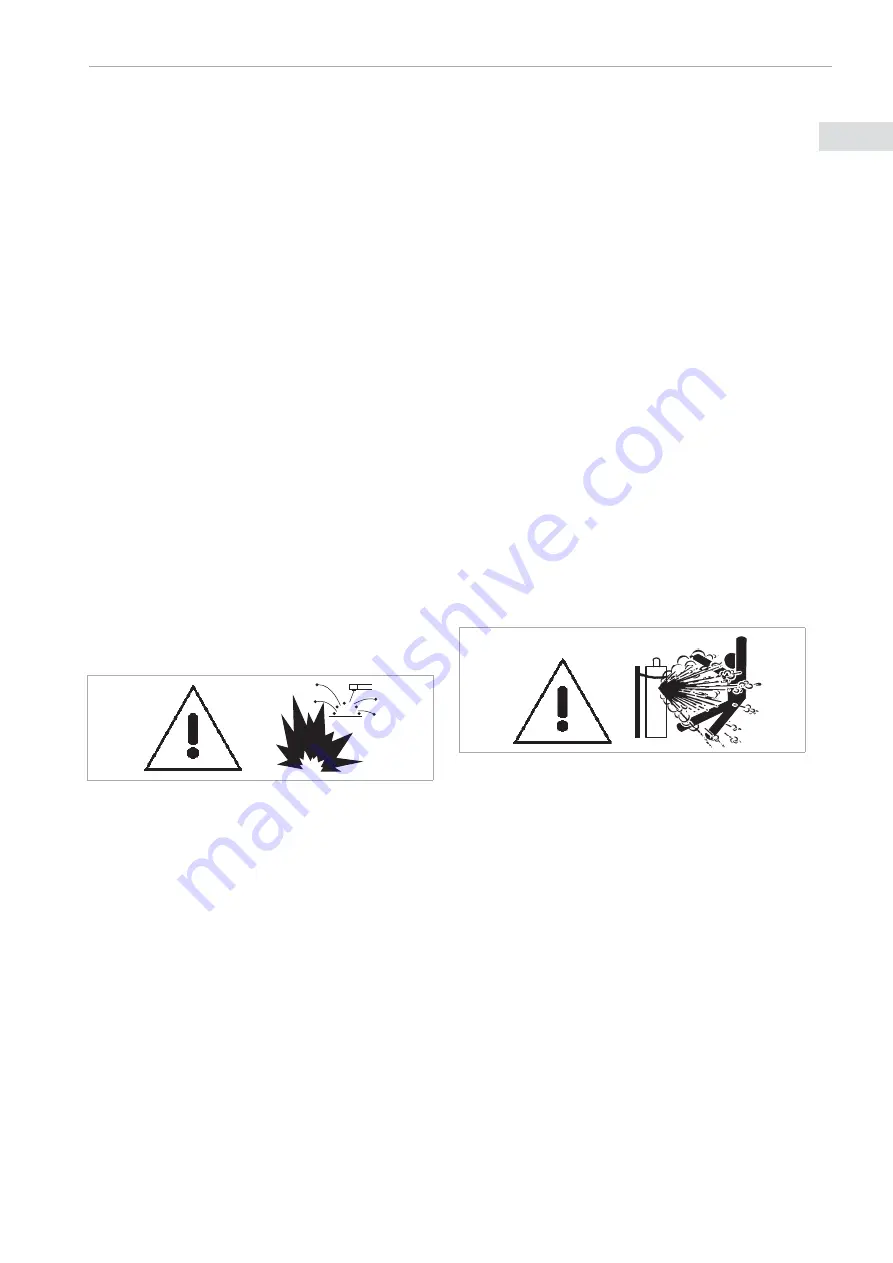
In case of doubt, checks by an expert should
be made to establish noise levels in any
particular environment, and, if these are
in excess of the prescribed limit, one of the
following alternatives may apply:
a) Insulation of the noise source as far as
possible, e.g. by
fi
tting silencers or sound
proof enclosures
b) Insulation of the operator from the noise
source
c) E
ff
ective maintenance of sound protection
devices
d) Indication as „ear protection areas” where
applicable
e) Restriction of entry to these „ear protection
areas” to authorized persons.
f) Protect your hearing with appropriate
personal protection measures, e.g. earplugs
or hearing protectors.
1.6. FIRE AND EXPLOSION
Arc welding and allied processes can cause
fi
re and explosions and precautions should
be taken to prevent these hazards.
1.6.1. FIRE
•
Before setting to perform welding
operations, ensure that elements involving
fi
re hazard are removed from the zone
where welding operations are to be
performed. If this is impossible, protect
all
fl
ammable elements against the impact
of sparks. Remember that sparks and hot
metal may penetrate through small cracks
and openings into the adjacent area.
• Avoid welding in the vicinity of hydraulic
conduits.
• The welding arc throws sparks and splatters
out. Welders should wear clean and dry
protective clothing (staining with oil should
be avoided in particular) such as welding
gloves, welder’s apron, welder’s trousers,
welder’s boots, protective hood/cap, etc.
• When no welding operations are carried
out, make sure no part of the electrode is
in contact with the material to be welded
or chassis ground. Accidental contact may
lead to overheating and create a
fi
re hazard.
• An extinguisher should always be ready
for use and available in an easily accessible
place nearby.
• The surroundings of the work should be
observed for an adequate period after its
termination.
•
„Hot spots” and their immediate
surroundings should be observed until
their temperature has dropped to normal.
1.6.2. EXPLOSION
• It is forbidden to heat up, cut or weld tanks,
barrels or containers that contained toxic
or
fl
ammable materials. For there is an
explosion hazard, even if the containers
have been emptied and cleaned.
1.6.3. USE OF CYLINDERS WITH SHIELDING
GAS
• In case compressed gases are used in the
work place, apply special safety measures
to prevent dangerous situations.
• Use gas cylinders with appropriate
shielding gas, foreseen for a particular
process. Additional equipment (pressure
regulator, hoses, connectors) should be in
good technical condition. A gas cylinder
and accessories should have the required
valid attestations and approvals for use.
• Gas cylinders should always be stored in
vertical position,
fi
xed to an undercarriage
or permanent support.
• Gas cylinders should be placed far away
from areas, where they could be exposed
to the risk of being overthrown or su
ff
ering
physical damage.
• Ensure gas cylinders are at a safe distance
7
SPARTUS
®
Easy MIG * USER’S MANUAL
ENG
ENG
Содержание EasyMIG 220E PULSE SYNERGY
Страница 1: ......
Страница 2: ......
Страница 29: ...29 SPARTUS Easy MIG USER S MANUAL ENG ENG...
Страница 30: ...30 SPARTUS Easy MIG USER S MANUAL ENG ENG...
Страница 31: ......
Страница 32: ......