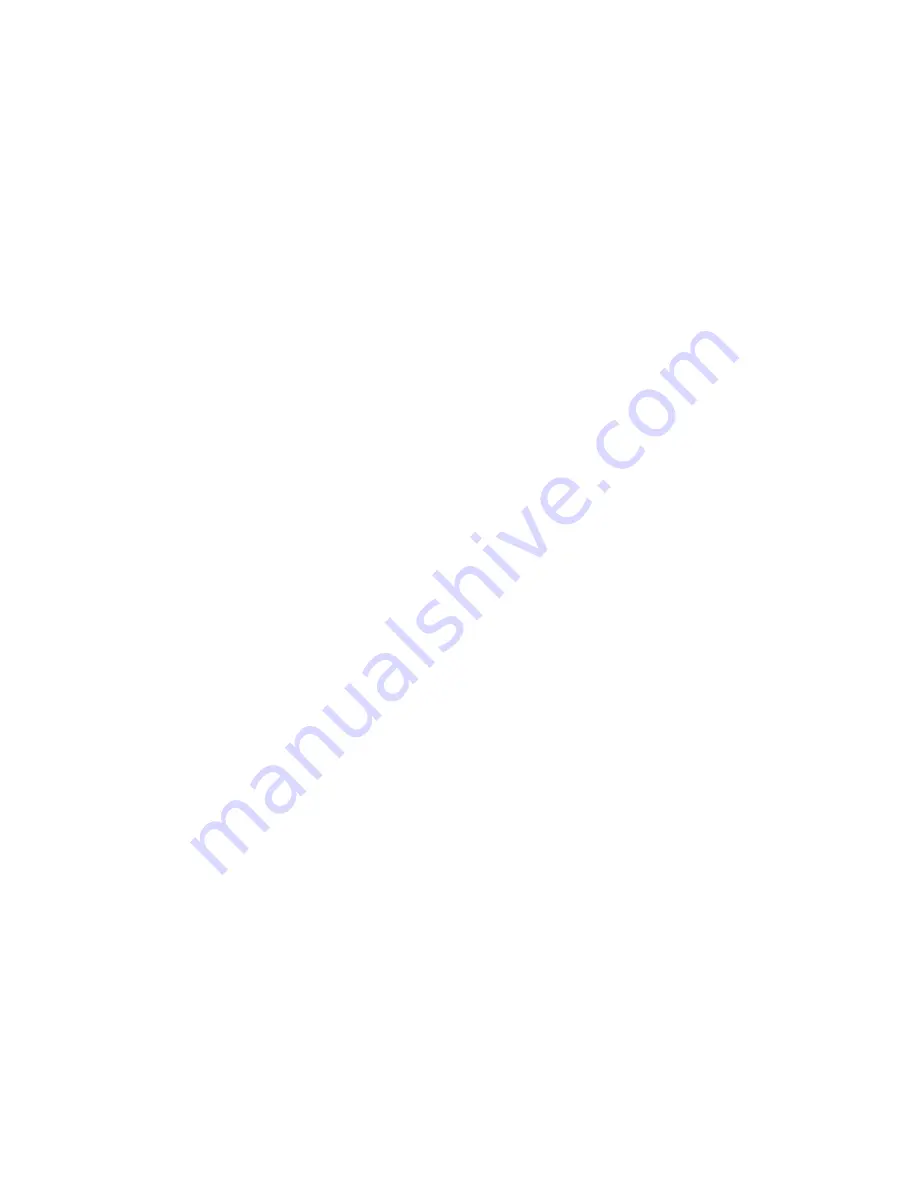
17
Air Tightness
While the air receiver tank is pressurized to at least 120 psi and the compressor is switched off, listen for any audible air
leaks. Squirt soapy water around any suspect joint and watch for bubbles indicating a leak. De-pressurize the air
receiver tank carefully and all connected air hoses and/or air piping before commencing any repairs.
Disassemble the leaking joint and clean off all traces of thread tape or sealant using a wire brush. Apply PTFE thread
tape or Loctite™ 243 liquid sealant to the male threaded connection before reassembling and tightening the joint. Allow
approximately 30 minutes for the liquid sealant to cure, if used. Re-pressurize the air receiver tank and check that the
air leak has been rectified before putting the unit back into normal operation.
Lubricating Oil
Maintain the oil level at the top of the red circle on the oil sight glass fitted to the compressor pump.
Remove the oil fill cap to add oil only when the compressor is switched off.
Use premium quality engine oil with an API Service Classification of at least CG or SH, or alternatively use specialized
air compressor oil meeting DIN 51506 specification. Select an oil of monograde or multigrade viscosity that is appropriate
for the ambient temperature in which the compressor will be operating.
The compressor pump has been filled at the factory with SAE 15W-40 mineral based engine oil that is suitable for
ambient temperatures from −15°C (5°F) to over 40°C (104°F). Mineral based, semisynthetic or fully synthetic oils may
be used, but different types of oils should not be mixed together. Regular oil changes in accordance with the
recommended maintenance schedule are crucial to the service life of the compressor pump.
To change the oil, remove the oil fill cap and then remove the oil drain plug. Another way is to simply evacuate the oil
through the oil fill hole by inserting a suction probe. Oil flows easier if the pump is warm, but do not touch the oil in case it
is hot. Reinstall the oil drain plug tightly before adding the new oil and then finally screw the oil fill cap back in place.
If the oil changes to a white colour, this indicates water contamination. If it changes to a dark colour, this typically
indicates compressor overheating. Change the oil immediately in either case. Do not pollute the environment by
improper or illegal disposal of waste oil. New or rebuilt compressor pumps will discharge higher than normal amounts of
oil until the piston rings are seated in, which can take approximately 100 operating hours. Some oil may also
concurrently accumulate at the crankcase breather openings and this too will diminish with run time.
TROUBLESHOOTING
Before performing any inspection, test or repair work on the compressor, switch off the unit, tag and lock out the power
supply, and carefully release all air pressure from the receiver tank, air hoses and/or air piping.
Please refer to the troubleshooting guide shown in Table 5 for assistance with diagnosing and repairing any problem that
might occur with your air compressor. Whilst many of the tasks can be undertaken by a mechanically proficient person
with access to proper tools, all electrical work must by undertaken by a licensed electrician.
It is recommended for your convenience and expedience that the troubleshooting guide is consulted prior to contacting
advice.
Use only genuine spare parts for maintenance and repair of the compressor to ensure its safe and reliable operation.
For best results, the following repair procedures should always be observed:
Use only genuine spare parts for maintenance and repair of the compressor to ensure its safe and reliable operation.
•
Use new gaskets, seals and O-rings during reassembly.
•
Use PTFE thread tape or Loctite™ sealant on threaded joints subject to pressure.
•
Use Loctite™ retaining compound when fitting engine or motor pulleys onto their drive shafts.